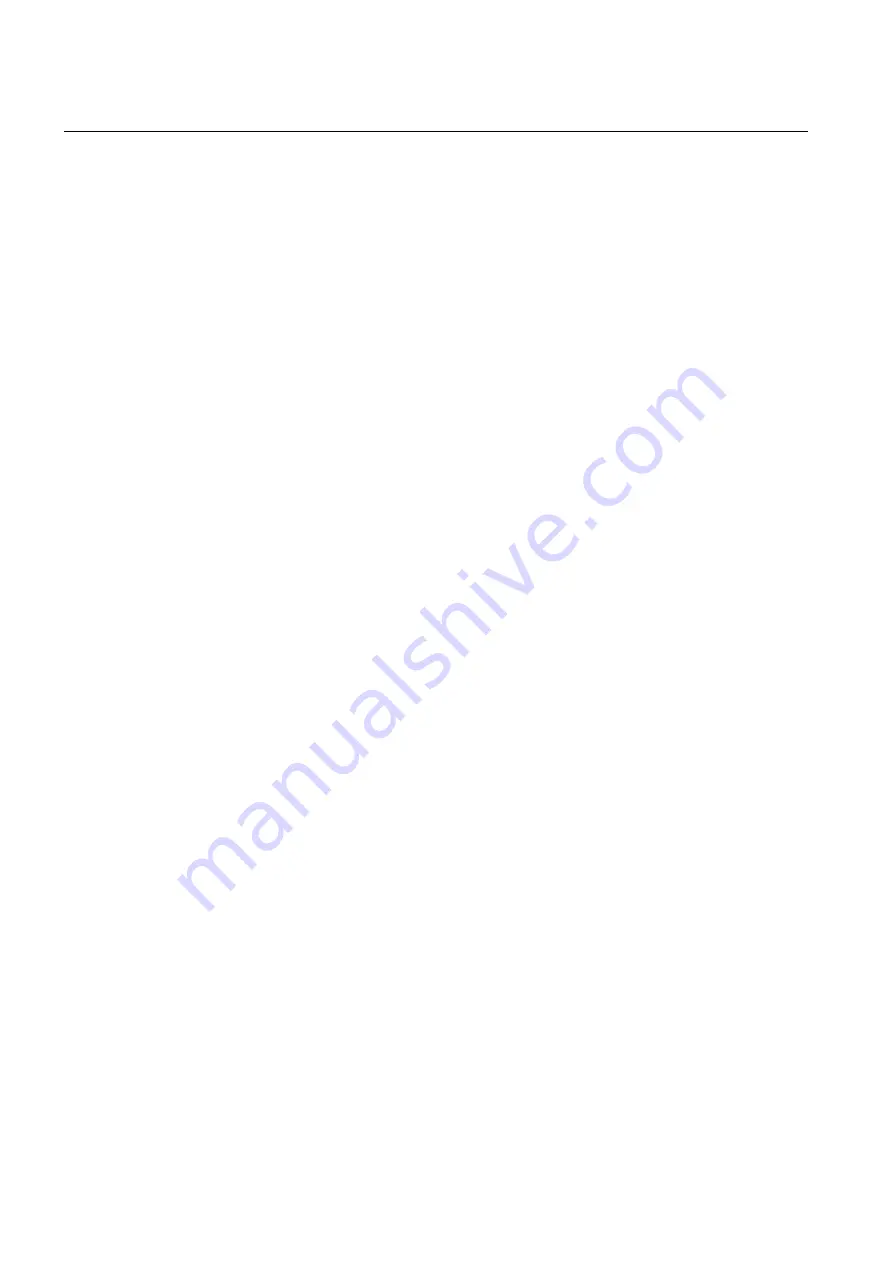
The pickup value of the ground-fault element is typically selected to be 5...30% In
of the fully developed ground-fault current and the operate time to be 0.5...2
seconds.
If a residual connection is preferred, the pickup value and operate time must be set
slightly higher in order to avoid possible stability problems due to unbalance in the
main transformers, as the unbalance will cause virtual ground-fault currents during
high phase current conditions. Also, an external stabilizing resistor can be used to
compensate too weak main transformers, thus preventing them from causing
ground-fault currents.
6.1.7.1.
Stabilizing virtual ground-fault currents
An apparent ground-fault current caused by the difference between the phase current
transformers connected in parallel may cause nuisance trippings of the ground-fault
element, especially during an overload. This can be avoided by using a stabilizing
resistor in the ground-fault current circuit. The continuous power withstand of the
resistor can be 30 W, for instance. The resistance value can be, for instance, 100
Ω
when the 1 A input is used and 10
Ω
when the 5 A input is used. The value of the
knee-point voltage must be checked and should be >2 x U
stab
. The stabilizing
resistor will also slightly reduce the ground-fault sensitivity.
6.1.7.2.
Increasing the sensitivity of the ground-fault protection
The sensitivity of the ground-fault protection can be increased by using a relay
provided with a 1 A input instead of one with a 5 A input. This is possible in a
solidly grounded network as well, because the thermal withstand capability of the
current input is normally high enough.
6.1.8.
Circuit-breaker failure protection
The operate time of the CBFAIL should be set to be longer than the circuit-breaker
opening time + the resetting time of the protection element with the longest resetting
time, with the exception of the thermal, temperature and phase reversal protection
elements and the external trip.
6.1.9.
Temperature protection (optional)
Tripping due to a beginning thermal overload can be avoided by reducing the load
of the motor at an alarm of element 49/38-1/49/38-2.
6.2.
Protecting a circuit-breaker controlled motor
Data of the squirrel cage motor stated by the manufacturer:
138
REM 610
REM 610
Motor Protection Relay
Technical Reference Manual - ANSI Version
1MRS755537
Summary of Contents for REM 610
Page 1: ...Motor Protection Relay REM 610 REM 610 Technical Reference Manual ANSI Version ...
Page 2: ......
Page 6: ...6 ...
Page 8: ...8 ...
Page 12: ...12 ...
Page 124: ...124 ...
Page 144: ...144 ...
Page 154: ...154 ...
Page 157: ......