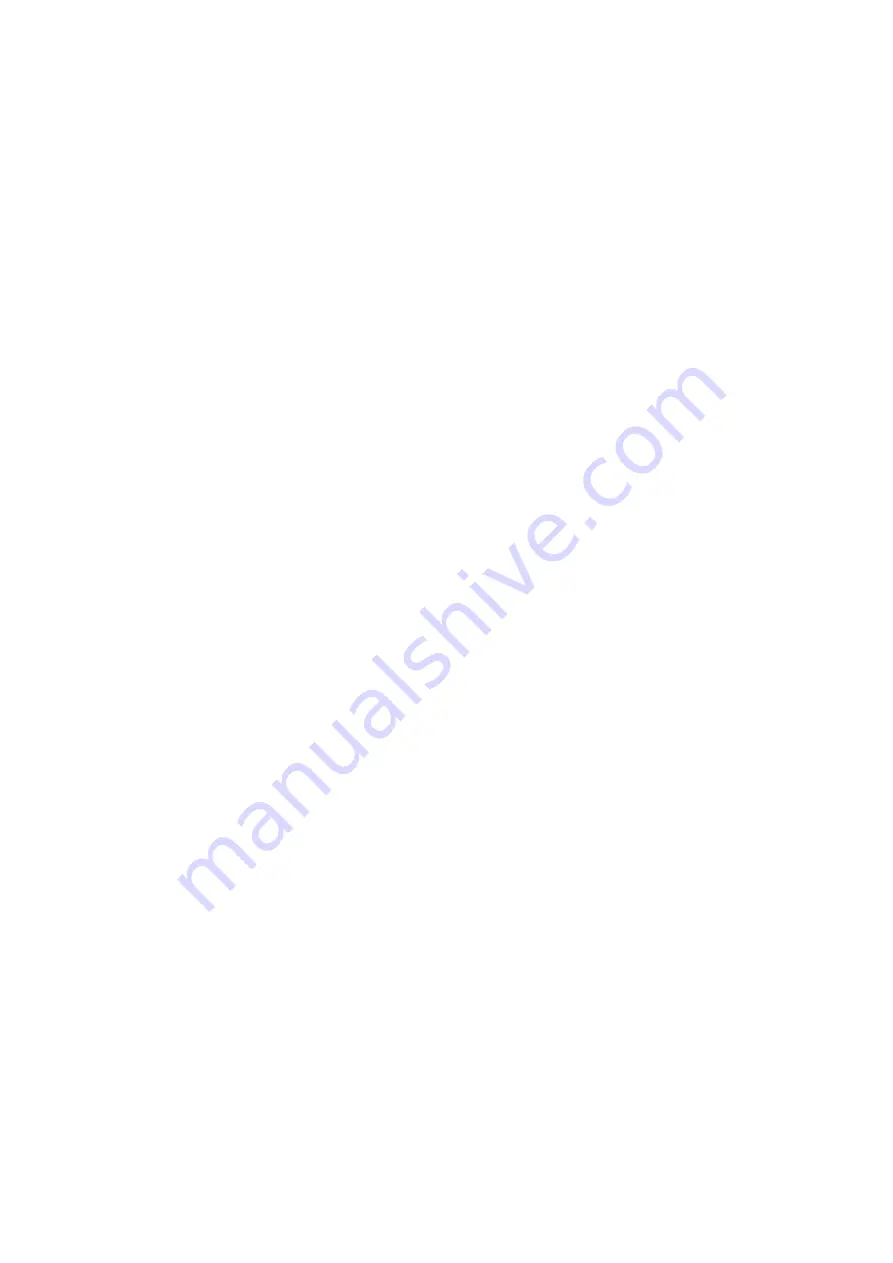
6
vides a latching function after any trip opera-
tion. After having latched the output relay must
be manually reset or reset by remote control.
The trip alarm signals from the relay module are
obtained via output relays B and C. The signals
to be routed to these relays are selected with
switches1...7 of switchgroup SGR1 and switches
4...8 of switchgroup SGR2 of the relay module.
