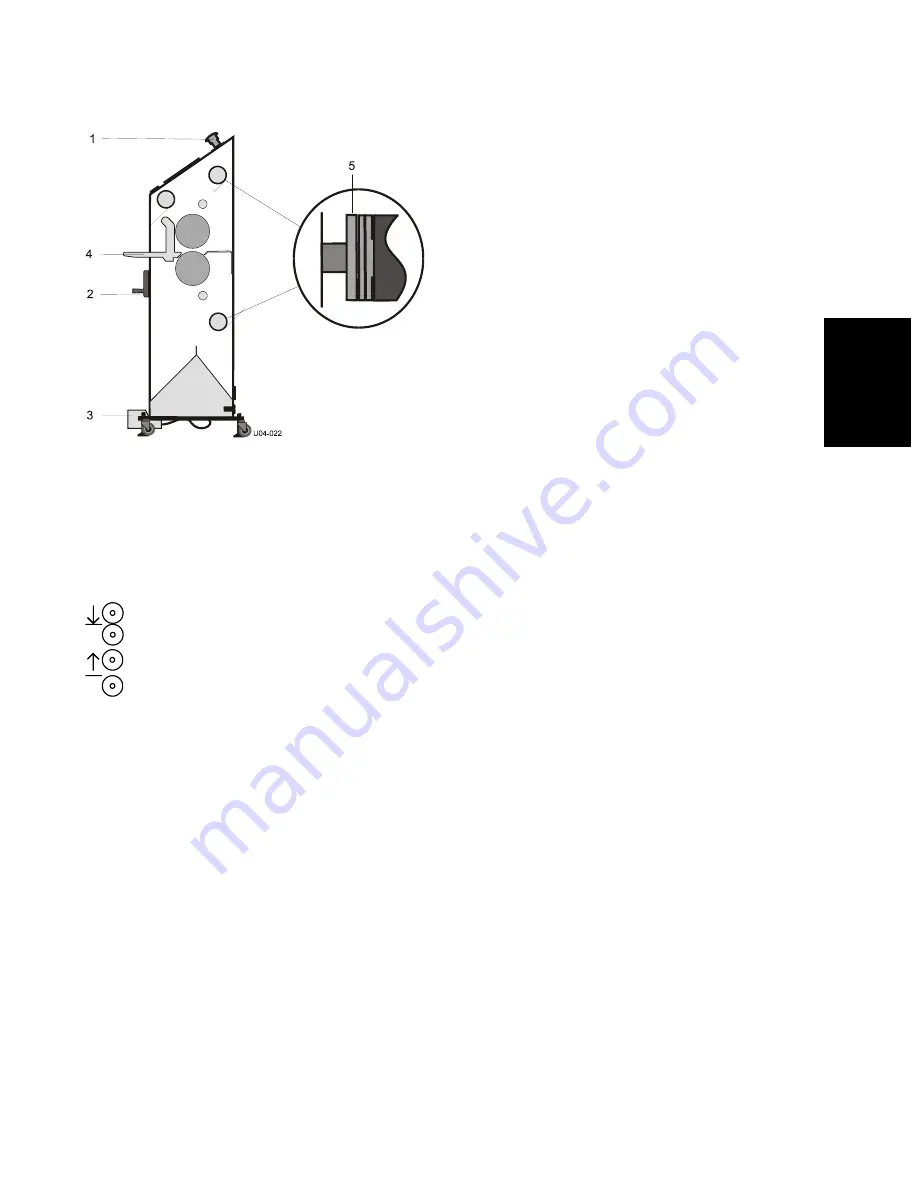
Operating
19
Engl
is
h
4.1.2
Additional controls
Figure 9: Additional controls
Emergency stop buttons (1)
, push and hold button;
When pressed the rotation of the rolls is stopped immediately and the button is locked into this stop
position. The safety indicator LED will flash while the button is depressed.
Turn the button to unlock it.
Pressing start, reverse or pressing the footswitch starts the process again.
Nip setting wheel (2)
, geared wheel;
Turn the wheel clockwise to narrow (close) the nip and set pressure or
counter-clockwise to release pressure and widen (open) the nip.
When both rollers touch the materials, the pressure is set. By turning the wheel clockwise the
pressure is increased. Turning the nip setting wheel counter-clockwise the pressure will decrease.
The pressure is indicated on the control panel by 4 LED’s.
Foot switch (3)
, snap switch;
Press and hold the switch to start the rotation of the rolls. Insert the forefoot completely to disable
the safety lock that prevents accidental starting.
When the switch is released, the rotation of the rolls will stop.
In-feed table (4)
The in-feed table can swing up around the pivot point at the top of the table arms.
The image guide is clamped to the table arms and can be removed by pulling it forward from its
retaining blocks.
Unwind tension control (5)
, ring;
By turning this ring counter-clockwise (top to rear) an amount of friction is set between the shaft and
the frame, so this will act as a brake.
Tightening the brake will apply more tension to the material on the shaft.
Turning the ring clockwise (top to front) will release the brake and therefore release the tension.