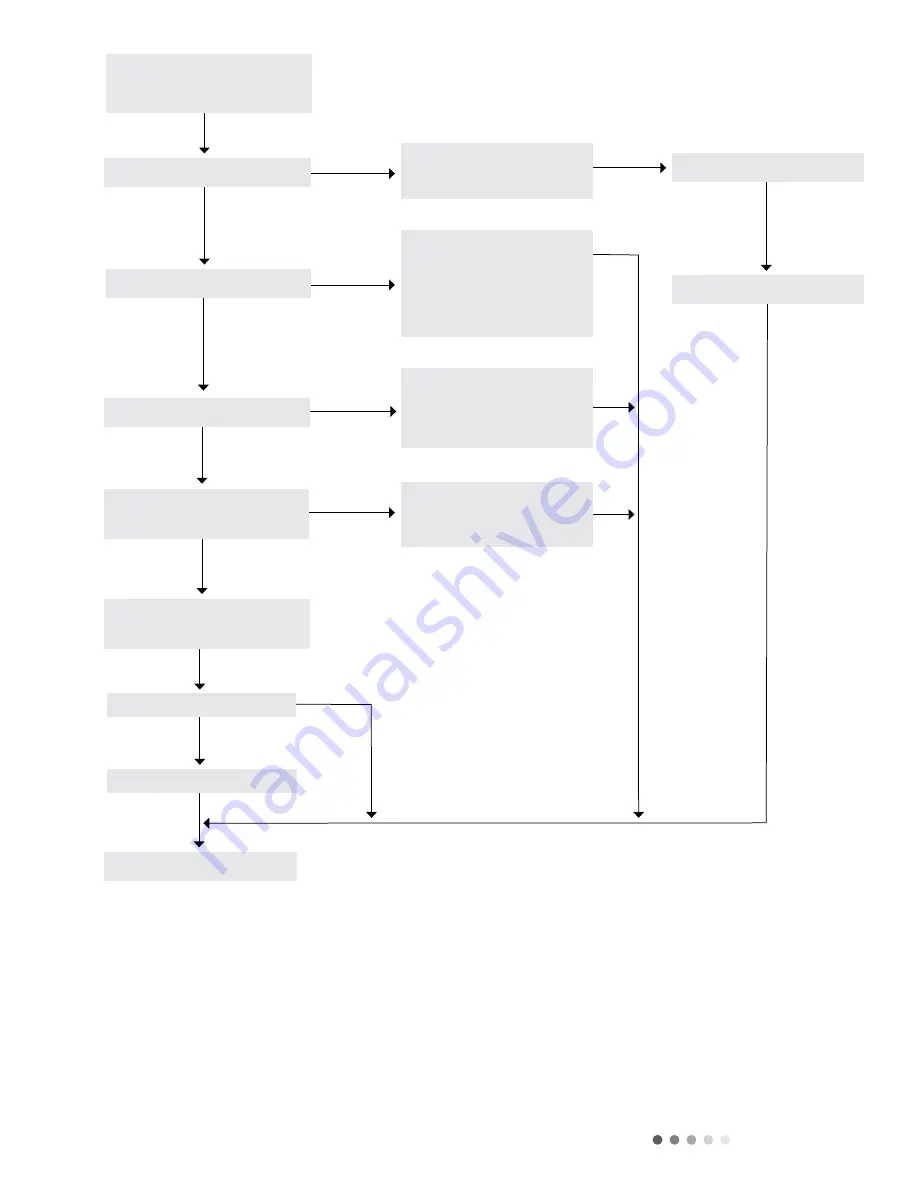
27
Technical Information
Unit radiation is good?
Desynchronizing happens
during operation
Outdoor unit is working?
End
Replace the outdoor
mainboard
Input voltage is normal?
Refrigerant amount is too
much?
NO
Eliminate the malfunction
YES
YES
Replace the compressor
Check if fan terminal is
connected well
Improve radiation
situation of the unit
(such as cleaning the
heat exchanger, improve
ventilation
Turn on the unit after
the power supply voltage
resumes normal
Charge refrigerant
according to the service
manual
Replace the outdoor unit
Replace the fan capacitor
NO
NO
YES
YES
NO
NO
YES