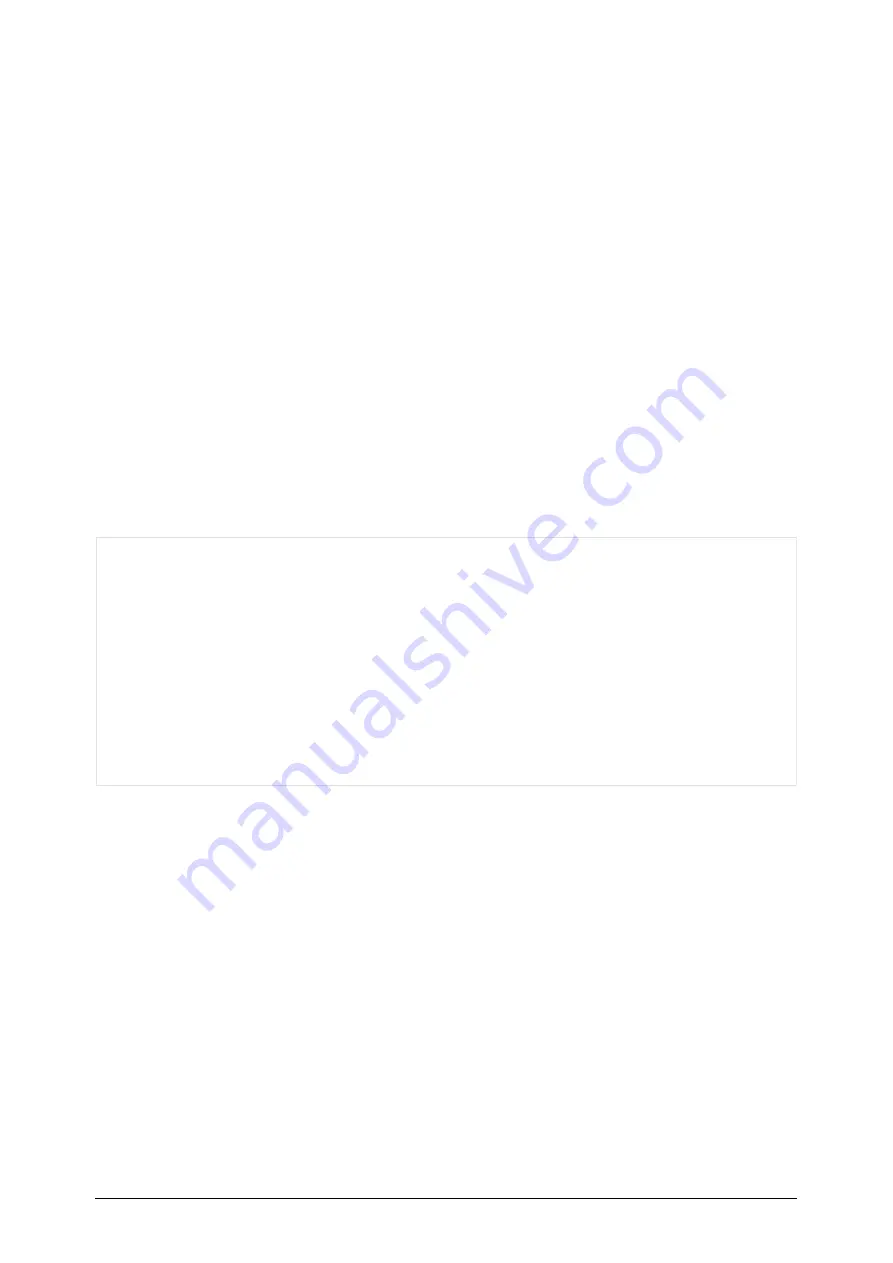
mode, and then back to Automatic mode.
Path handling of instructions with multiple joint targets
The path functions Rotate, Translate, and Mirror do not work as expected with instructions containing
via points as jointtargets. The functions will leave the jointtargets as is. Interpolate Path gives an
Unknown Error and Tool Compensation reports an error message.
Event Manager: Simulation cannot be triggered by analog system signals
The event manager only supports analog station signals, not analog system signals.
Conveyor Tracking
*Conveyor objects must be re-added for stations created prior to RS 6.05
When opening stations with conveyor tracking created prior to RobotStudio 6.05, conveyor objects
must be re-added.
Incorrect default values for c1Position and c1Speed for RobotWare 5 with the PaintWare option
The default values for the parameters c1Position and c1Speed may become incorrect for a virtual
controller system. The symptom is that its attribute values are all zero, see snapshot below.
Workaround:
Save the following lines to a CFG file named ‘TEMP.CFG’ or similar and load in the virtual
controller followed by a restart.
EIO:CFG_1
.0
:
5
:
0
::
#
EIO_SIGNAL:
-Name
"c1Position"
-SignalType
"AI"
-Unit
"CnvIf"
\
-SignalLabel
"ctPosition"
-UnitMap
"0-31"
-Access
"ALL"
\
-MaxLog
21474.8
-MaxPhys
1
-MaxPhysLimit
1
\
-MaxBitVal
2147483647
-MinLog -
21474.8
-MinPhys -
1
-MinPhysLimit -
1
\
-MinBitVal -
2147483647
-Name
"c1Speed"
-SignalType
"AI"
-Unit
"CnvIf"
-SignalLabel
"ctSpeed"
\
-UnitMap
"32-63"
-Access
"ALL"
\
-MaxLog
21474.8
-MaxPhys
1
-MaxPhysLimit
1
\
-MaxBitVal
2147483647
-MinLog -
21474.8
-MinPhys -
1
-MinPhysLimit -
1
\
-MinBitVal -
2147483647
MultiMove
MultiMove error: ‘Object reference not set to an instance of an object’
When the Test Play button is pressed in the MultiMove tool, the following error message may be
displayed: ‘Object reference not set to an instance of an object’, but the robot moves and the Status
‘Calculation OK’ is displayed. In addition, when ‘Create Paths‘ is pressed the following message is
displayed: ‘Can't create paths : Value cannot be null’, and no paths are created. In the ‘Create Paths
Settings’, is the WP TCP drop down empty.
Reason:
Workobject is not set for the current task.
External Axis
Error 50091: ‘Restart not possible’ after warm start of a system with external axis
When restarting a system with activated mechanical units the activation state is lost. Then the program
can no longer be started from the Virtual FlexPendant, the RAPID Editor or the RAPID Tasks window.
Workaround:
Reset the program pointer (‘Program Pointer to Main’) before starting the program from
© Copyright 2021 ABB. All rights reserved.
22/30