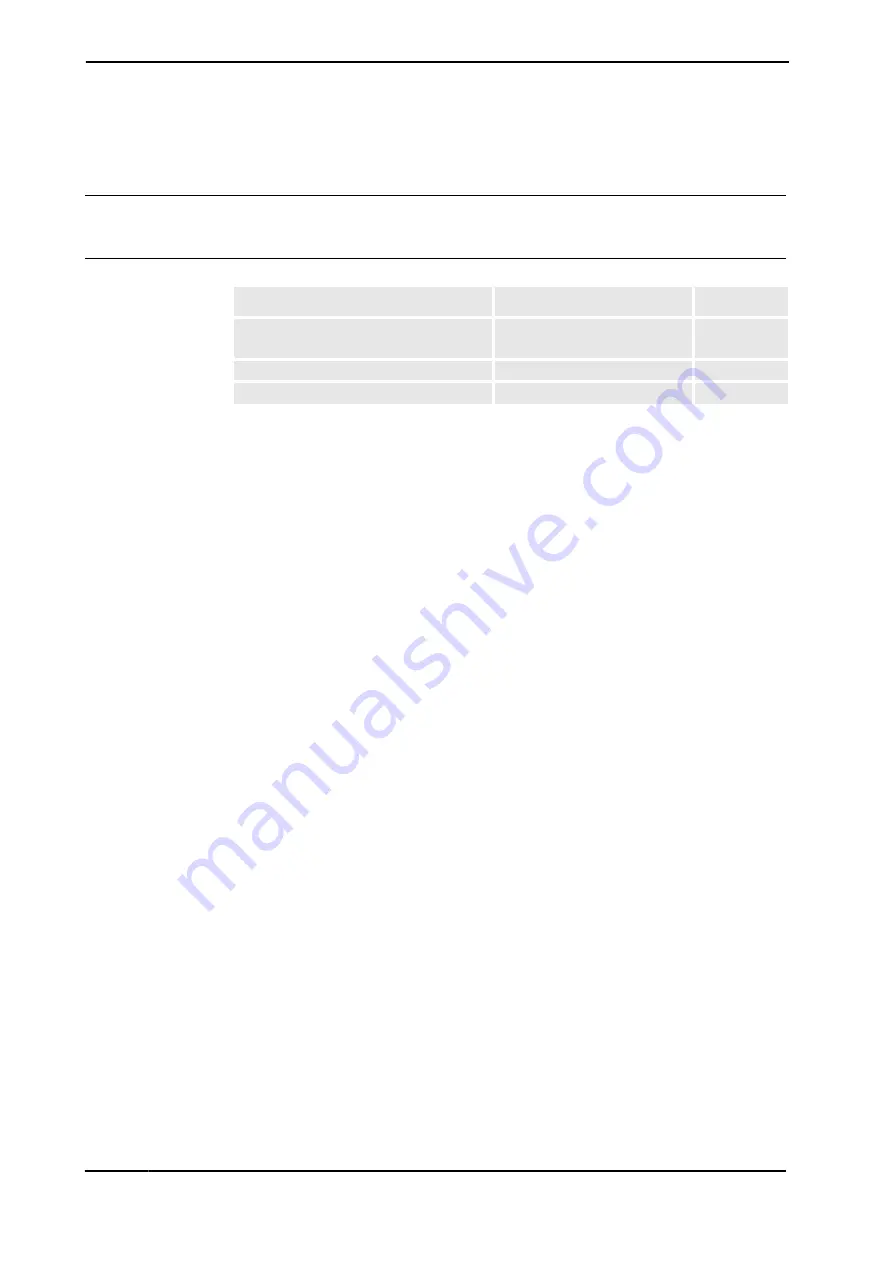
3 Maintenance
3.2.3. Expected component life
3HAC026876-001 Revision: C
114
© Copyri
ght
200
6-2008 ABB.
All rights reserved.
3.2.3. Expected component life
General
The expected life of a component can vary greatly depending on how hard it is run.
Expected life
1)
The expected life can also be affected by assemblage of cabling other than standard options.
The given life is based on a test cycle that for every axis starts from the calibration position
to minimum angle to maximum angle and back to the calibration position. Deviations from
this cycle will result in differences in expected life! The life may also be affected by acid or
alkaline environment.
2)
The given life for the balancing device is based on a test cycle that starts from the initial
position and goes to maximum extension, and back. Deviations from this cycle will result in
differences in expected life!
3)
The robot is dimensioned for a life of 8 years (350,000 cycles per year) in a normal spot
welding application. Depending on the actual application, the life of individual gearboxes
may vary greatly from this specification. The Service Information System (SIS), integrated
in the robot software, keeps track of the gearbox life in each individual case and will notify
the user when a service is due. For Foundry Prime robots, working in 100% humidity, other
service intervalls may be required.
The SIS for an M2004 system is described in the Operating manual - Service Information
System. Document number can be found in section
.
Component
Expected life
Note
Cabling for robot, 7th axisand fan
4,000,000 cycles axis 1 ±180º
2,000,000 cycles axis 1 ±220º
See note
1)
Balancing device
2,000,000 cycles
See note
2)
Gearbox
40,000h
See note
3)