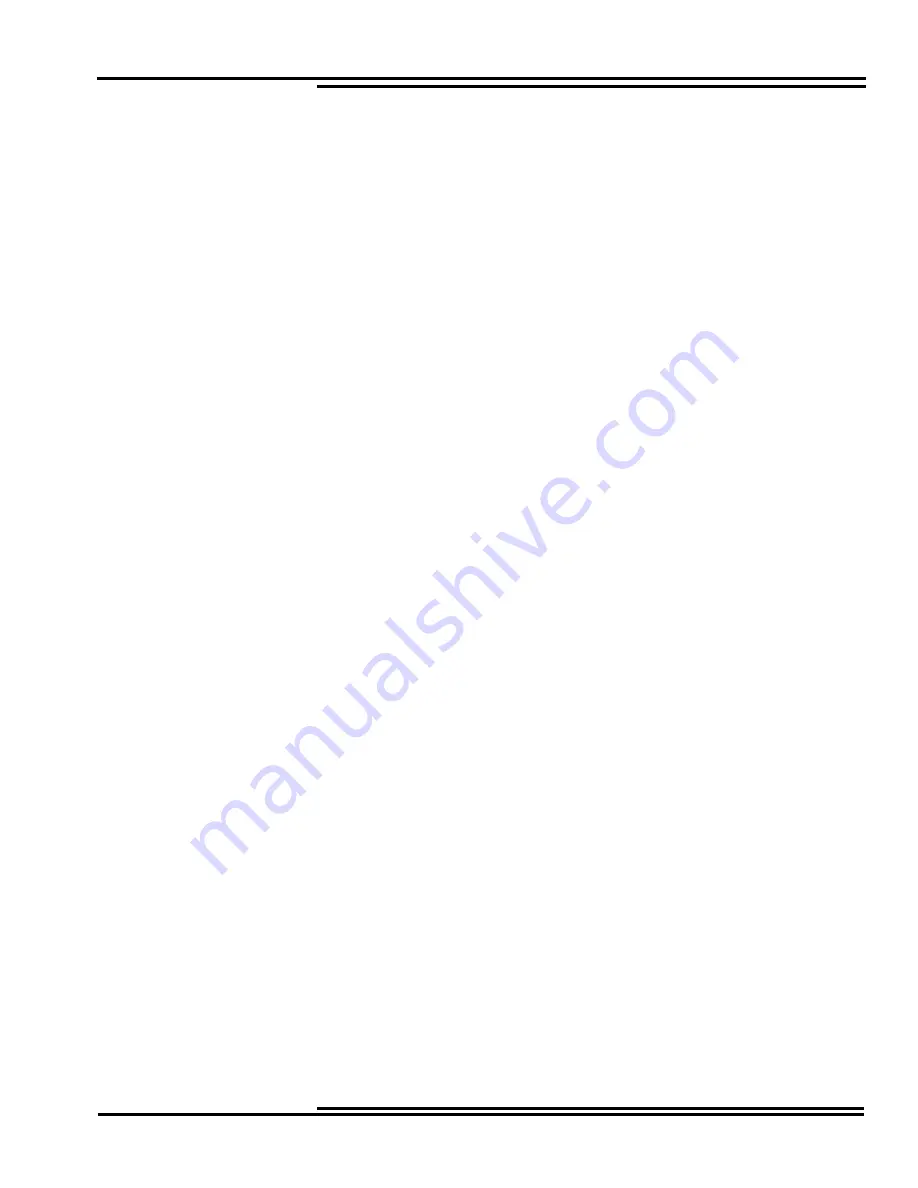
ABB REL 356 Current Differential Protection
2-7
Installation, Operation and Maintenance
Test Plugs and FT-14 Switches
• Test Plugs are available as accessories; they are inserted into the FT-14 switches for the purpose of System Function
Tests.
External Wiring
All external electrical connections pass thru the Backplate on the outer chassis. Seven DIN connectors (J11, J12, J13,
JA1, JA2, JA3, JA4) allow for the removal of the inner chassis from the outer chassis.
Electrical inputs to the Backplane module, which are routed either directly thru the Backplate or thru the FT-14 switch to
the Backplate include:
•V
A
, V
B
, V
C
and V
N
•I
A
/I
AR
, I
B
/I
BR
, I
C
/I
CR
• Power Supply (Battery) Inputs
Primary (IBP, IBN)
Backup (2BP, 2BN)
Analog input circuitry consists of three current transformers (I
A
, I
B
, I
C
) three voltage transformers, (V
A
, V
B
and V
C
), and
low-pass filters. The six transformers are located on the Backplane PC Board. The primary winding of all six transform-
ers are directly-connected to the input terminal TB6/1 thru 12; the secondary windings are connected thru the Intercon-
nect module to the Analog Input module.
As shown in Figure 2-1, dry contact outputs for breaker failure initiation (BFI), reclosing initiation (RI), reclosing block
(RB), failure alarm and trip alarm are located on the Backplane PC Board.
As shown in Figure 2-4, the power system ac quantities (V
a
, V
b
, V
c
, V
n
, I
a
, I
b
, I
c
), as well as the dc sources are connected
to the left side 1FT-14 switch (front view). All the trip contact outputs are connected to the right-side 2FT-14 switch (front
view). Switches 13 and 14 on 2FT-14 may be used for disabling the Breaker Failure Initiation/Reclosing Initiation (BFI/
RI) control logic.
The INCOM/PONI communication box is mounted thru the Backplate of the outer chassis and connected to the Backplane
module. An RS-232C serial port is provided for remote transmission of target data. The serial port is also available for
networking, data communications, and remote settings.
Separating the Inner and Outerchassis
CAUTION: It is recommended that the user of this equipment become acquainted with the information in these
instructions before energizing the REL 356 and associated assemblies. Failure to observe this precaution may
result in damage to the equipment.
All integrated circuits used on the modules are sensitive to and can be damaged by the discharge of static
electricity. Electrostatic discharge precautions should be observed when operating or testing the REL 356.
CAUTION: Use the following procedure when separating the inner chassis from the outer chassis; failure to
observe this precaution can cause personal injury, or undesired tripping of outputs and component damage.
a. Unscrew the front panel screws.
b. Remove the (optional) FT-14 covers if supplied (one on each side of the REL 356).
c. Open all FT-14 switches.
Do Not Touch the outer contacts of any FT-14 switch; they may be energized.
d. Slide out the inner chassis.
e. Close all FT-14 switches.
f. Replace the FT-14 covers.
g. Reverse procedures above when replacing the inner chassis into the outer chassis.
Summary of Contents for REL 356
Page 23: ...ABB REL 356 Current Differential Protection 1 10 Product Overview and Specifications ...
Page 83: ...ABB REL 356 Current Differential Protection 3 36 Settings and Application ...
Page 127: ...ABB REL 356 Current Differential Protection 5 28 Testing ...
Page 186: ...LINE SECTIONALIZING USING A PLC AND ABB PROTECTIVE RELAY Page 49 of 53 ...
Page 187: ...LINE SECTIONALIZING USING A PLC AND ABB PROTECTIVE RELAY Page 50 of 53 ...
Page 188: ...LINE SECTIONALIZING USING A PLC AND ABB PROTECTIVE RELAY Page 51 of 53 ...
Page 189: ...LINE SECTIONALIZING USING A PLC AND ABB PROTECTIVE RELAY Page 52 of 53 ...