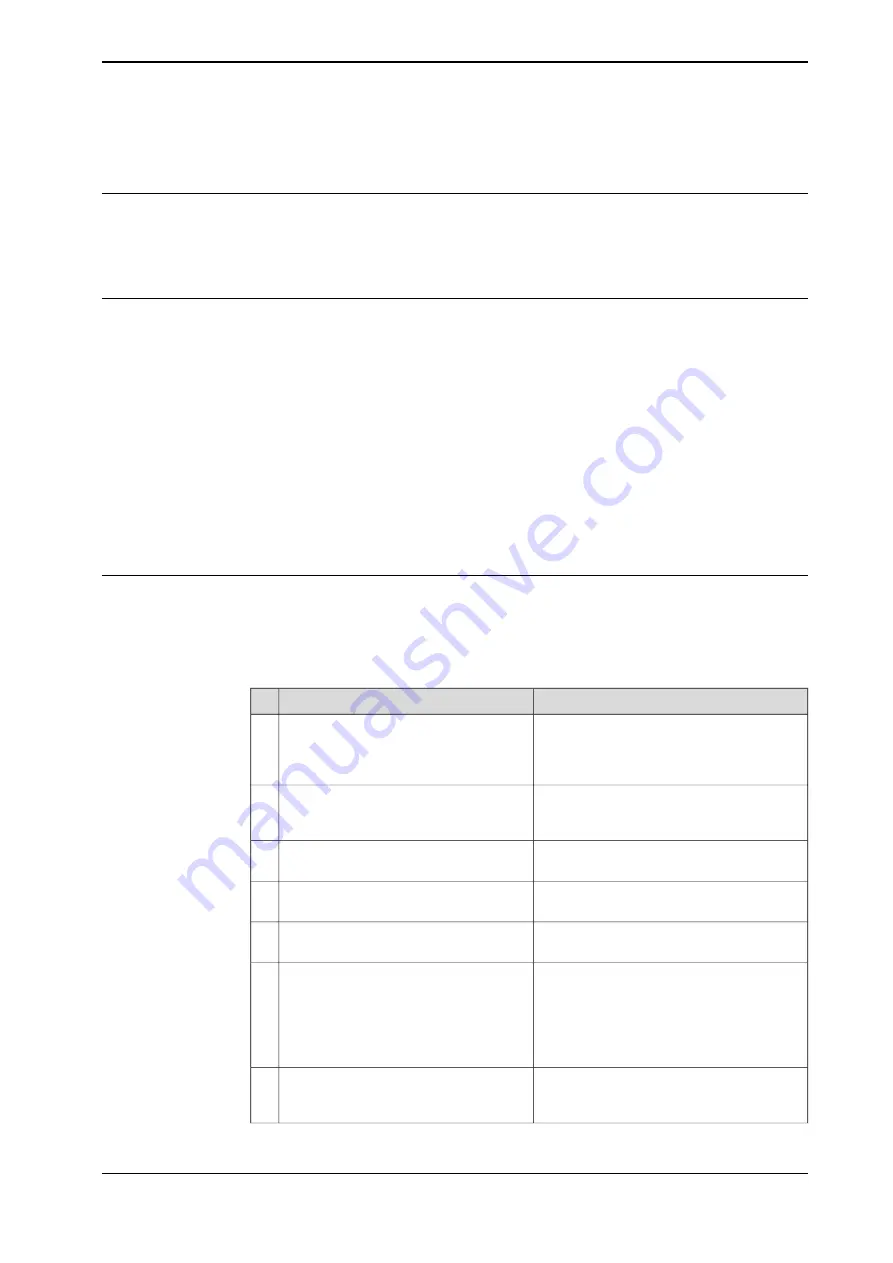
7.2.9 Inconsistent path accuracy
Description
The path of the robot TCP is not consistent. It varies from time to time, and is
sometimes accompanied by noise emerging from bearings, gearboxes, or other
locations.
Possible causes
The symptom can be caused by (the causes are listed in order of probability):
•
Robot not calibrated correctly.
•
Robot TCP not correctly defined.
•
Parallel bar damaged (applies to robots fitted with parallel bars only).
•
Mechanical joint between motor and gearbox damaged. This often causes
noise to be emitted from the faulty motor.
•
Bearings damaged or worn (especially if the path inconsistency is coupled
with clicking or grinding noises from one or more bearings).
•
The wrong robot type may be connected to the controller.
•
The brakes may not be releasing correctly.
Recommended working procedure
The path accuracy depends on many factors. The following table describes the
most common causes of problems with the path accuracy. Depending on your
installation, the recommended working procedure is to work step by step, starting
with the step that seems most plausible given your circumstances.
Note
Action
Remove the obstacles.
Study the path of the robot in motion, to
find if an external force, for example, an
external cable package, is colliding with
or restricting the movement of the robot.
1
Improve the ventilation around the robot.
In high temperature environments, the
material in the robot can expand, thereby
causing inconsistent path accuracy.
2
How to define these are described in
Oper-
ating manual - OmniCore
.
Make sure the robot tool and work object
are correctly defined.
3
Update if required.
Check the positions of the revolution
counters.
4
How to calibrate the robot is described in
the product manual for the robot.
If required, re-calibrate the robot axes.
5
Replace the faulty motor, gearbox, or bearing
as specified in the product manual for the
robot.
If you hear noise that has not been there
before, locate the source to define if a
motor or bearing is faulty.
6
Study the path of the robot TCP to estab-
lish which axis, and thus which motor,
may be faulty.
Replace the faulty parallel bar as specified
in the product manual for the robot.
Check the trueness of the parallel bar
(applies to robots fitted with parallel bars
only).
7
Continues on next page
Product manual - OmniCore V250XT
371
3HAC073447-001 Revision: B
© Copyright 2020-2022 ABB. All rights reserved.
7 Troubleshooting
7.2.9 Inconsistent path accuracy
Summary of Contents for OmniCore V250XT
Page 1: ...ROBOTICS Product manual OmniCore V250XT ...
Page 34: ...This page is intentionally left blank ...
Page 50: ...This page is intentionally left blank ...
Page 174: ...This page is intentionally left blank ...
Page 410: ...This page is intentionally left blank ...
Page 418: ...This page is intentionally left blank ...
Page 454: ......
Page 455: ......