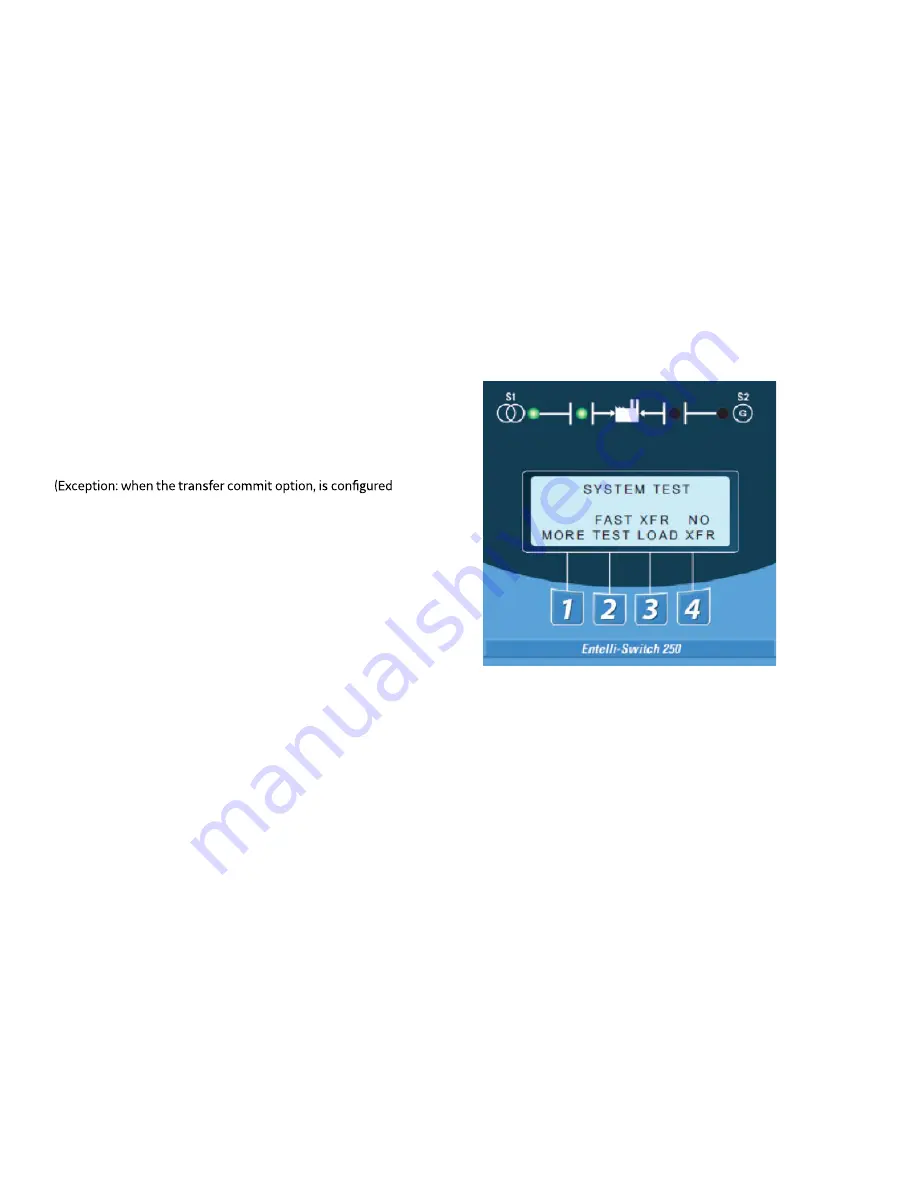
14
Zenith Automatic Transfer Switch | new.abb.com/low-voltage
ATS Testing
Start generator and verify proper voltage, frequency and phase
sequence (match to Source 1). Shut down gen set and place
in Auto. Complete the visual inspection of the transfer switch,
and close the cabinet door. Initiate the test by pressing the TEST
button on the LCD keypad. The controller will then prompt for
your access code. After entering the code, three test options
will appear - XFR LOAD, FAST TEST and NO XFR (See Figure S4-10).
• XFR LOAD test starts the generator and using the
current timer settings, transfers the load to Source 2.
• FAST TEST test presets timer values to a maximum
30 seconds during the test. After completion
of the test, all timers are reset to their original
values. (T3, W3, DT and DW remain)
• NO XFR test starts the generator but does
not transfer the load to the Source 2.
Press and hold the desired test option button until the switch
transfers to Source 2 (load test) or until the generator has been
run for the desired amount of time (no load test). Releasing
the test button before W timer timeout will abort the test
“ON”). To test lamps, press TEST then scroll through MORE,
then press LAMP TEST. To cancel LAMP TEST press MORE.
Standard Transition
When the test is initiated, the controller initiates the Time
Delay Source 2 Start Timer (Engine Start Timer “P”) cycle.
A manual CANCEL button is provided to cancel the test if
desired. Upon completion of the (P) time delay, an Engine
start Signal is sent to Source 2. When Source 2 voltage
and frequency reach the preset “Restore” Values, the time
delay to Source 2 Timer (W) begins its timing cycle to ensure
voltage and frequency stabilization before transfer. A manual
pushbutton BYPASS is provided to bypass the “W” time delay
if desired. After the (W) time delay, the MX controller initiates
a transfer signal through the Relay Driver Module to operate
the main transfer operator. The load is now transferred to
Source 2 line. The transfer switch is mechanically locked.
SN limit switch awaits the next operation to Source 1.
Restoration of Source 1 Power:
Deactivating the test switch initiates re-transfer to Source
1 sequence. The delay to Source 1 Timer (T) begins its timing
cycle to ensure voltage and frequency stabilization before
retransfer. A manual pushbutton BYPASS is provided to bypass
the “T” time delay if desired. After the (T) time delay, the MX
controller initiates a transfer signal through the Relay Driver
Module to operate the main transfer operator. The load is now
transferred to Source 1 line. The transfer switch is mechanically
locked. SE limit switch awaits the next operation to Source 2.
Immediately after re- transfer, the S2 Stop Delay Timer (Delay
to Engine Stop “U”) begins its cycle to allow Source 2 Engine
to run unloaded. A manual pushbutton BYPASS is provided to
bypass the “U” time delay if desired. Upon completion of the
(U) timing cycle, the controller sends an Engine stop signal.
Figure S4-10 : MX250 Controller HMI