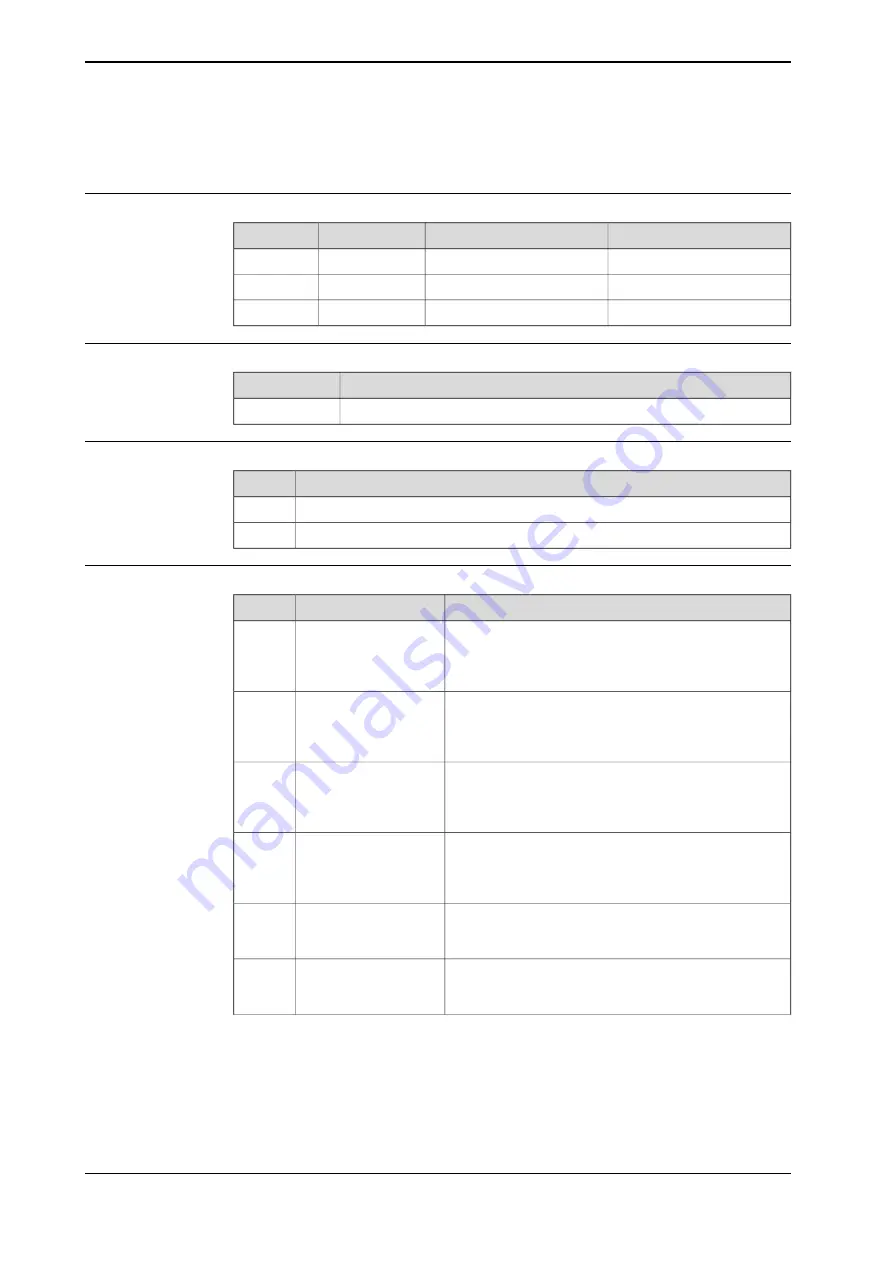
2.2 Manipulator
Variants
Reach (m)
Rated handling capacity (kg)
IRB Type
Option
0.45
3
IRB 910SC
435-135
0.55
3
IRB 910SC
435-136
0.65
3
IRB 910SC
435-137
Protection
Description
Option
Standard
287-4
Connection kit
Description
Option
For the connectors on the upper arm, customer connection.
431-1
For the connectors on the foot.
239-1
Warranty
Description
Type
Option
Standard warranty is 12 months from
Customer Delivery
Date
or latest 18 months after
Factory Shipment Date
,
whichever occurs first. Warranty terms and conditions
apply.
Standard warranty
438-1
Standard warranty extended with 12 months from end
date of the standard warranty. Warranty terms and con-
ditions apply. Contact Customer Service in case of other
requirements.
Standard wa 12
months
438-2
Standard warranty extended with 18 months from end
date of the standard warranty. Warranty terms and con-
ditions apply. Contact Customer Service in case of other
requirements.
Standard wa 18
months
438-4
Standard warranty extended with 24 months from end
date of the standard warranty. Warranty terms and con-
ditions apply. Contact Customer Service in case of other
requirements.
Standard wa 24
months
438-5
Standard warranty extended with 6 months from end
date of the standard warranty. Warranty terms and con-
ditions apply.
Standard wa 6
months
438-6
Standard warranty extended with 30 months from end
date of the standard warranty. Warranty terms and con-
ditions apply.
Standard wa 30
months
438-7
Continues on next page
46
Product specification - IRB 910SC
3HAC056431-001 Revision: G
© Copyright 2016-2020 ABB. All rights reserved.
2 Specification of variants and options
2.2 Manipulator
Summary of Contents for IRB 910SC
Page 1: ...ROBOTICS Product specification IRB 910SC ...
Page 6: ...This page is intentionally left blank ...
Page 50: ...This page is intentionally left blank ...
Page 52: ...This page is intentionally left blank ...
Page 54: ......
Page 55: ......