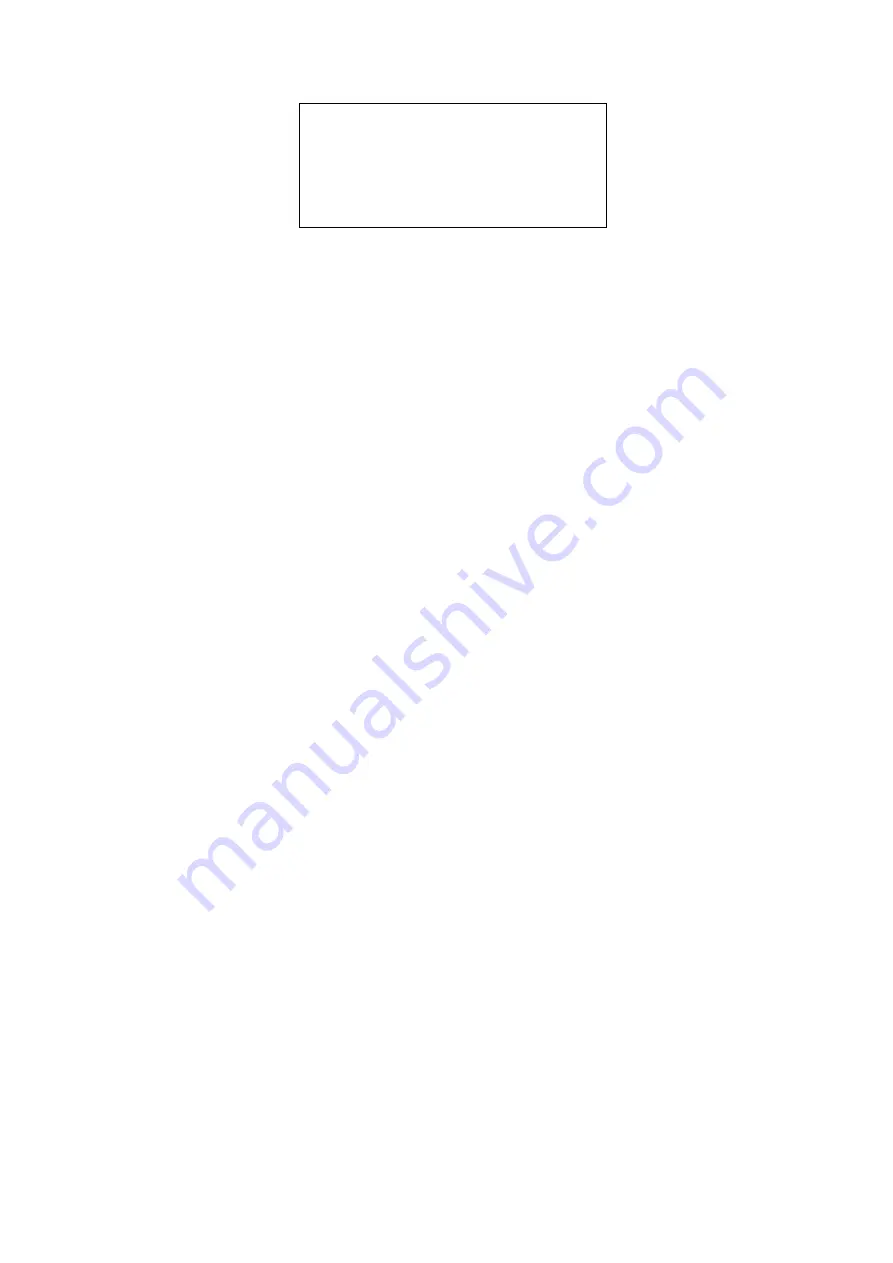
ACER
OPERATION MANUAL
Precision Flat Bed CNC Lathe
Model: ATL 1840E
Taiwan: Ya-Gin Machine Tool Manufacturing, Inc.
No. 101, 506 Lane, Seng-Tso Road
Seng Karng District, Taichung City, Taiwan
Tel: 886-4-2520-4120 Fax: 886-4-2520-4123
CA: Springwood Industrial, Inc.
2320 E. Valencia Drive
Fullerton, CA 92831
Tel: 714-871-5558 Fax: 714-871-5554
NJ: Klim Industrial, Inc.
244 N. Randolphville Rd.
Piscataway, NJ 08854
Tel: 732-752-9100
Fax: 732-752-9101
Revision: 3/10/16
Summary of Contents for ATL 1820E
Page 5: ...1 SAFETY INSTRUCTIONS ...
Page 22: ...Page 1 17 ...
Page 24: ...2 MACHINE SPECIFICATIONS ...
Page 25: ...Page 2 1 2 MACHINE SPECIFICATIONS 2 1 Dimensional drawing ...
Page 27: ...Page 2 3 2 1 2 Chip Conveyor ...
Page 31: ...3 INSTALLATION ...
Page 34: ...3 1 2 Layout floor plan Following is a top view drawing ...
Page 43: ...4 MAINTENANCE ...
Page 55: ...5 CHUCK ...
Page 64: ...Page 7 3 7 1 HEADSTOCK 1 HEADSTOCK _ 18 SPINDLE BORE 58mm 2 ...
Page 65: ...Page 7 4 18 SPINDLE BORE 58mm 2 ...
Page 69: ...Page 7 8 7 2 BED Z AXIS TRANSMISSION ...
Page 71: ...Page 7 10 7 3 CARRIAGE CROSS SLIDE ...
Page 74: ...Page 7 13 7 4 TAILSTOCK MANUAL TAILSTOCK _ 18 ...