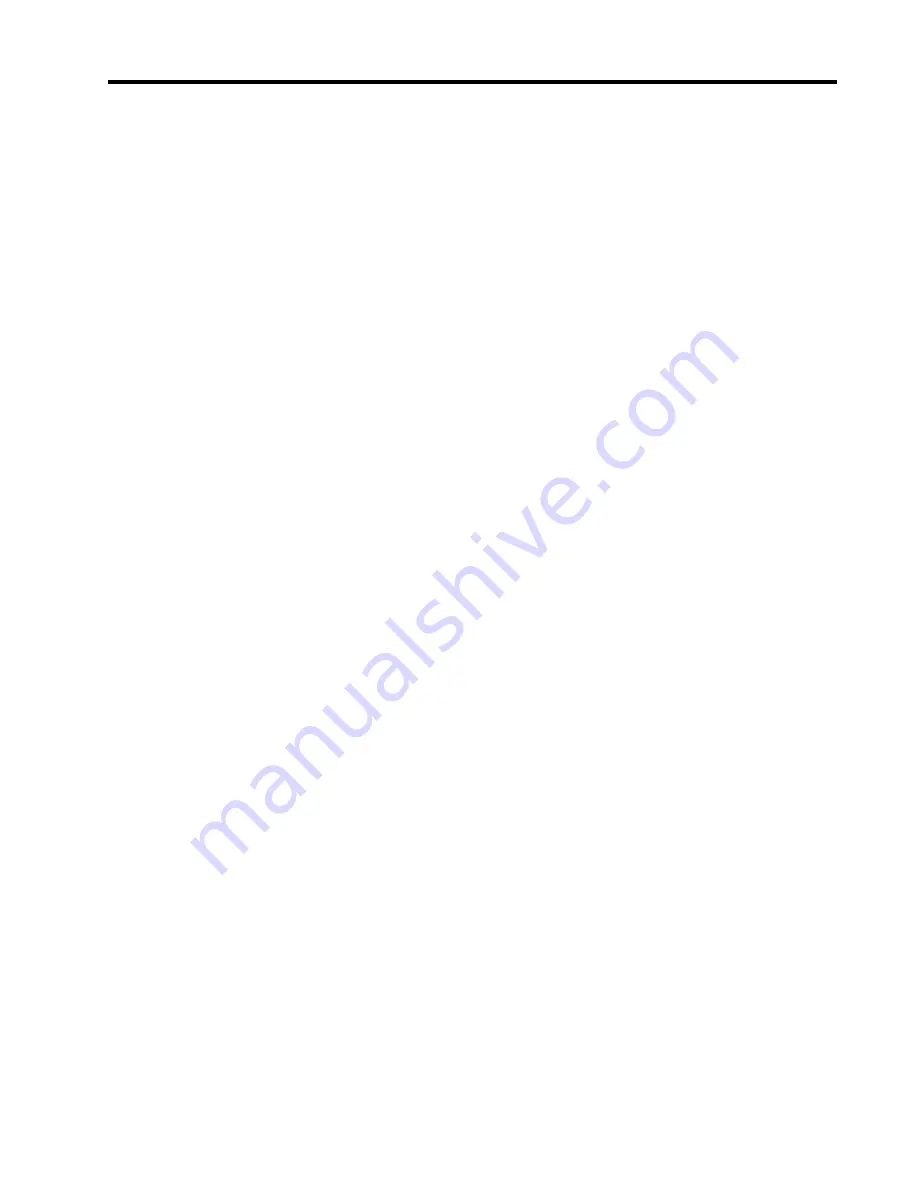
641P026-008
HMB-8 / HMB-8.7 Mechanism
©
(formerly HMB-11)
Page 9
4 November 2005
To prevent injury or equipment dam-
age, the breaker must be removed
from service, isolated, and grounded
before performing any maintenance
or manual operating procedures. Be
sure that the mechanism disc
springs are discharged and that all
control power is disconnected.
Manual operation of this mechanism
overrides all electrical breaker op-
eration lock-outs such as those that
occur with low SF
6
gas density.
4.1
Pre-Maintenance Procedures
Before performing maintenance on the mechanism, the
following actions are required:
1.
