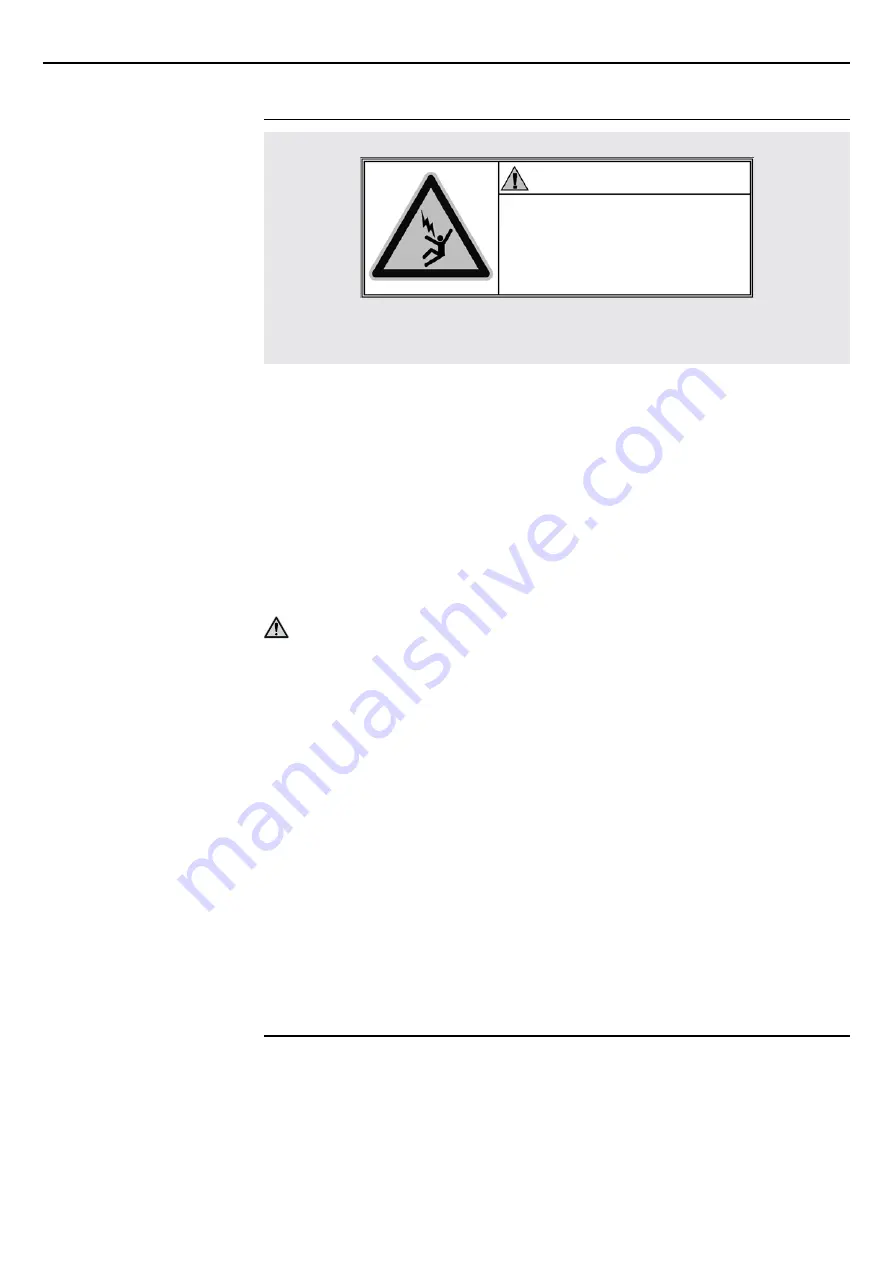
ABB | SACE Emax 2
Emax E2.2-E4.2-E6.2 circuit-breakers
2 - Safety
5 | © 2023 ABB | 1SDH001000R0002 - ECN000297030
2 - Safety
Warnings
HAZARD
ACCIDENTAL CONTACT WITH LIVE POINTS
CAN CAUSE SHOCK, BURNS AND RESULT
IN DEATH.
Do not try to use the product in any way, before having
read this instruction manual
Figure 2
The following warnings must be respected:
•
READ THE INSTRUCTIONS CAREFULLY BEFORE TRYING TO INSTALL, OPERATE OR REPAIR THE
CIRCUIT BREAKER.
• Store these instructions along with other documents for instruction, maintenance and installation,
drawings and descriptive notes on the circuit-breaker.
• Keep these documents available during the installation, operation and maintenance of the appliance.
The use of these instructions facilitates proper maintenance.
• install the circuit-breaker within the limits of the project described in the instruction manual
shipped with the unit. These circuit-breakers are designed to operate with values of voltage and
current within the limits of plate ratings. Do not install this equipment in systems operating at
nominal values exceeding these limits.
• follow the safety procedures indicated by Your Company.
• Do not open any covers or doors, do not work on devices before removing power from all circuits,
and after making sure of that with a measuring instrument.
WARNING!
• Detailed descriptions of standard procedures for installation, use, maintenance and principles
for safe operation are not included. It is important to note that this document contains safety
instructions and caution against certain methods (installation, operation and maintenance) that
could cause injury to personnel, damage equipment, or make them unsafe.
• these warnings and alarms do not include all the conceivable methods of performing the installation,
operation and maintenance operations recommended by ABB and others, which could be performed,
or the possible consequences and complications of each conceivable method, neither will ABB
investigate all those methods.
• anyone using maintenance procedures or devices, recommended by ABB or not, must check thoroughly
that neither personal safety nor the safety devices are endangered by mode of installation, use,
maintenance or the instruments used. For more information, questions or specific problems contact
your nearest ABB representative.
• This manual is written for qualified personnel only and is not intended as a substitute for a proper
course, or experience about safety procedures for this device.
• regarding products equipped with communication systems, the purchaser, installer or end customer
are responsible for applying all the IT security measures to prevent risks deriving from connection
to communication networks; among others, these risks include use of the product by unauthorized
persons, alteration of its normal operation, access to and modification of the information.
• the purchaser, installer or end customer are responsible for ensuring that safety warnings and
notices are affixed and moreover, that all points of access and operating devices are securely
blocked when the switchgear is left even momentarily unattended.
• all the information contained in this document reflects the latest product information available
at the time of printing. We reserve the right to edit the document at any time and without notice