Normally the output relays B and C are given
such a configuration that a thermal prior alarm
is obtained over relay C and the trip signals of
the protection units are linked to output relay B
to form an auxiliary trip signal. This is also the
default setting of the relay on delivery from the
factory.
The signals to be routed to the output relay D
are selected with switches 1, 2 and 3 of software
switchgroup SGR2 in the main menu of the
relay module. Switch SGR2/1 routes the ther-
mal prior alarm, switch SGR2/2 routes the
startup information for the motor and switch
SGR2/3 routes the start signal of the high-set
overcurrent stage to output relay D.
Output relay E, terminals 74-75, is a heavy duty
output relay capable of controlling a circuit
breaker, as the main trip relay A. Relay E is used
for controlling the restart of the motor. If the
thermal capacity used exceeds the set restart
inhibit level of the thermal unit, if the allowed
maximum cumulative start-up count is exceeded
or if the external restart inhibit signal is active
the output relay E prevents a motor restart
attempt. This also applies to a condition where
the protective relay is out of auxiliary voltage or
the relay is faulty.
Output relay F, terminals 70-71-72, operates as
the output relay of the integrated self-supervi-
sion system. The relay operates on the closed-
circuit principle, thus under normal service con-
ditions the contact gap 70-72 is closed. If a fault
is detected by the self-supervision system, or if
the auxiliary supply fails, the output relay drops
off, providing an alarm signal by closing the NO
contact 71-72.
The relay is connected to the SPA data bus by
means of bus connection module type SPA-ZC
17 or SPA-ZC21. The bus connection module
is connected to the D type connector marked
SERIAL PORT on the rear panel of the relay.
The fibre-optic cables are connected to the
connectors Tx and Rx of the bus connection
module. The communication mode selector
switches on the bus connection module are set
in position "SPA".
The three phase currents are connected to ter-
minals 1-2, 4-5 and 7-8, when the rated current
of the secondary circuits is I
n
= 5 A. When using
current transformers with a rated current of 1 A,
terminals 1-3, 4-6 and 7-9 are used. The ther-
mal overload protection may also be used in
single-phase or two-phase applications, in this
case inputs not used may be left unconnected.
To get a proper operation of the unbalance and
incorrect phase sequence protection in a two-
phase application, the two phase currents should
be summed in the third phase current input. In
single-phase applications, wiring the phase cur-
rent through two or three current inputs in series
may slightly increase the operating speed of the
relay and stabilize operation of the thermal unit.
The neutral current of the earth-fault protection
is connected to terminals 25-26 when the rated
current is 5 A and to terminals 25-27 when the
rated current is 1 A.
The control input 10-11 can be used in five
different ways:
- as the control input controlled by a motor
speed switch in Ex-type applications
- as the control input of an external blocking
signal for blocking the operation of the unbal-
ance or earth-fault protection units
- as the control input for an external trip signal
- as the control input for unlatching the trip relay
- as the control input for the restart enable relay.
The designed function is selected by means of
switches 1...8 of switchgroup SGB in the main
menu of the protection relay module.
The auxiliary supply voltage of the relay is
connected to the terminals 61-62. At d.c. auxil-
iary supply voltage the positive lead is connected
to terminal 61. The accepted input voltage
range is determined by the type of power supply
and output relay module inserted in the relay
case. For further details see the description of the
power supply module. The accepted auxiliary
voltage range of the relay is indicated on the
front panel.
Output relay A provides the CB tripping com-
mands when the operate time of a protective
unit has elapsed. The earth-fault unit can be
made non-tripping, i.e. only signalling, with
switch 8 of switchgroup SGR1. On delivery from
factory all protective units are selected to per-
form tripping. A latching function of the output
relay A can be selected by means of switches
SGB/7 and SGB/8. Switch SGB/7 gives a latch-
ing function after a short-circuit, an earth-fault
or an unbalance tripping. Switch SGB/8 pro-
Connections