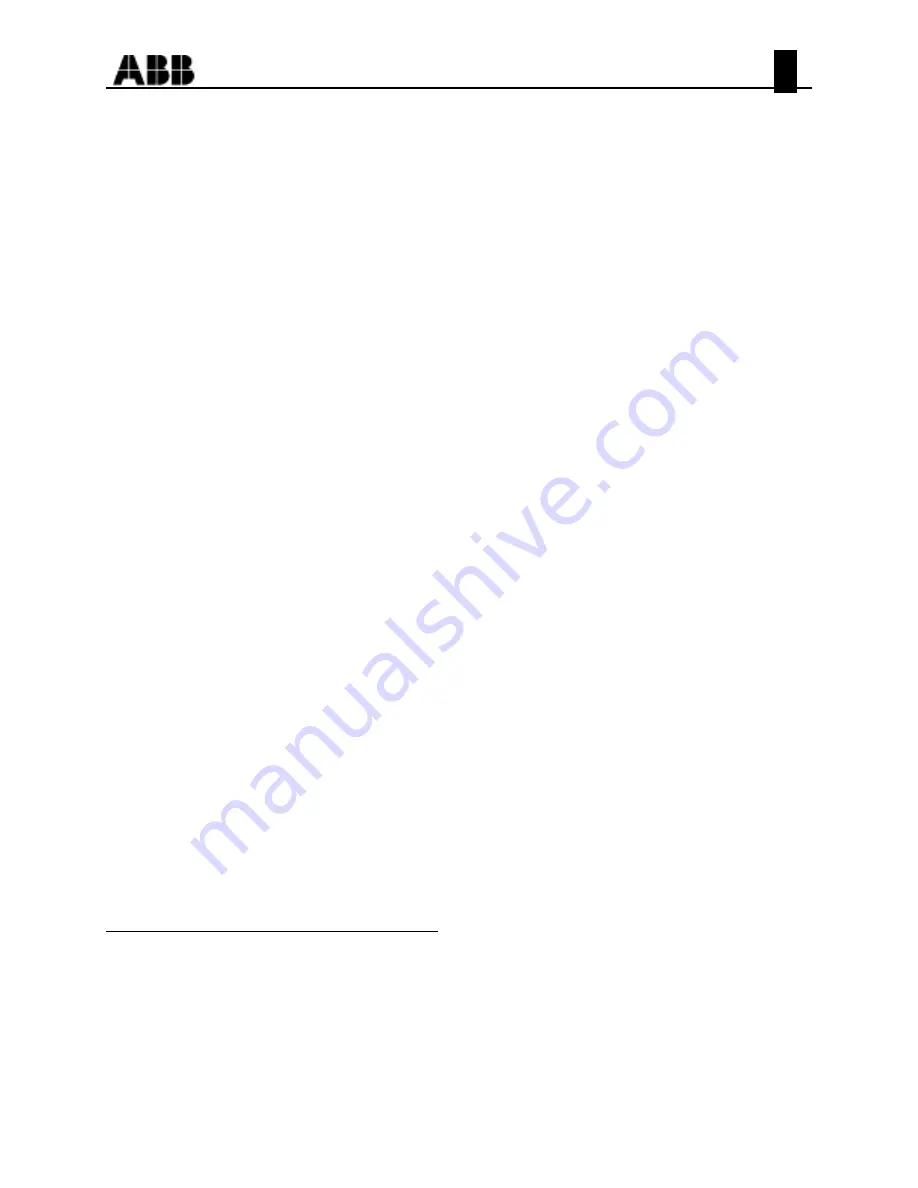
IB 6.2.7.7-3I
9
Removal From TEST Position
1. Turn the Release Lever to the left, rotate the
Crank one-quarter (¼) turn counterclockwise,
and then release the Release Lever. It will
again remain in the
released
position.
Continue Cranking counterclockwise until
Racking Mechanism automatically stops at the
DISCONNECT position.
Removal From DISCONNECT Position
1. Turn the Rack Release Lever to the left, and
turn Crank counterclockwise one-quarter (¼)-
turn. Release the Rack Release Lever. It will
again remain in the released position.
Continue cranking counterclockwise until a
resistance is felt (approximately 2-3 turns) (Do
Not Force.) The breaker is now in the
WITHDRAW position.
If the Closing Springs were previously
charged, they will automatically discharge as
the Racking Mechanism reaches the
WITHDRAW position.
2. The circuit breaker can now be removed from
the compartment by pulling on the handle
located on the Front Barrier.
Safe Operations Recommendations
It is recommended that any circuit breaker be
withdrawn and stored in the withdrawn position
whenever it is to be maintained in the OPEN
position with no planned switching.
It is recommended that a Ground & Test Device
(a.k.a. G&T Device) be connected to the proper
compartment when any work is to be done on any
bus or feeder circuit. See section "Ground and
Test Devices" for a description.
ADJUSTMENTS, TESTS AND
PERIODIC MAINTENANCE
The circuit breakers are designed and tested to
insure minimum maintenance. The few
adjustments that are noted are required only when
an operational check indicates a problem. Of
course, during the maintenance checks, all
accessible bolts, units and screws should be
routinely checked to insure that they are tight.
It is recommended that the circuit breaker be
inspected after the first 1000 mechanical
operations and on a yearly basis unless
environmental considerations and operating
experience indicate that more or less frequent
inspections are appropriate.
Vacuum interrupters, as used on the VHK vacuum
circuit breakers, have an inherently long contact
life and will provide trouble-free service under
varied application conditions as long as the circuit
breaker is applied within its rating. The
interrupters have been tested up to 2000% KSI
minimum. It is unlikely that a circuit breaker will
be subjected to this much duty in its life, and it is
not expected that the interrupters will have to be
replaced due to excessive contact erosion.
The wear condition of the individual vacuum
interrupters will vary, however, depending on
circuit conditions and such variables as single
phase versus three-phase interruption, X/R ratio
(asymmetry) and relay delay times. Therefore, the
interrupters in all three phases may not erode
equally. Additionally, interrupting high short-circuit
current will cause contact erosion to occur faster
than load current interruptions.
There is, however, a check for Contact Wipe
(Contact Spring overtravel), which is a measure of
contact erosion. This check is covered under the
subsection "Contact Wear and Contact Pressure."
When Contact Wipe is less then the minimum
specified and there is not any mechanical
problem, the interrupter should be replaced due to
contact erosion.
If, after the first inspection period, there is no
indication of any problems, actual operating
experience with specific circuits will indicate the
future amount of maintenance needed for the
various circuit breakers, and the procedure can be
modified as required.
Where unusual service conditions exist, as
covered by ANSI Standard C37.04, it must be
presumed that these conditions were considered
at the time of order, the equipment supplied was