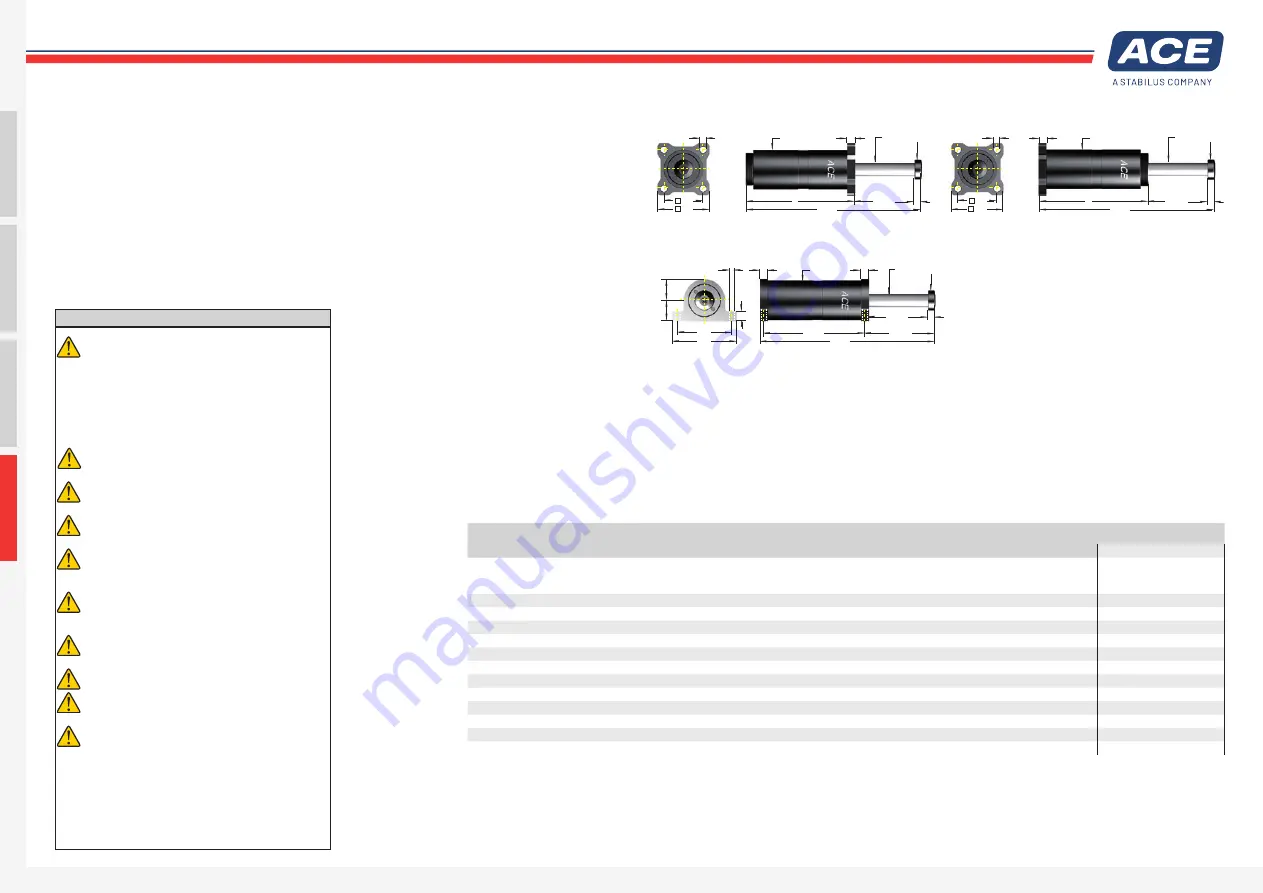
ACE Stoßdämpfer GmbH · Postfach 1510 · D-40740 Langenfeld · T +49 (0)2173 - 9226-10 (Technik -20) · F +49 (0)2173 - 9226-19 · info@ace-int.eu · www.ace-ace.com
Stand 03.2021
ACE Stoßdämpfer GmbH · www.ace-ace.com
21_22_0019 Issue 05.2022
4
Performance data and dimensions
Mounting type
TYPES
1
Energy capacity
Nm/cycle
1
Reacting force
N
Return Force min.
N
Return Force max.
N
Stroke
mm
A max.
mm
B
mm
D
mm
E max.