Remove the breaker from service and isolate it from
the high voltage system.
2.
Place the breaker in the OPEN position.
3.
Disconnect all control power to the mechanism.
4.
Equalize the pressure in the mechanism as described
in section 4.1.1.
5.
If the mechanism is horizontally mounted, deactivate
the close-position as described in section 4.1.5.
4.1.1
Pla cing the Mechanism Out of Service
Equalize the pressure in the mechanism with the breaker
in the OPEN position before performing any mechanism
maintenance that involves replacing parts or making ad-
justments.
Caution
Do not equalize pressure with the breaker/
mechanism in the CLOSED position.
Equalizing hydraulic pressure does not remove
the mechanical preload from the disc spring
assembly. Do not attempt to remove the disc
spring assembly.
To equalize the pressure in the mechanism:
1.
Place the mechanism in the OPEN position.
2.
Slowly open the pressure equalizing valve stem 51017
(Fig. 2) by lifting the black handle (Illustration 1) to
discharge the hydraulic pressure and release the
energy in the disc springs. The pressure should be
allowed to drop only very gradually (approximately 5
thru 10 seconds to release energy).
4.1.2
Equalizing the Pressure in the Mechansim
When doing maintenance work on the operating mecha-
nism, the circuit breaker must be placed out of service.
Prevent an automatic start of the pump motor by discon-
necting the electric power.
4.1.3
Manually Operating the Operating Mechanism
The circuit breaker can be operated by hand by pressing
the hand plungers of the pilot valves (Figure 8). The circuit
breaker may be operated only if the disc spring assembly
is charged.
4.1.4
Slow Switching Operations
This manual does not contain instructions for slow switching
operations (which are never to be performed when the
breaker is in service). If, however, slow switching operations
are necessary, they should be done only by trained personnel.
4.1.5
Deactivating the Close-Position Interlock
Deactivate the close-position interlock device on any hori-
zontally mounted mechanism. To do this, remove the
spring clip (shown in Figure 9). The close-position inter-
lock facility is engaged by reinserting the clip.
4.2
General Maintenance Practices
The following general maintenance practices should be
observed when performing mechanism maintenance.
4.2.1
Cleanliness
Because cleanliness is so important, care must be taken
to perform mechanism maintenance under clean, dry
conditions. Absolute cleanliness of all hydraulic elements
is a prerequisite for trouble-free operation of the HMB
mechanism and the circuit breaker as a whole.
The disc springs of the HMB mechanism are treated with
an anti-corrosion coating. Avoid cleaning the disc springs
with solvent (alcohol, trichlorethane, etc.) or scratching the
anti-corrosion coating. Also, avoid any contamination with
hydraulic fluid. Areas that are damaged should be recoated.
4.2.2
Mechanism Seals
During inspection/repair, replace old seals with new seals.
• Always check seals for cracks, deformities, and
brittleness
before they are installed. Acceptable
seals are flexible and free of cracks. Do not install
seals that are cracked, brittle, or deformed.
• Cleaning of internal parts is done best with a lint-free
wipe soaked in clean hydraulic oil. Wipe all oil from o-
ring seals with a lint-free wipe before installing them.
• Never clean seals with abrasives even if the abra-
sives are very fine.
4.2.3
Hydraulic Oil and Service Life
Oil used in the hydraulic system is subject to aging even
under no-load use. Oil used in the HMB mechanism
should be inspected after every 5 years of service. If the oil
is cloudy or much darker than fresh oil, the oil should be
drained, the mechanism evacuated, and the mechanism
filled with fresh oil as described in sections 4.3.2, 4.3.5,
and 4.3.6.
Summary of Contents for Mechanism HMB-8
Page 2: ......
Page 5: ...641P026 008 HMB 8 HMB 8 7 Mechanism formerly HMB 11 Page 5 4 November 2005 ...
Page 19: ...641P026 008 HMB 8 HMB 8 7 Mechanism formerly HMB 11 Page 19 4 November 2005 NOTES ...
Page 33: ...641P026 008 HMB 8 HMB 8 7 Mechanism formerly HMB 11 Page 33 4 November 2005 NOTES ...