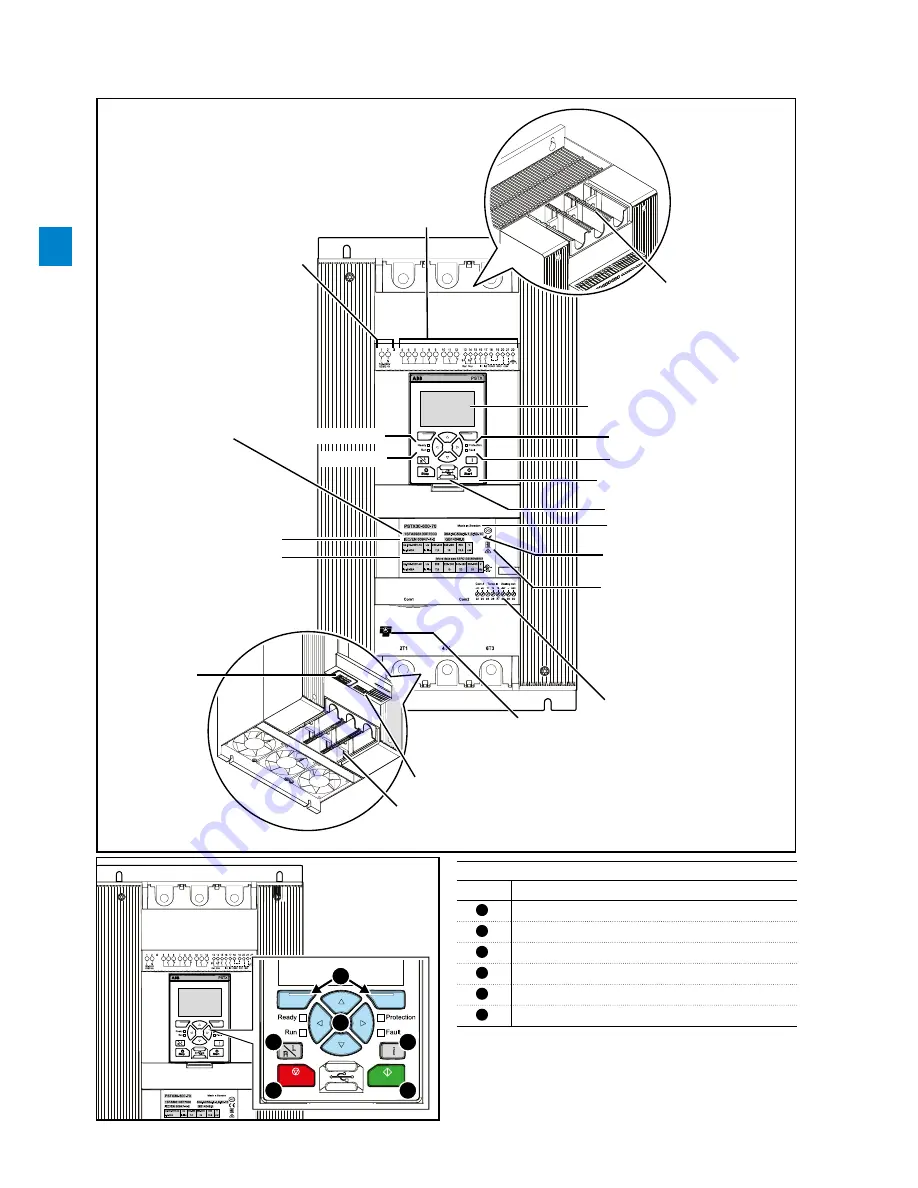
14
Description
| Service Manual | 1SFC13105M0201
2.1.8
Markings and connections
Table 4
Position Key
1
Selection soft keys
2
Navigation keys
3
R\L-key = Remote or Local control
4
i-key = Information
5
Stop key
6
Start key
L
100-250V
50/60 Hz
K4
K5
K6
Start Stop
In1 In2 DGND
+24V
GND
N
In0
Ready
Run
Fault
Protection
PSTX
Start
Options
Menu
3
5
1
4
6
2
1
Stop
L
100-250V
50/60 Hz
K4
K5
K6
Start Stop
In1 In2 DGND
+24V
GND
N
In0
Ready
Run
Fault
Protection
PSTX
Symbol for
Torque control
Anybus
connection
(Com2)
Supply voltage Us
Order code
Technical data
according to UL 508
Fieldbus connection (Com1)
Motor side connection
Terminal marking of
control circuits
Line side connection
Display
Keypad
Mini USB
Country of origin
Utilization code
Approvals
Terminal marking of
control circuits
Protection (Yellow)
Fault (Red)
Technical data
according to
IEC 60 947-4-2
Ready (Green)
Run (Green)
2
Summary of Contents for PSTX 1050
Page 1: ...Softstarter type PSTX720 840 Service manual Service manual en rev B 1SFC132115M0201 ...
Page 4: ......
Page 6: ......
Page 16: ...16 Description Service Manual 1SFC13105M0201 2 ...
Page 54: ...54 Service PSTX720 840 Service Manual 1SFC13105M0201 3 ...
Page 57: ...1SFC13105M0201 Service Manual Circuit Diagrams 57 4 ...
Page 59: ...1SFC13105M0201 Service Manual Revisions 59 5 ...