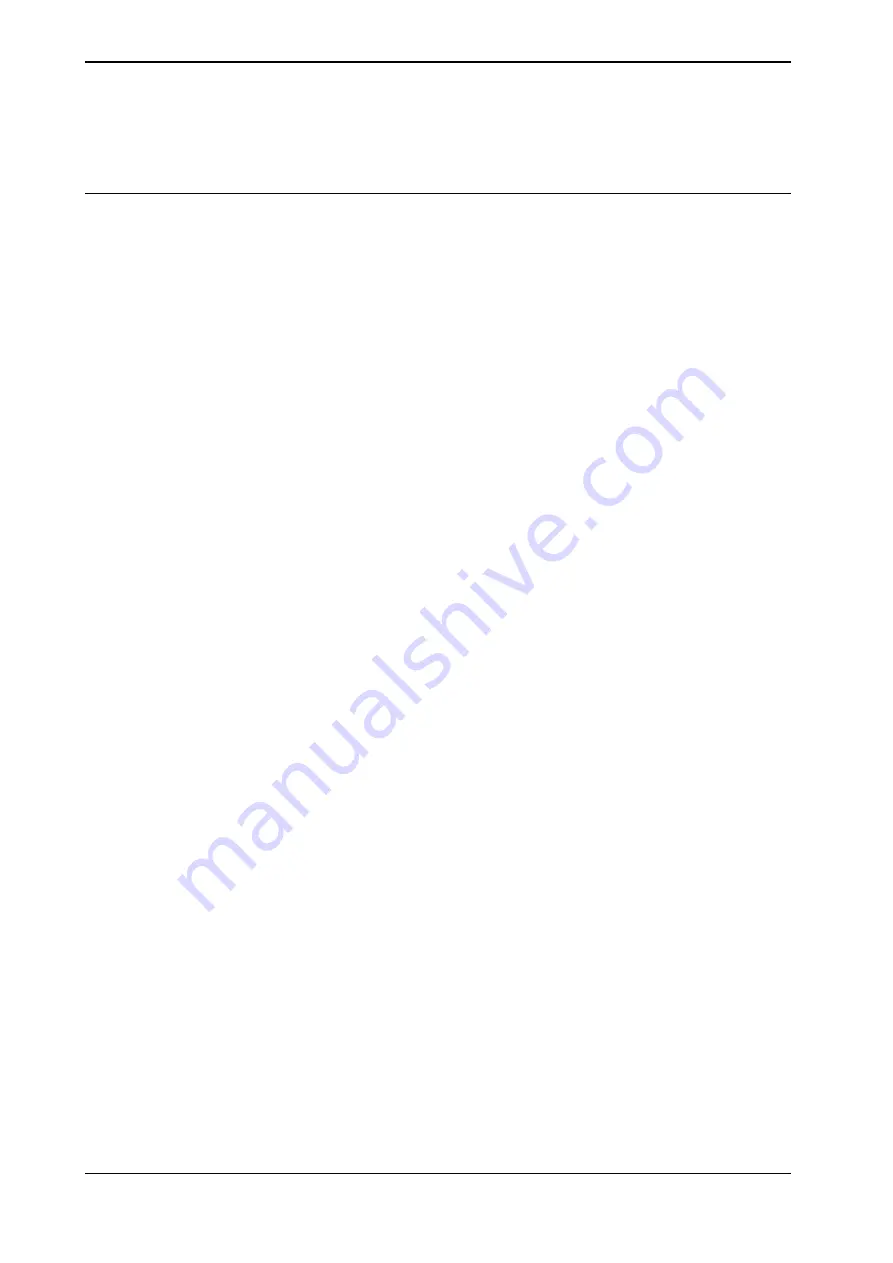
5.4.5 Reference calibration
Brief introduction to Reference Calibration
Reference calibration is a faster method compared to Fine calibration, as it refers
to a previously made calibration.
1 Create a backup of the current robot system.
2 Check that the active calibration offset values corresponds to the values on
the silver label (on the lower arm or the base).
3 Jog the manipulator so that all axes are in zero position (ex use
MoveAbsJ
instruction). Check that all axis scales are aligned with calibration marks.
4 If the scales differ from calibration marks it might depend on wrong turns of
the revolution counters. Make a marker line on the corresponding axis to be
able to validate the result of the calibration. If more than one motor revolutions
are wrong, the calibration will fail.
5 Use a verification position. This is especially recommended if all axes were
not aligned with the synchronization marks (step 3). Reuse an existing
position that is suitable and accurate so it can be used to validate the repair.
Use a position where a deviation in axis calibration gives a big deviation in
positioning. Note! Check the position after each repair in one axis.
6 Use Reference calibration to save reference values for all axes that is to be
replaced. Make sure that the values are saved in RobotStudio or FTP program.
The files are located in "Active system folder name/HOME/RefCalibFiles".
7 Perform the repair.
8 Make sure that the tooling and process equipment are the same as when
creating the reference. Use Reference calibration to update the system with
new calibration offset value for the repaired axis.
9 Check the position against the verification position (step 5).
10 Proceed with the repair of the next axis, if necessary, and repeat (step 8-9)
for every axis.
11 (For system containing SafeMove or EPS) Download new calibration values
to SafeMove. Use Visual SafeMove in RobotStudio.
12 (For system containing SafeMove or EPS) Synchronize SafeMove to activate
SafeMove.
13 Perform test run.
14 Update the label for resolver values with new calibration values.
Manual tuning of calibration offset
Manual tuning of calibration offset is normally not needed, but can be useful in
some situations. The requirement to do manual tuning is that there is a known
accurate position, that worked accurately before the repair (step 5, see
introduction to Reference Calibration on page 694
).
Example "Adjust axis 4":
1 Create a backup.
Continues on next page
694
Product manual - IRB 6700Inv
3HAC058254-001 Revision: L
© Copyright 2017 - 2020 ABB. All rights reserved.
5 Calibration
5.4.5 Reference calibration
Summary of Contents for IRB 6700Inv
Page 1: ...ROBOTICS Product manual IRB 6700Inv ...
Page 16: ...This page is intentionally left blank ...
Page 40: ...This page is intentionally left blank ...
Page 182: ...This page is intentionally left blank ...
Page 672: ...This page is intentionally left blank ...
Page 704: ...This page is intentionally left blank ...
Page 720: ...This page is intentionally left blank ...
Page 722: ...This page is intentionally left blank ...
Page 729: ......