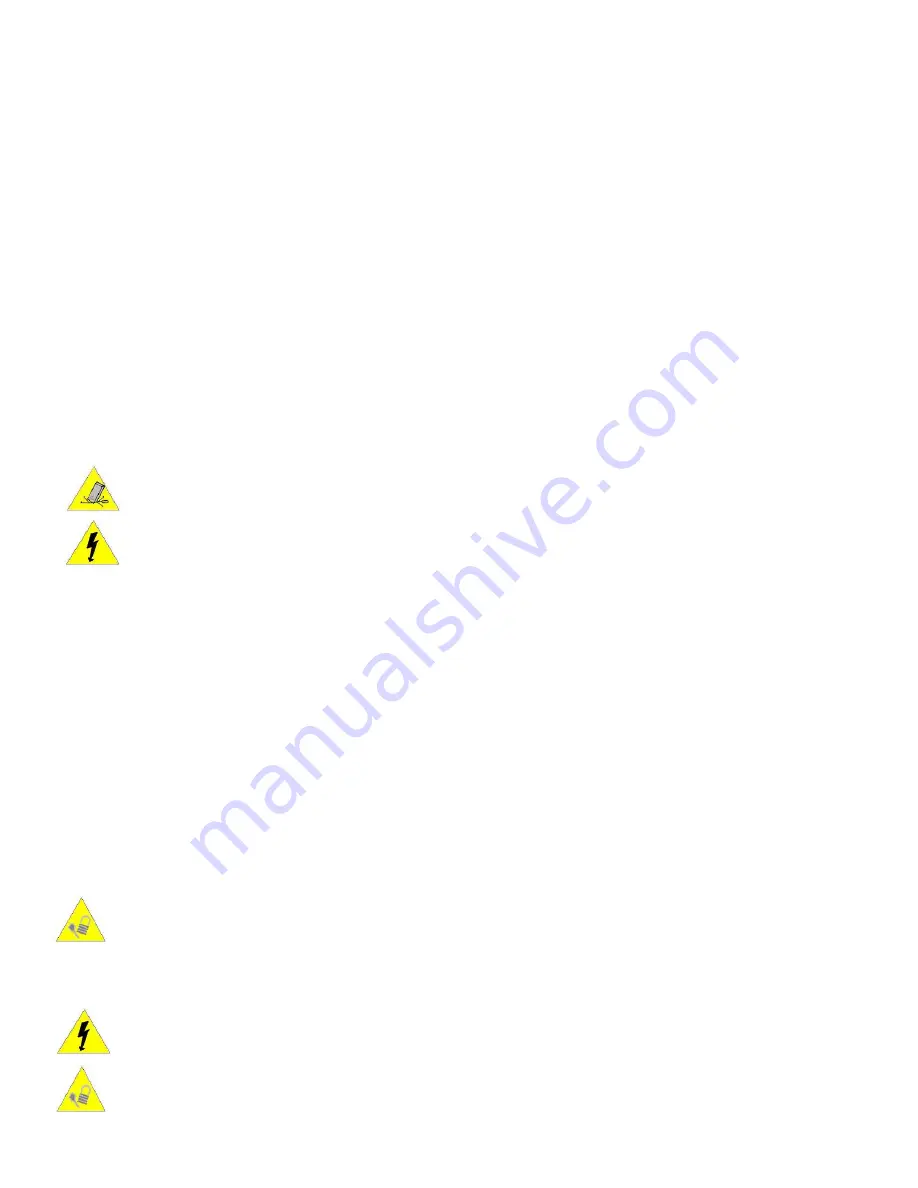
13
Tag-out all controls and energy sources which cannot be locked out. All personnel affected
must know about and understand all lockout tags.
Verify that all energy sources have been accounted for before performing any maintenance
or service work.
When restarting equipment, all lockout/tag-out devices must be removed by the person
who installed it.
