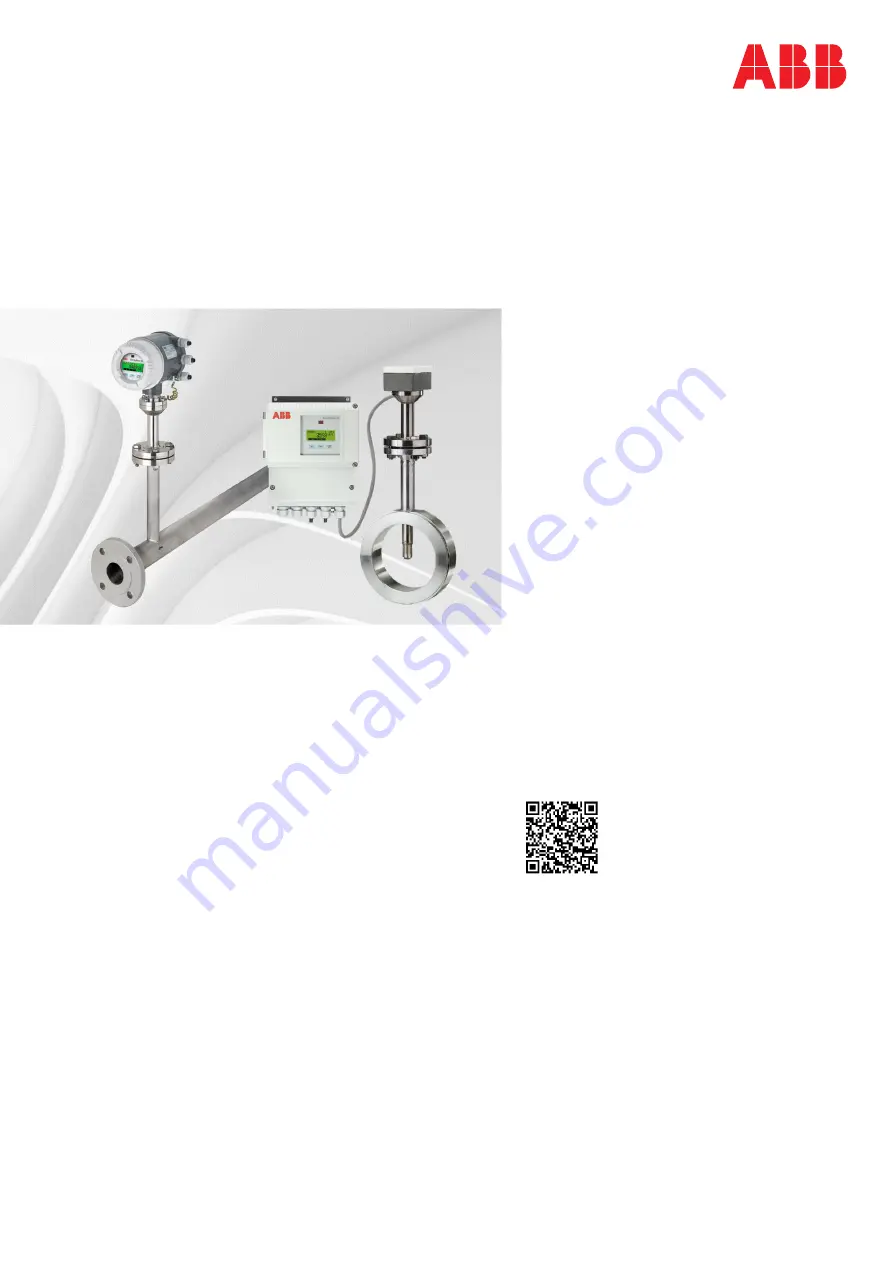
—
A B B M E A S U R E M E N T & A N A L Y T I C S | O P E R A T I N G I N S T R U C T I O N
Sensyflow FMT500-IG
Thermal Mass Flowmeter
—
ABB Limited
Measurement & Analytics
Howard Road, St. Neots
Cambridgeshire, PE19 8EU
UK
Tel: +44 (0)870 600 6122
Fax: +44 (0)1480 213 339
Email: enquiries.mp.uk@gb.abb.com
ABB Automation Products GmbH
Measurement & Analytics
Schillerstr. 72
32425 Minden
Germany
Tel: +49 571 830-0
Fax: +49 571 830-1806
abb.com/flow
ABB Inc.
Measurement & Analytics
125 E. County Line Road
Warminster, PA 18974
USA
Tel: +1 215 674 6000
Fax: +1 215 674 7183
For gas, intelligent analog / HART
PROFIBUS DPV1
Measurement made easy
OI
/F
M
T500-I
G
-E
N Re
v. C
03
.2
019
—
Sensyflow FMT500-IG
Introduction
The Sensyflow FMT500-IG thermal mass
flowmeter is a digital mass flowmeter for air, gas
and gas mixtures in process applications. The
measuring system is equipped with a LCD
display, integrated gas temperature
measurement and counter functions.
Additional Information
Additional documentation on
Sensyflow FMT500-IG is available for download free
of charge at www.abb.com/flow.
Alternatively simply scan this code:
—
We reserve the right to make technical changes or modify the contents of this document
without prior notice. With regard to purchase orders, the agreed particulars shall prevail.
ABB does not accept any responsibility whatsoever for potential errors or possible lack of
information in this document.
We reserve all rights in this document and in the subject matter and illustrations contained
therein. Any reproduction, disclosure to third parties or utilization of its contents – in whole
or in parts – is forbidden without prior written consent of ABB.
© ABB 2019
3KXF421008R4201