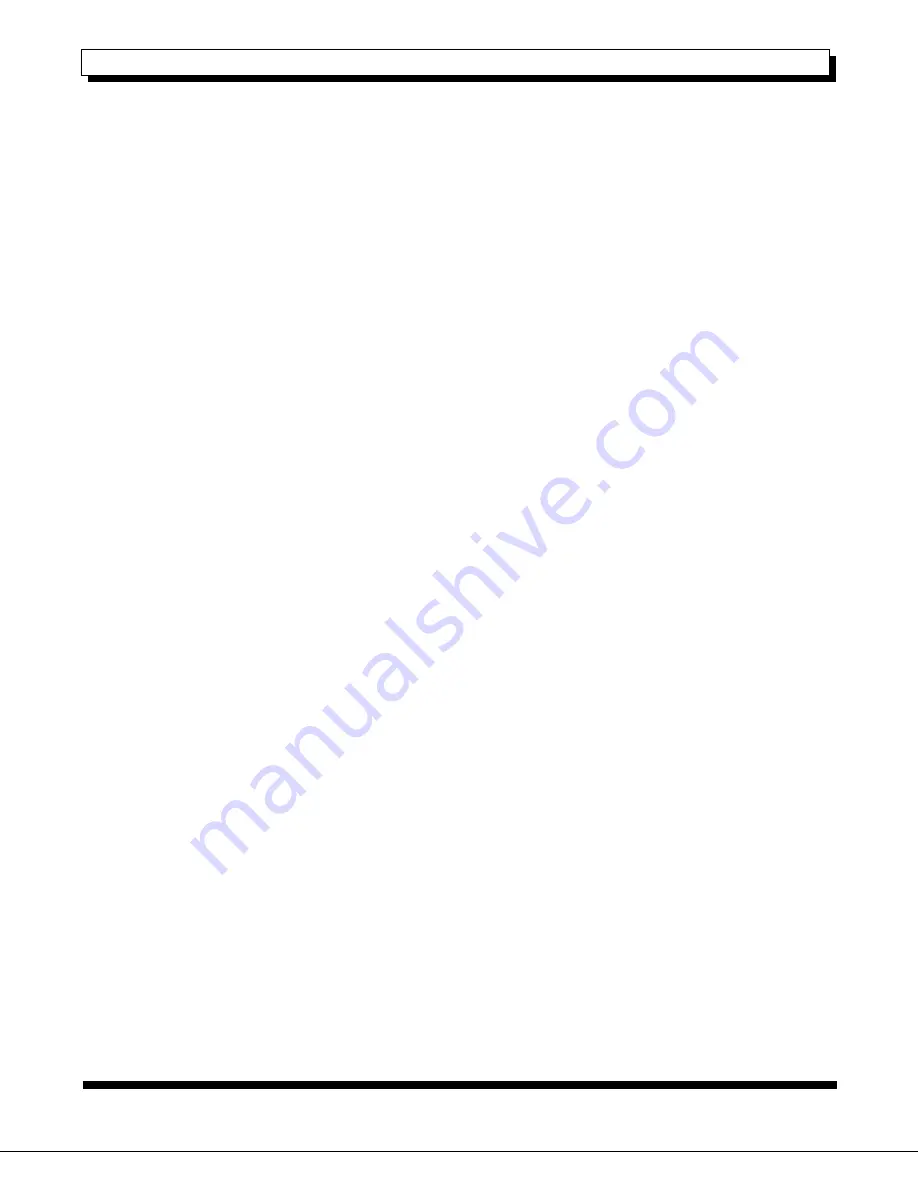
- 4 -
4
©
Copyright 2003 Accuspray Application Technologies, Inc., Cleveland, Ohio USA
800-618-6860 or 440-498-9677 Fax: 440-498-9815
V M X
®
Owners Manual
Operation Instructions Cont.:
7. System pressure has now been set. System
pressure is not atomizing pressure or material
pressure. These pressures are independently
controlled at the pot and spray gun respectively.
System pressure ensures smooth operation at both
regulators and compensates for any pressure drop
when system is in use.