3.5 EMERGENCY STOP
The E-Stop is the first line of defense to stop a machine from operating. This button halts operation of the
machine and may be used for emergency situations or general shut down. When using the button for non-
emergency shutdowns it is important to wait until the machine is not in a cycling mode as the emergency
brake system will rapidly stop the Gantry if it is in motion.
The emergency stop does not remove power
to the machine
. Follow lockout/tag-out procedure prior to any service or maintenance.
3.6 SETUP
The following procedures are designed to maximize safety and machine life:
Make sure a properly rated forklift is used to unload your machine and follow all unloading
instructions in this guide.
Do not operate machine until all components are located correctly and anchor bolted to
the concrete floor.
Before making electrical connections, verify the incoming voltage correctly matches the
factory set voltage of the WoodRunner.
3.7 OPERATION
OPERATION OF MACHINE
is to be performed by qualified and trained personnel only. Before operating the
machine a safety check should be performed to verify the machine is ready for use and is operating
correctly.
3.8 SAFETY WHILE SERVICING
ADJUSTMENTS AND SERVICING
is to be performed by trained personnel only. A safety check should be
performed upon completion of adjustments or servicing to determine that the equipment is operating
correctly.
3.9 PNEUMATIC SAFETY
Make sure machine is properly locked out when servicing. When servicing the pneumatic system
maintain a clean working area and environment to minimize contamination potential. Keep all spare
pneumatic parts in sealed proper containers until needed to minimize contamination.
3.10 ELECTRICAL SAFETY
Make sure machine is properly locked when servicing. Do not attempt to change or modify the
electrical system without first consulting and obtaining approval from a qualified person. Any
Summary of Contents for Wood Runner
Page 5: ...5 ...
Page 36: ...36 ...
Page 37: ...37 ...
Page 54: ...54 ...
Page 55: ...55 10 DETAILED PARTS IDENTIFICATION WOOD RUNNER 10 1 RUNWAY ASSEMBLY ...
Page 58: ...58 10 3 RUNWAY DRIVE ASSEMBLY ...
Page 61: ...61 10 5 GANTRY ASSEMBLY ...
Page 62: ...62 GANTRY ASSEMBLY ...
Page 64: ...64 10 6 PICKING HEAD ASSEMBLY ...
Page 65: ...65 PICKING HEAD ASSEMBLY ...
Page 68: ...68 10 7 ELECTRICAL PANEL ASSEMBLY ...
Page 70: ...70 10 8 GANTRY ENCLOSURE ASSEMBLY ...
Page 72: ...72 10 9 CONSOLE ASSEMBLY ...
Page 73: ...73 CONSOLE ASSEMBLY ...
Page 75: ...75 10 10 AIR SUPPLY ASSEMBLY ...
Page 77: ...77 10 11 GANTRY VALVE ASSEMBLY ...
Page 79: ...79 10 12 GANTRY BRAKE ASSEMBLY ...
Page 81: ...81 11 ELECTRICAL DIAGRAMS 11 1 SYSTEM OVERVIEW ...
Page 82: ...82 11 2 MAIN ENCLOSURE LOW VOLTAGE ...
Page 83: ...83 11 3 GANTRY WIRING LOW VOLTAGE ...
Page 84: ...84 11 4 I O CHART ...
Page 85: ...85 11 5 INFEED WIRING LOW VOLTAGE ...
Page 86: ...86 11 6 OPERATORS CONSOLE ...
Page 87: ...87 11 7 MAIN ENCLOSURE HIGH VOLTAGE ...
Page 88: ...88 11 8 MAIN ENCLOSURE RECEPTACLE WIRING ...
Page 89: ...89 11 9 SAFETY CIRCUIT LAYOUT ...
Page 90: ...90 11 10 SAFETY CIRCUIT DIAGRAM ...
Page 91: ...91 11 11 BRAKE SENSOR DIAGNOSIS ...
Page 92: ...92 12 PNEUMATIC DIAGRAMS 12 1 SINGLE HEAD GANTRY ...
Page 93: ...93 12 2 DOUBLE HEAD GANTRY ...
Page 94: ...94 12 3 INFEED DECK ...