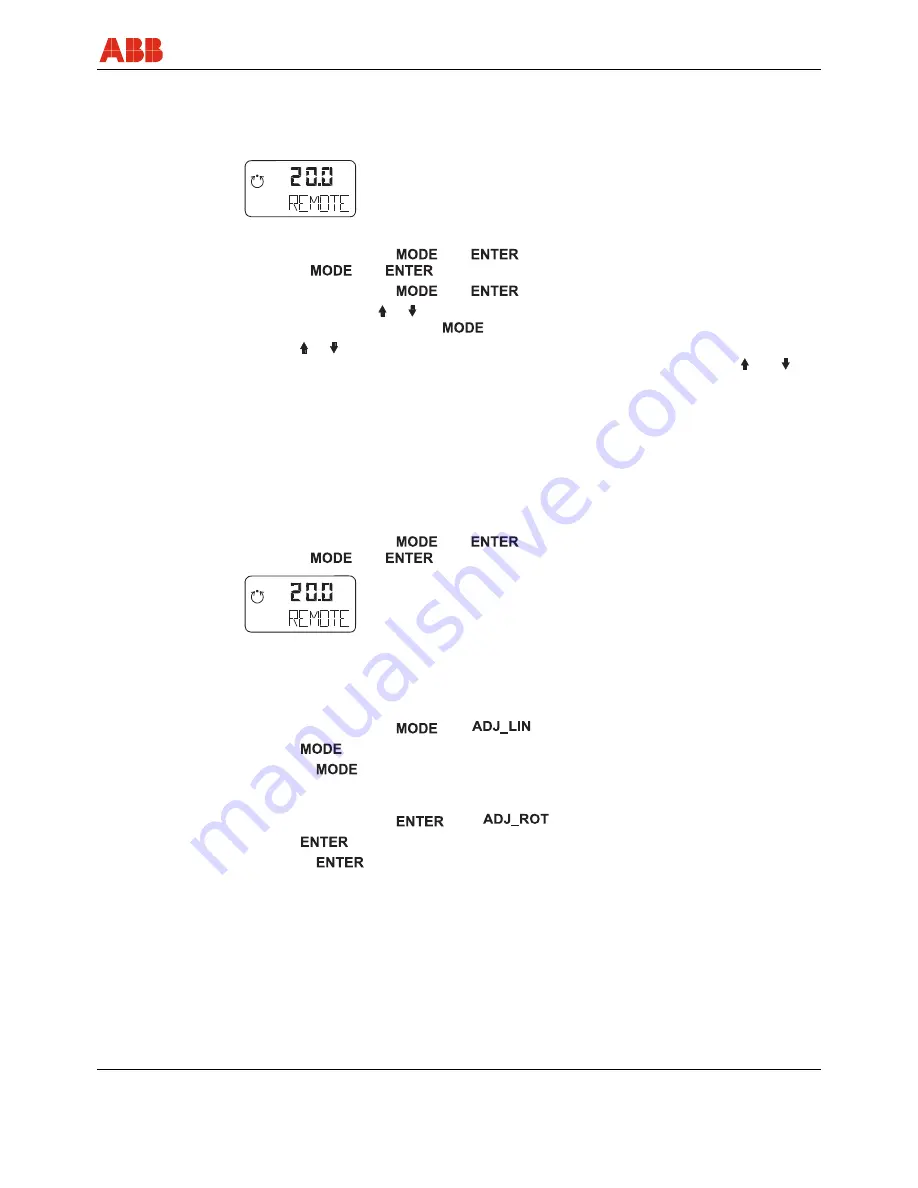
Commissioning
CI/TZIDC/110/120-EN
TZIDC, TZIDC-110, TZIDC-120
33
6.2
TZIDC-110 / TZIDC-120
bieten
1.
Feed in pneumatic supply power
2.
Connect the bus to the bus terminals with any polarity (or supply power 9 ... 32 V DC)
is displayed
3.
Check mount:
• Press and hold down
and
; once the countdown has gone from 3 to 0,
release
and
; the unit switches to the operating level, mode 1.x
• Press and hold down
and
.
• Additionally, press or until operating mode 1.3 (manual adjustment within the sensor
range) is displayed. Release
• Press or to move the actuator into the mechanical end position; check the end
positions; rotation angle is displayed in degrees (for high-speed mode, press and
simultaneously)
Recommended range:
- between -28 ... 28° for linear actuators
- between -57 ... 57° for rotary actuators
Minimum angle: 25°
4.
Go back to the bus level:
• Press and hold down
and
; once the countdown has gone from 3 to 0,
release
and
is displayed.
5.
Run Autoadjust
• Check that the unit is on the bus level ("REMOTE")
For linear actuators
1)
:
• Press and hold down
until
is displayed. Release the control button
• Press
again and hold down until the countdown ends
• Release
; this starts Autoadjust
For rotary actuators
1)
:
•
Press and hold down
until
is displayed. Release the control button
•
Press
again and hold down until the countdown ends
•
Release
; this starts Autoadjust
mA
%
C
°
mA
%
C
°
Summary of Contents for TZIDC
Page 46: ...Ex relevant specifications 46 TZIDC TZIDC 110 TZIDC 120 CI TZIDC 110 120 EN...
Page 47: ...Ex relevant specifications CI TZIDC 110 120 EN TZIDC TZIDC 110 TZIDC 120 47...
Page 48: ...Ex relevant specifications 48 TZIDC TZIDC 110 TZIDC 120 CI TZIDC 110 120 EN...
Page 57: ...Ex relevant specifications CI TZIDC 110 120 EN TZIDC TZIDC 110 TZIDC 120 57...
Page 58: ...Ex relevant specifications 58 TZIDC TZIDC 110 TZIDC 120 CI TZIDC 110 120 EN...
Page 67: ...Ex relevant specifications CI TZIDC 110 120 EN TZIDC TZIDC 110 TZIDC 120 67...
Page 68: ...Ex relevant specifications 68 TZIDC TZIDC 110 TZIDC 120 CI TZIDC 110 120 EN...
Page 70: ...Appendix 70 TZIDC TZIDC 110 TZIDC 120 CI TZIDC 110 120 EN...