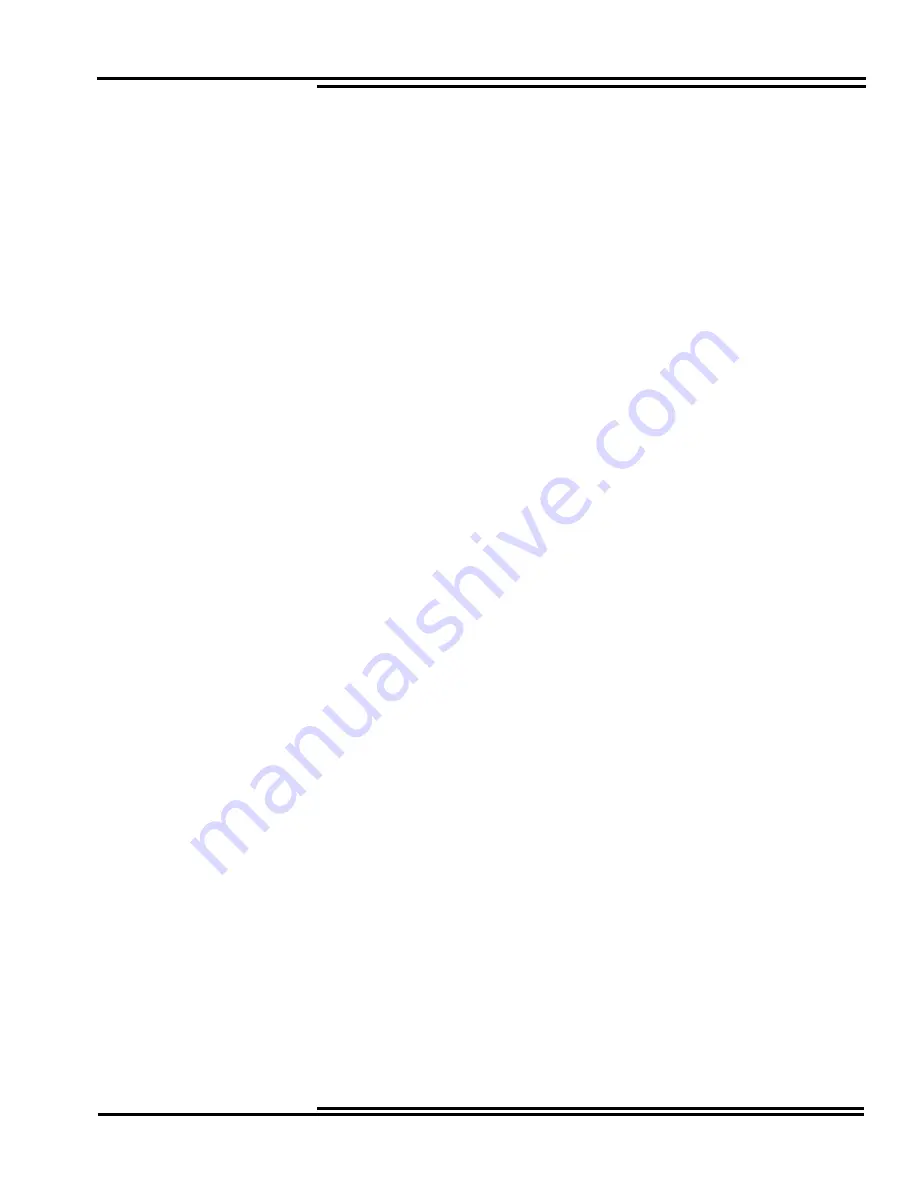
ABB REL 356 Current Differential Protection
3-33
Settings and Application
Out of Step Block (OSB)
OSB = BOTH
This setting enables the out of step block logic that blocks the Zone 2 and/or Zone 3 distance units for out of step
conditions. The setting options are:
NONE
No OSB used
Z2
Out of step logic blocks Zone 2 impedance elements only
Z3
Out of step logic blocks Zone 3 impedance elements only
BOTH
Out of step logic blocks Zone 2 and Zone 3 impedance elements
Inner Blinder (RT)
RT = 1.15 ohms
This setting is the offset in the perpendicular direction to the line impedance on the R-X diagram in secondary ohms.
Apart from its function in the OSB and OST logic, it also performs load restriction of the three phase impedance units.
The resistance RT must have a setting sufficiently low (in ohms) to avoid operation on the minimum stable swing ohms
expected. Similarly it must have a setting sufficiently high to accommodate the maximum fault resistance that is likely
to be encountered for three phase faults on the protected line. Operation of the three phase distance function for all
zones can be avoided for swing angles (between the two equivalent sources) as great as 120
°
if the inner blinder is given
a resistance setting of 0.288 Z
T
or less, where Z
T
is the protected line positive sequence impedance plus the sum of the
lowest positive sequence impedance at each end of the line. The minimum setting should accommodate a three phase
fault resistance value of at least 0.1 Z
T
ohms based on an arc voltage of 400 volts per foot (primary) and typical phase
separation.
Using the average of these two conservative figures a reasonable value to use for the inner blinder resistance is 0.2 Z
T
.
RT = 0.2 x Z
T
= 0.2 (Z1SA + Z1SB + ZL1) = 0.2( 2.56 + 2.22 + 4.86) primary = 5.752 x 0.2 secondary = 1.15 ohms
secondary
Outer Blinder (RU)
RU = 3.45 ohms
This setting is the offset in the perpendicular direction to the line impedance on the R-X diagram in secondary ohms.
The outer blinder resistance setting must be chosen to assure proper distinction between faults and swing conditions.
Sustained load must not be allowed to operate the outer blinder. The recommended setting is 3 times the inner blinder
setting but not more than 80% of minimum load impedance.
RU = 3 x RT = 3 x 1.15 = 3.45 ohms < 80% of the minimum load impedance (10.6 ohms)
Out of Step Detection Timer (OST1)
OST1 = 5.00 cycles
This timer is started when the outer blinder, RU, has operated but the inner blinder, RT, has not operated. If the timer
times out, an out of step condition has been detected and OSB is active. The recommended setting is 3 cycles.
Out-of-step trip not used
Out of Step Trip Way In Timer (OST2)
OST2 = 5.00 cycles
This timer is started when the an out of step condition has been detected and the two blinders have operated. Once it
times out, a trip signal is issued for OST. The recommended setting is 2 cycles.
Out-of-step trip not used
Out of Step Trip Way Out Timer (OST3)
OST3 = 5.00 cycles
This timer is started when the an out of step condition has been detected and the OST2 timer has timed out and both
blinders are not operated. This permits controlling the time that the breaker opens. The recommended setting is 0.5
cycles.
Out-of-step trip not used
Summary of Contents for REL 356
Page 23: ...ABB REL 356 Current Differential Protection 1 10 Product Overview and Specifications ...
Page 83: ...ABB REL 356 Current Differential Protection 3 36 Settings and Application ...
Page 127: ...ABB REL 356 Current Differential Protection 5 28 Testing ...
Page 186: ...LINE SECTIONALIZING USING A PLC AND ABB PROTECTIVE RELAY Page 49 of 53 ...
Page 187: ...LINE SECTIONALIZING USING A PLC AND ABB PROTECTIVE RELAY Page 50 of 53 ...
Page 188: ...LINE SECTIONALIZING USING A PLC AND ABB PROTECTIVE RELAY Page 51 of 53 ...
Page 189: ...LINE SECTIONALIZING USING A PLC AND ABB PROTECTIVE RELAY Page 52 of 53 ...