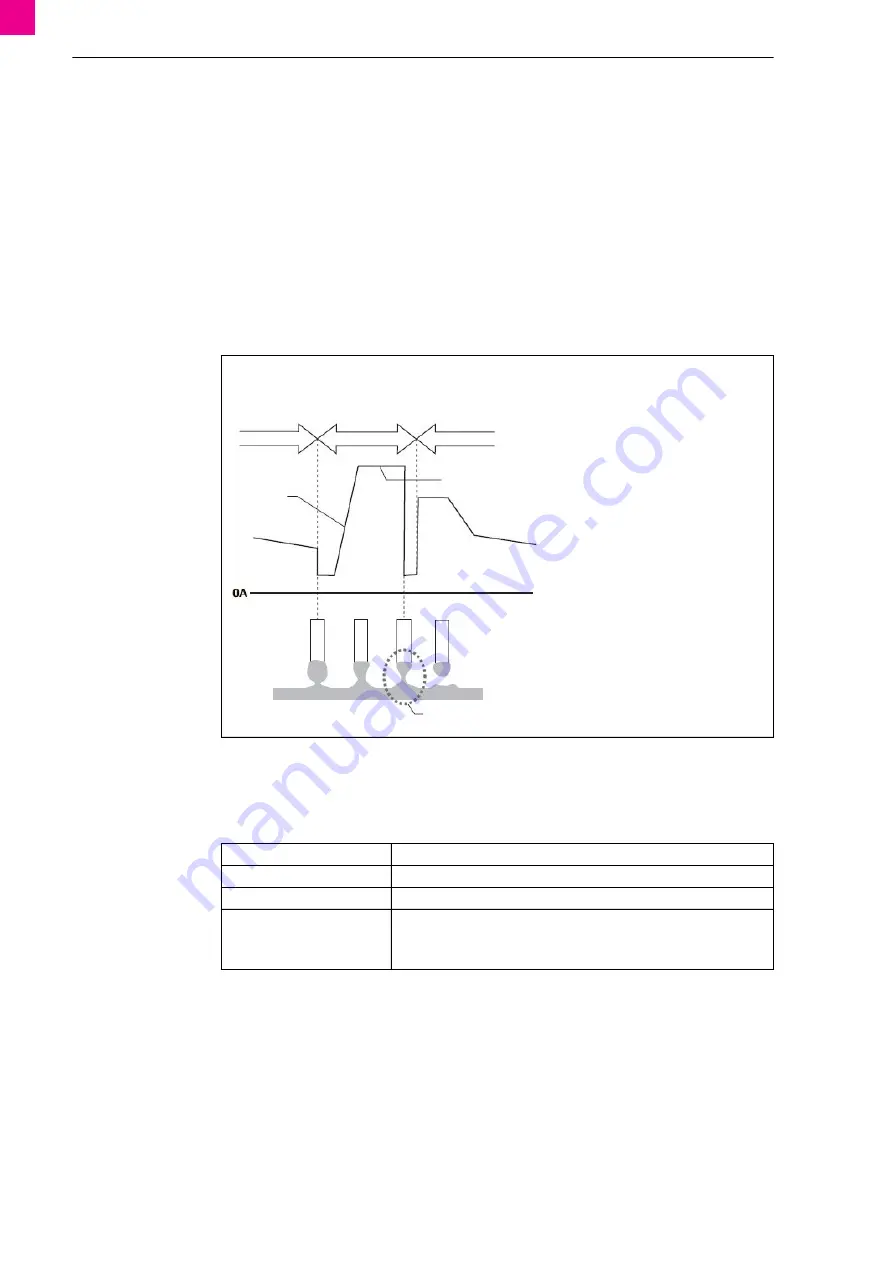
EN
-
40
7 Operation
iROB
®
501, iROB
®
401, iROB
®
301
F33: Displaying the necking detection blocking ratio
Any shift in necking detection leads to increased spatter formation. This function makes it possible to check
the blocking ratio for necking detection from the time welding starts to the time it ends. If the internal function
is selected after the welding process ends, the blocking ratio is displayed in the right digital display.
The welding process can be performed if F33 is selected.
If the arc becomes unstable, necking may also become unstable as a result. If this occurs, check the welding
parameters. If the blocking ratio is 70% or less, adjust the sensitivity using functions F36/F37 (spatter
adjustment) even if the arc is stable.
In short arc welding, where the short circuit and arc alternate, most spatter is produced when the short circuit
occurs immediately before the arc. The time immediately before the arc is called necking and is shown
below. Detecting this necking and quickly reducing the welding current at the correct moment prevents
molten material from being flung out by the force of the arc, thus minimizing spatter. Therefore, necking must
be detected as accurately as possible.
F34: Automatically correcting the necking detection sensitivity
Although the necking detection sensitivity is set for each welding procedure and for each welding wire
diameter, it depends on factors such as welding environment (line lengths and routing), welding position,
parameters and weld shape. An inaccurate setting leads to an increase in spatter.
Fig. 13
Necking
A
Arc
B
Short circuit
C
Short circuit current increase period 1
D
Current progression
E
Short circuit current increase period 2
F
Necking
E
C
D
A
B
A
F
Adjustable range
ON/OFF
Default value
ON
Storage option
Yes
Description
OFF: Automatic correction of necking detection sensitivity deactivated.
The F36/F37 functions can be used to fine-tune necking detection.
ON: Automatic correction of necking detection sensitivity activated.