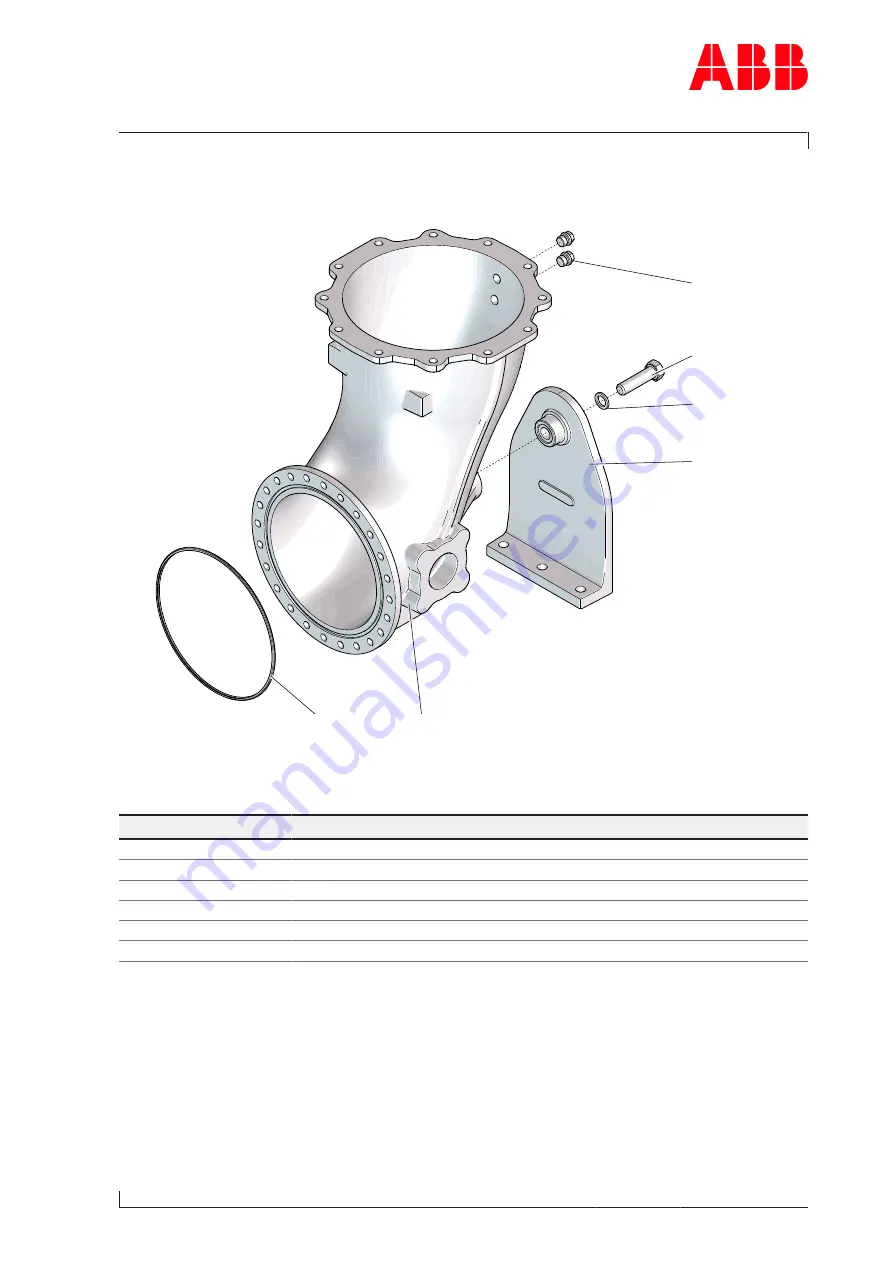
Operation Manual / Power2 340-H / Low-pressure stage
13 Spare parts / 13.2 Spare part – Illustrations
© Copyright 2022 ABB. All rights reserved.
HZTL4053_EN
Rev.F
March 2022
Gas outlet casing
61004
61003
61005
61300
61001
61002*
HZTL443298 Mod. A
* = Available within the spare part set
Part no.
Designation
61001
Gas outlet casing
61002*
Gasket
61003
Hexagon-head screw
61004
Verbusripp washer
61005
Screw plug
61300
Support
Table 61
Page
107
/
122
Summary of Contents for PT003924
Page 2: ......