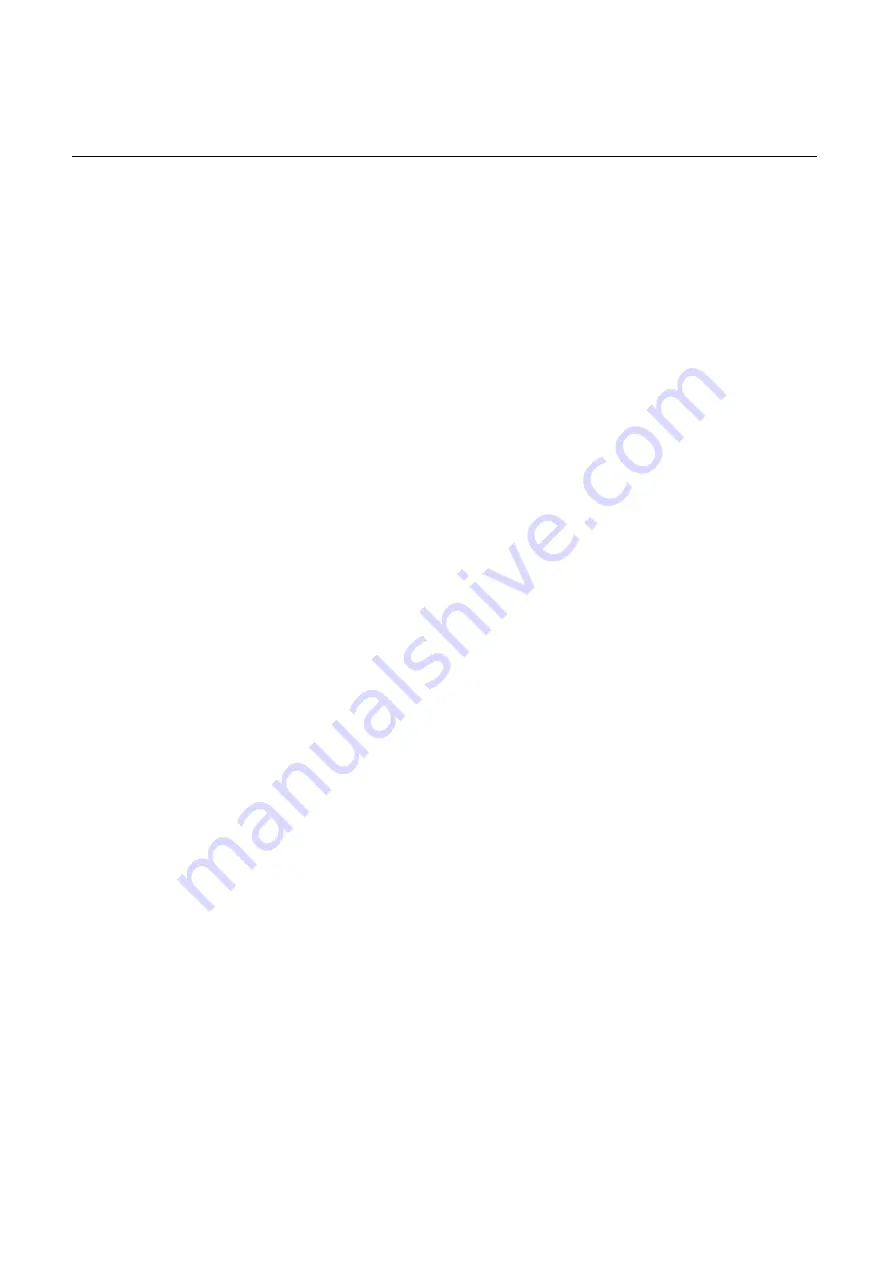
73
About this chapter
Chapter 11
Establishing connection and
verifying the
SPA/IEC-communication
Chapter 11 Establishing
connection and
verifying the
SPA/IEC-communi
cation
About this chapter
This chapter contains instructions on how to establish connection and verify that the
SPA/IEC-communication operates as intended, when the terminal is connected to a monitoring
or control system via the rear SPA/IEC port.
Summary of Contents for REB 551-C3*2.5
Page 9: ...Contents ...
Page 21: ...12 Introduction to the installation and commissioning manual Chapter 1 Introduction ...
Page 27: ...18 Note signs Chapter 2 Safety information ...
Page 53: ...44 Installing the 56 64 kbit data communication cables Chapter 5 Installing the terminal ...
Page 59: ...50 Checking the binary I O circuits Chapter 6 Checking the external circuitry ...
Page 147: ...138 Repair support Chapter 16 Fault tracing and repair ...