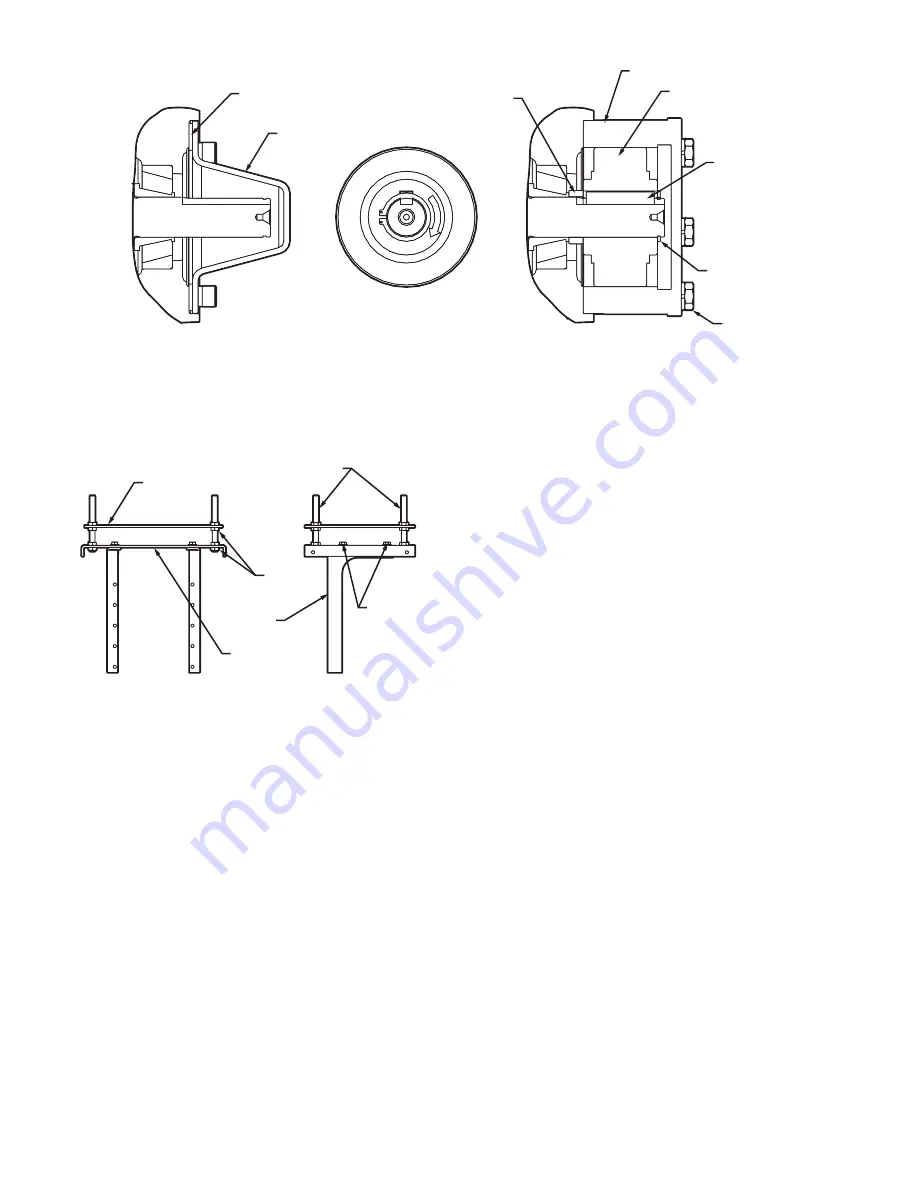
10
SPACER (IF APPLICABLE)
BACKSTOP SHAFT
COVER GASKET
REDUCER WITH
BACKSTOP INSTALLED
REDUCER WITHOUT
BACKSTOP INSTALLED
ARROW ON HUB OF INSTALLED
BACKSTOP MUST MATCH
DIRECTION OF DESIRED
SHAFT ROTATION
RETAINING
RING
BACKSTOP
FASTENERS
BACKSTOP
KEY
OUTER RACE
INNER RACE
BACKSTOP
SHAFT COVER
Figure 12 - Backstop Assembly
MOTOR MOUNTS
Motor Mount Assembly:
JAM
NUTS
TOP PLATE
ADJUSTING
STUDS
BOTTOM
PLATE
BOLTS
UPRIGHTS
BOTTOM
PLATE
Figure 13 – Motor Mount Components
Refer to Figure 12 for descriptions of component parts. Using
the hardware provided, assemble uprights (the angled parts
to which the reducer is fastened) to the u-shaped, rectangular
bottom plate. Notice that there are eight slots cut into the plate.
If the reducer is to be mounted in Positions A or C, as illustrated
in Figure 8, assemble the uprights in the outermost slots. If
the reducer is to be mounted in Positions B or D, assemble
the uprights in the innermost slots. The bottom plate may be
mounted with the vertical flanges up or down (as shown in
Figure 11). Snug bolts only, do not torque bolts at this time.
Fasten long threaded studs to the four corners of bottom plate
using jam nuts, one on each side of the plate. Securely tighten
these nuts, as they will not require any further adjustment. Add
ne additional jam nut to each stud and thread approximately
to the middle of the stud. Assemble top motor plate (the flat
rectangular plate with many holes) on top of the jam nuts.
Assemble the remaining jam nuts on studs to secure top motor
plate. Do not fully tighten these nuts yet.
The motor mount may be installed in any of the four positions
(A, B, C or D) and in any of the mounting levels (M1, M2, M3 or
M4) shown in Figure 12. Note that the motor mount uprights
attach to the input side of the reducer when mounted in either
the “B” or “D” positions.
Motor Mount Installation:
WARNING: To ensure that drive is not unexpectedly
started, turn off and lock out or tag power source before
proceeding. Remove all external loads from drive before
removing or servicing drive or accessories. Failure to
observe these precautions could result in bodily injury.
Remove four or six (as required) housing bolts from the reducer.
Place the motor mount in position and reinstall the bolts
through the motor mount uprights and reducer housing. Where
reducer is shaft mounted in positions A or C, the torque-arm
adapter plate must be mounted between the reducer housing
and the motor mount upright. Tighten bolts to the torque
specified in Table 12.
Mount the motor onto the top plate and bolt securely. Install the
motor sheave and reducer sheave as close to the motor and
reducer housings as practical. Loosen the bottom plate bolts
and slide the motor and mounting plate to accurately align the
motor and reducer sheave. Securely tighten the bottom plate
bolts. Install the required number of V-belts and tension belts
by alternately adjusting the jam nuts on the four adjusting studs
provided on the motor mount. Check all bolts to see that they
are securely tightened. Verify that the V-belt drive is properly
aligned before operating the reducer.
Summary of Contents for TA0107L
Page 31: ...31 ...