8. To set fluid pressure use the regulator on top of
the pressure pot. Make sure to complete step 5 first.
Operating pressure range is between 5 and 50 psi.
Do not exceed 80 psi.
9. To set atomizing air pressure use the regulator
on the bottom of the spray gun. Always adjust
atomizing air with the trigger pulled (active air).
HVLP compliant pressure range is between zero
and 43 psi.
Note: This is a 4.3 to 1 ratio HVLP conversion gun.
43 psi into the spray gun regulator yields 10 psi at
the air cap.
Shut down and Clean Up Instructions:
Always relieve all pressure from the entire system
before attempting any clean up.
1. Turn unit off.
2. Remove pressure from the pot by unscrewing the
pressure relief screw on top of the pot lid.
3. Disconnect the supply air hose at the compressor
using the quick disconnect.
4. Always flush the system with a solvent that is
compatible with the coating you have sprayed.
5. Pressurize the system to flush the fluid line and
spray gun.
6. Always drain all fluid from system and store dry.
7. Always drain all air from tanks and open drain
cock to remove and prevent moisture build up.
8. See the spray gun portion of this manual for
additional care instructions.
Pressure Settings:
The following instructions are to be used as
guidelines on how to correctly set the pressure on
your VMX
®
system. Proper settings are crucial to
achieve quality finishes while cutting down on
overspray and compressor run time. Always keep
the outlet pressure regulator (located at the
compressor) as close to 90 psi as possible. This
regulates system pressure and keeps both the fluid
and air regulators operating smoothly.
Fluid pressure should be set first; this is done using
the regulator located on top of the pressure pot,
which controls fluid pressure only. A good rule of
thumb is to shut off the atomizing air completely
while adjusting fluid pressure. This is done by
turning the spray gun regulator to zero.
Trigger the gun fully open and hold spray gun
parallel with the floor. Increase fluid pressure until
you achieve a 6 to 12 inch fluid stream that is
parallel with the floor. The stream should hold
steady 6 to 12 inches and then curve towards the
floor. The pressure needed to achieve this stream is
your proper fluid pressure and will vary greatly
depending on the viscosity of the fluid used as well
as the size of the atomizing kit used.
Adjust atomizing air at the spray gun air regulator
(located directly below the gun). Once fluid pressure
is set simply increase air pressure until you have a
uniform fully wet pattern when the gun is held 6 to 8
inches from the spray surface. Maximum gun
pressure should not exceed 43 psi active air. Gun
pressure is always measured at active air levels
(gun triggered open). This gun has a two-stage
trigger pull; the first half of trigger travel releases air,
fluid is released later. This lets you adjust active air
levels without triggering fluid. Minor atomizing
adjustments are handled at the spray gun; see the
spray gun portion of this manual for instructions.
Remember, proper patterns are achieved through
a balance of air pressure and fluid pressure. These
pressures vary greatly from coating to coating and
can be affected by temperature. Pressures may
also need to be increased if hose length is increased
or when spraying from ladders at increased heights.
Do not add fluid hose. Extend the air supply hose
between the compressor and pressure pot to
increase overall distance from the compressor
system.
Listed below are some common pressure ranges
for popular materials.
Lacquers:
Fluid Pressure: 8 to 15 psi
Air pressure: 15 to 22 psi
Oil-based Enamels:
Fluid pressure: 12 to 25 psi
Air pressure: 17 to 30 psi
Most Latexes:
Fluid pressure: 25 to 45 psi
Air pressure: 25 to 43 psi
Multi-color Coatings:
Fluid pressure: 25 to 45 psi
Air pressure: 20 to 43 psi
These pressures are starting points only. Always
spray at the lowest possible pressure. Thinning is
not required on most materials. However, we
recommend heavy latexes be thinned between 5
and 15 percent to improve system performance. For
best results use the proper atomizing set for the
viscosity of the material being sprayed as follows.
Fine finish (light bodied):
Prokit-35
Medium (oils and latex enamels): Prokit-37(supplied)
Heavy (multi colors and latex): Prokit-36