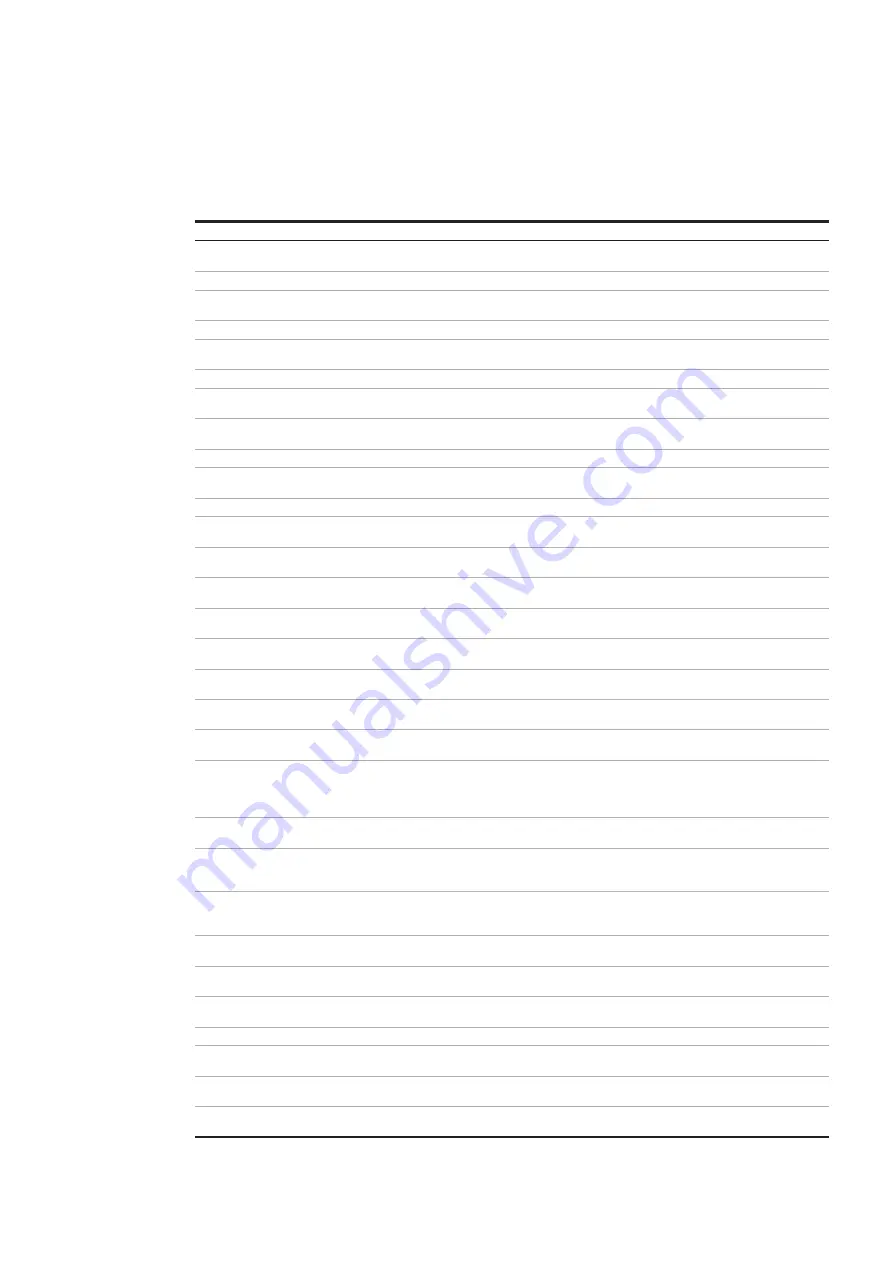
USER I N T ER FAC E
13
The DSP controller and the μcontroller can both record system faults. Most faults reported by the
μcontroller relate to control board failure, whereas the DSP mainly reports faults related to the
installation. Table 6 and Table 7 offer an overview of faults recorded by the DSP controller and
μcontroller respectively:
—
Table 6: Overview of events
Name
Description
Action
Over voltage RMS
The RMS value of the supply voltage is higher than
the acceptable maximum value
Disconnect from grid
Over voltage Peak
The peak valud of the supply voltage is too high
Disconnect from grid
Under voltage RMS
The RMS value of the supply voltage is lower than
the acceptable minimum value
Disconnect from grid
Loss of phase
The system detected a loss of supply on at least one phase
Disconnect from grid
Wrong phase rotation
The module is fed by a supply system, which has
the wrong phase rotation
Inverter trips/
reset required
Unbalanced supply
The supply imbalance is out of range
Disconnect from grid
Island detected
Unit was grid connected initially, but has detected it is currently
in island while island operation is forbidden
Disconnect from grid
Bad CT connection
The automatic CT detection procedure encountered a problem
during the identification process
Continue
Over frequency
The system detected that the network frequency above limit
Disconnect from grid
Unstable mains
frequency
The network frequency is fluctuating too fast
Disconnect from grid
No synchronization
The system cannot synchronize with the network
Disconnect from grid
DC over voltage (SW)
The DC software over voltage protection was triggered
Inverter trips/
reset required
DC over voltage (HW)
The DC hardware over voltage protection was triggered
Inverter trips/
reset required
DC under voltage (SW)
The DC software under-voltage protection was triggered
Inverter trips/
reset required
Preload problem
The DC capacitors could not be preloaded. The voltage increase
on the DC capacitors during the preload phase is not high enough
Inverter trips/
reset required
DC Top over voltage
The DC over-voltage protection of the capacitors in the
positive stack was triggered
Inverter trips/
reset required
DC Bot over voltage
The DC over-voltage protection of the capacitors in the
negative stack was triggered
Inverter trips/
reset required
Over current peak (SW) The software peak current protection was triggered
Inverter trips/
reset required
Over current RMS
The system detected an RMS over-current
Inverter trips/
reset required
Global battery voltage
error
The battery voltage exceeds the maximum DC voltage of
PQstorI, the battery connections (+/-) are inverted or the AC voltage
is high and the battery voltage (SoC) is too low, preventing the DC
contactor from closing
Inverter trips/
reset required
Ground fault
Valid only in 3W, when common mode current it too high
Inverter trips/
reset required
IGBT temporary
The IGBT modules report a transient error that could be cleared by the
system, possibly due to peak over-current or a control voltage too low
for the IGBT drivers
Inverter trips/
reset required
IGBT permanent
The IGBT modules report an error that cannot be cleared by the system,
possibly due to peak over-current or a control voltage too low for the
IGBT drivers
Inverter trips/
reset required
IGBT check cooling
Software reported an IGBT over-temperature
Inverter trips/
reset required
SPI error
The DSP received no response from the SPI port
Inverter trips/
reset required
Mismatch between
units
Modules in a multiple module system have different settings
(e.g. 3-wire and 4-wire setting) or are connected in different ways
Inverter trips/
reset required
Under frequency
The system detected that the network frequency under limit
Disconnect from grid
Bad sequence
The DSP detected an inadequate behavior in the sequence
Inverter trips/
reset required
Bad ratings
Inconsistent set of commissioning parameters
Inverter trips/
reset required
Emergency stop
Emergency stop input has been activated
Inverter trips/
NO reset required