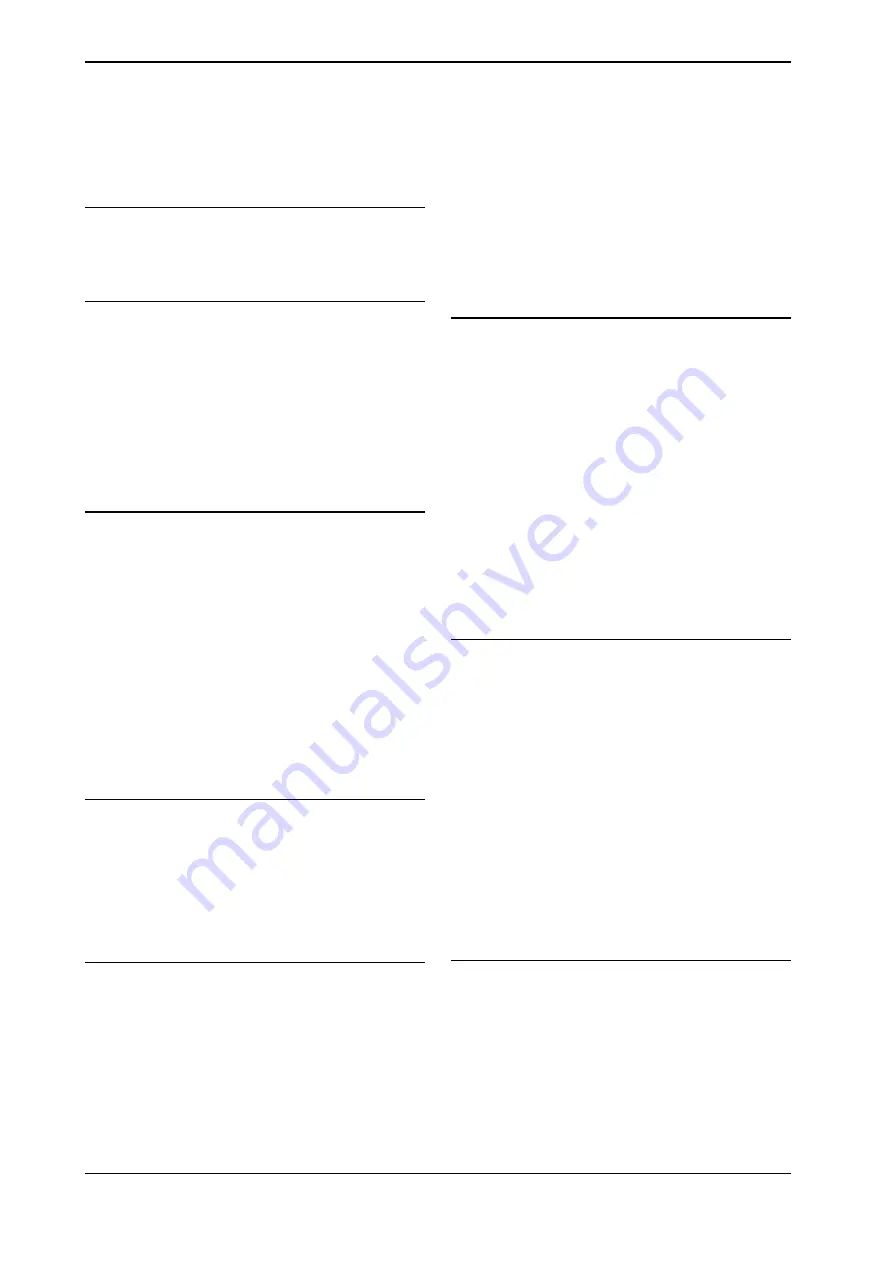
Recommended actions
Decrease speed. Deactivate OVR.
20491, SC
arg
Override active during startup
Description
Override digital input was active during startup on SC
arg
.
20492, SC
arg
SST violation in Brake test
Description
Movement detected during Brake test on Safety Controller (SC)
arg
. Mechanical unit
arg
. Axis
arg
.
Probable causes
Interrupted braketest. Worn out Brakes.
Recommended actions
Restart CBC. Replace Brake.
20493, SC
arg
SBR triggered
Description
Safe Brake Ramp (SBR) on Safety Controller (SC) was
interrupted by a Class 0 stop due to slow deceleration on
mechanical unit
arg
. This is normal and occurs in cases when
a stop1 is to slow. Check for other safety controller event
messages.
Recommended actions
Change parameter value for SBR in Motion configuration.
Trigger a new stop to test the Brake Ramp. If this happens
frequently, check the Application manual for mechanical units'
configuration.
20494, SC
arg
Tool change incorrect
Description
Incorrect tool change with Tool
arg
on mechanical unit
arg
.
Recommended actions
Check if correct tool. Decrease speed if needed. Perform a new
tool change.
20501, ES panel open
Description
The emergency stop panel has previously been broken, and
while broken, an attempt was made to operate the robot.
Consequences
The system remains in the Emergency Stop status.
Probable causes
An attempt has been made to maneuver a control, e.g. the
enabling device.
Recommended actions
To resume operation, first reset the emergency stop panel
button. Then switch the system back to state Motors ON by
pressing the Motors ON button on the Control Module.
20502, ES pendant open
Description
The emergency stop pendant has previously been broken, and
while broken, an attempt was made to operate the robot.
Consequences
The system remains in the Emergency Stop status.
Probable causes
An attempt has been made to maneuver a control, e.g. the
enabling device.
Recommended actions
To resume operation, first reset the emergency stop pendant
button. Then switch the system back to state Motors ON by
pressing the Motors ON button on the Control Module.
20503, ES ext.cat.0 open
Description
The emergency stop external has previously been broken, and
while broken, an attempt was made to operate the robot.
Consequences
The system remains in the Emergency Stop status.
Probable causes
An attempt has been made to maneuver a control, e.g. the
enabling device.
Recommended actions
To resume operation, first reset the emergency stop external
button. Then switch the system back to state Motors ON by
pressing the Motors ON button on the Control Module.
20505, Delayed stop open
Description
Delayed stop open.
Consequences
The system goes to status SYS HALT.
Continues on next page
148
Operating manual - Troubleshooting IRC5
3HAC020738-001 Revision: AA
© Copyright 2005-2018 ABB. All rights reserved.
5 Troubleshooting by event log
5.4 2 xxxx
Continued
Summary of Contents for IRC5 Compact
Page 1: ...ROBOTICS Operating manual Troubleshooting IRC5 ...
Page 10: ...This page is intentionally left blank ...
Page 40: ...This page is intentionally left blank ...
Page 90: ...This page is intentionally left blank ...
Page 586: ...This page is intentionally left blank ...
Page 588: ......
Page 589: ......