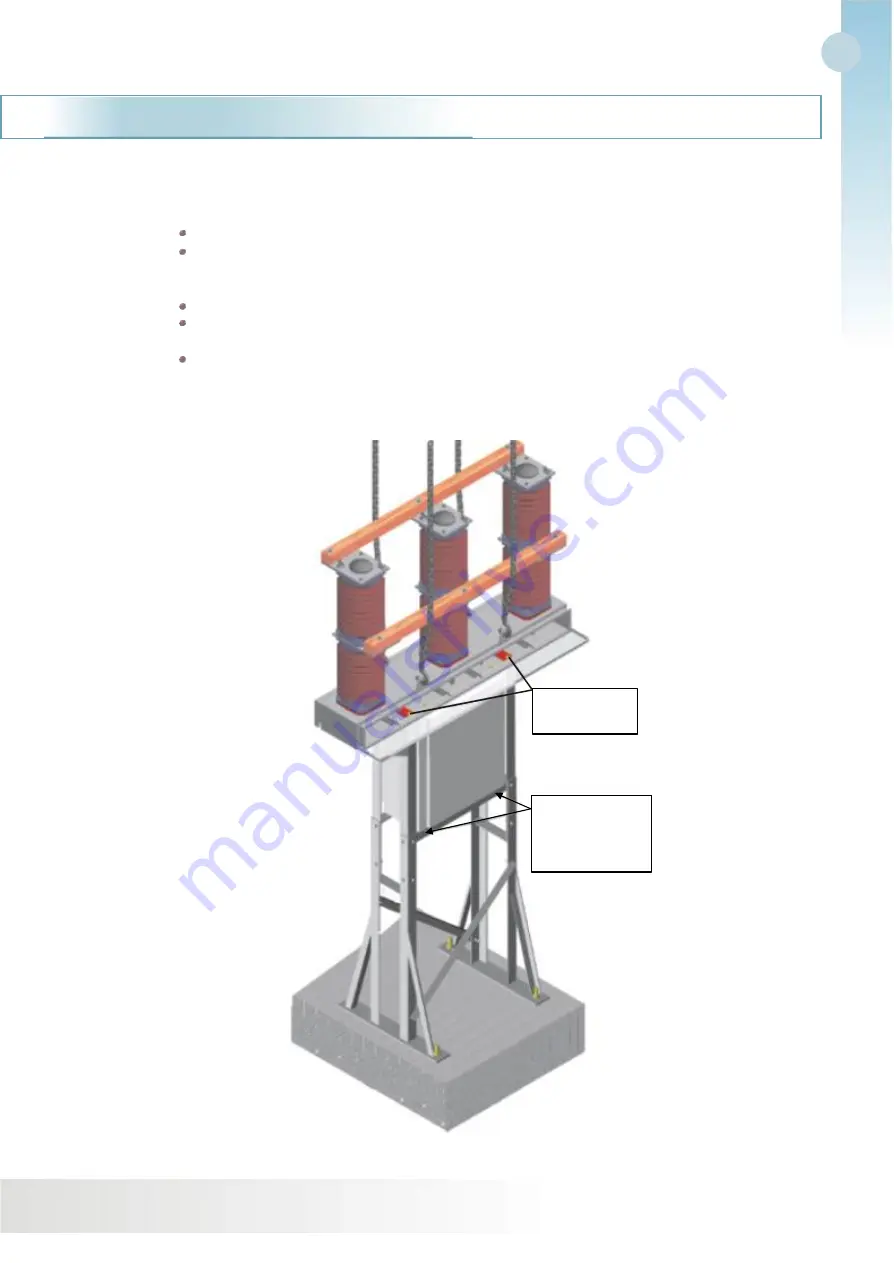
18
PART B Installation, Operation & Maintenance
4.2.1.6 Assembly of entire Circuit-Breaker on structure
Refer figure below before going for assembly.
Slowly lower the Circuit-Breaker in such a way that the Cabinet enters inside the Upper
Leg Assemblies & rests on the support angles & the Duct rests on the Upper Leg
Assemblies of structure.
Ensure that stiffener plates are placed inside the duct and assemble with structure.
Engage Cabinet with the support angles. Fix M12 bolts, spring washers, plain washers
from bottom of the support angles. [M12 Nuts are welded inside the cabinet]
This completes the assembly.
Now fasten all hardware; do not remove slings until all hardware are fastened fully.
Fixing the Breaker on the structure
Fix Cabinet with Duct
Assembly on support-
angles & fix M12 bolts,
washer & Spring
Washer from bottom
Ensure that stiffener
plates are placed
inside the duct.