mm
F and R
Weight
kg
S
Weight
kg
SDH50-100EU
14,500
160,000
1,000
1,200
100
416
297
258
139
23.5
25.0
SDH50-150EU
21,800
160,000
1,000
1,200
150
516
347
308
189
26.0
27.5
SDH50-200EU
29,100
160,000
1,000
1,200
200
616
397
358
239
28.5
30.0
SDH50-250EU
36,400
160,000
1,000
1,200
250
731
462
423
289
32.0
33.5
SDH50-300EU
43,600
160,000
1,000
1,200
300
831
512
473
339
34.5
36.0
SDH50-350EU
50,900
160,000
1,000
1,200
350
931
562
523
389
37.0
38.5
SDH50-400EU
58,200
160,000
1,000
1,200
400
1,046
627
588
439
40.0
41.5
SDH50-500EU
72,700
160,000
1,000
1,200
500
1,261
742
703
539
46.0
47.5
SDH50-600EU
87,300
160,000
1,000
1,200
600
1,476
857
818
639
52.0
53.5
SDH50-700EU
101,800
160,000
1,000
1,200
700
1,691
972
933
739
58.0
59.5
SDH50-800EU
116,400
160,000
1,000
1,200
800
1,906
1,087
1,048
839
64.0
65.5
SDH50-1000EU
145,500
160,000
1,000
1,200
1,000
2,336
1,317
1,278
1,039
75.0
76.5
1
The values apply to mounting style Front Flange and Foot Mounting. For mounting style Rear Flange, please consult ACE.
In case of an existing side load angle, please consult ACE.
Installation instructions
Before installation and use check whether the identification num-
ber on the damper or on the packaging matches the respective
designation on the delivery note.
Operating temperature range:
-20 °C to +60 °C
Mounting:
As required but always in such a way that the entire
damper stroke is used. The dampers must always be mounted
in such a way that the forces are introduced centrally over the
piston rod in the damper. The maximum side load angle must
not be exceeded. Safety dampers must not be exchanged from
one installation site to another if the conformity of the throttle
characteristic curve is not ensured.
Packaging disposal
Please dispose of the transportation packaging in an environ-
mentally-friendly manner. Recycling packaging materials saves
raw materials and reduces waste. The packaging materials do not
contain any prohibited materials.
Emergency stop application:
After an emergency stop, check
that the piston rod returns to the initial position, the damper is not
leaking and the mounting elements are properly secured. Make
sure that no damage has occurred to the piston rod, the body, or
the mounting hardware.
Regular start-up:
Safety shock absorbers can be regularly
started up with 100 % stroke utilisation with a creep speed of 1/10
of the max. impact velocity.
Checking:
A regular check should take place at an interval of
no
more than three months
.
Commissioning
First impacts on the shock absorber should only be tried after
correctly mounting and with reduced impact velocity and – if
possible – with reduced load. Differences between calculated and
actual operating data can then be detected early on, and damage
to the system can be avoided. If the safety dampers were selected
on calculated data that does not correspond to the maximum
possible loading (i.e. selection based on drive power being
switched off or at reduced impact velocity) then these restricted
impact conditions must not be exceeded during initial testing
or subsequent use of the system. Otherwise you risk damaging
the shock absorbers and/or machine by overstressing materials.
After the initial trial, check that the piston rod fully extends again
and that there are no signs of oil leakage. Also check that the
mounting hardware is still securely tightened. Make sure that no
damage has occurred to the piston rod, the body, or the mounting
hardware.
70
20
B
Stroke
A max
20
Ø
140
180
18
Ø
133
Ø
45
Ø
70
20
B
Stroke
A max
20
Ø
140
180
18
Ø
133
Ø
45
Ø
35
D ± 1
E max
Stroke
A max
20
35
190
225
22
Ø
73
72
40
133
Ø
45
Ø
70
Ø
SDH50-R Rear Flange
SDH50-S Foot Mount
SDH50-F Front Flange
WARNING
Take particular care that the customer-specific
identification number at the end of the damper designation
matches the number on the delivery note. The field data
to be read from the type plate, such as moving mass and
maximum impact velocity, must be compared with the
technical design. This ensures that the damper is the right
size for its use. Otherwise you risk damaging the shock
absorbers and/or machine by overstressing materials.
The gas accumulators of the SDH38 to SDH63 safety shock
absorbers are filled with nitrogen ex works. The respective
filling pressure (5 bar) can be found on the damper
label. The dampers may only be operated with this filling
pressure. A reduced filling pressure can lead to serious
malfunctions.
During installation of the dampers, moving masses can
lead to injuries due to inadvertent starting. Secure moving
masses against inadvertent moving.
The dampers may be unsuitable for use and have an
insufficient damping effect. Check the specific suitability
of the dampers before installation.
If operated outside of the operating temperature range,
the damper can lose its function. Operating temperature
range must be maintained. Do not paint dampers due to
heat emission.
Fluids, gases and dirt particles in the surrounding area can
attack or destroy the seal system of the damper and cause
it to fail. Protect or encapsulate piston rod and seal system
from external materials in the surrounding area.
Damage to the piston rod surface can destroy the seal
system. Do not grease, oil piston rod etc. and protect
against dirt particles.
The piston rod can be torn from the damper. Do not load
the piston rod with tensile stress.
Damper can tear off upon impact. Always lay out the
connection structure in such a way that the maximum
occurring forces can be absorbed with sufficient safety.
Safety shock absorber check after a damper impact.
Check that the piston rod returns to the initial position,
the damper is not leaking and the mounting elements are
properly secured.
Mounting accessories
If using accessory parts and mounting elements, note the respec-
tive separate mounting instructions for accessories.
Mounting instructions and mounting accessories
Safety Shock Absorbers SDH50 (high rack damper, optimised characteristic)