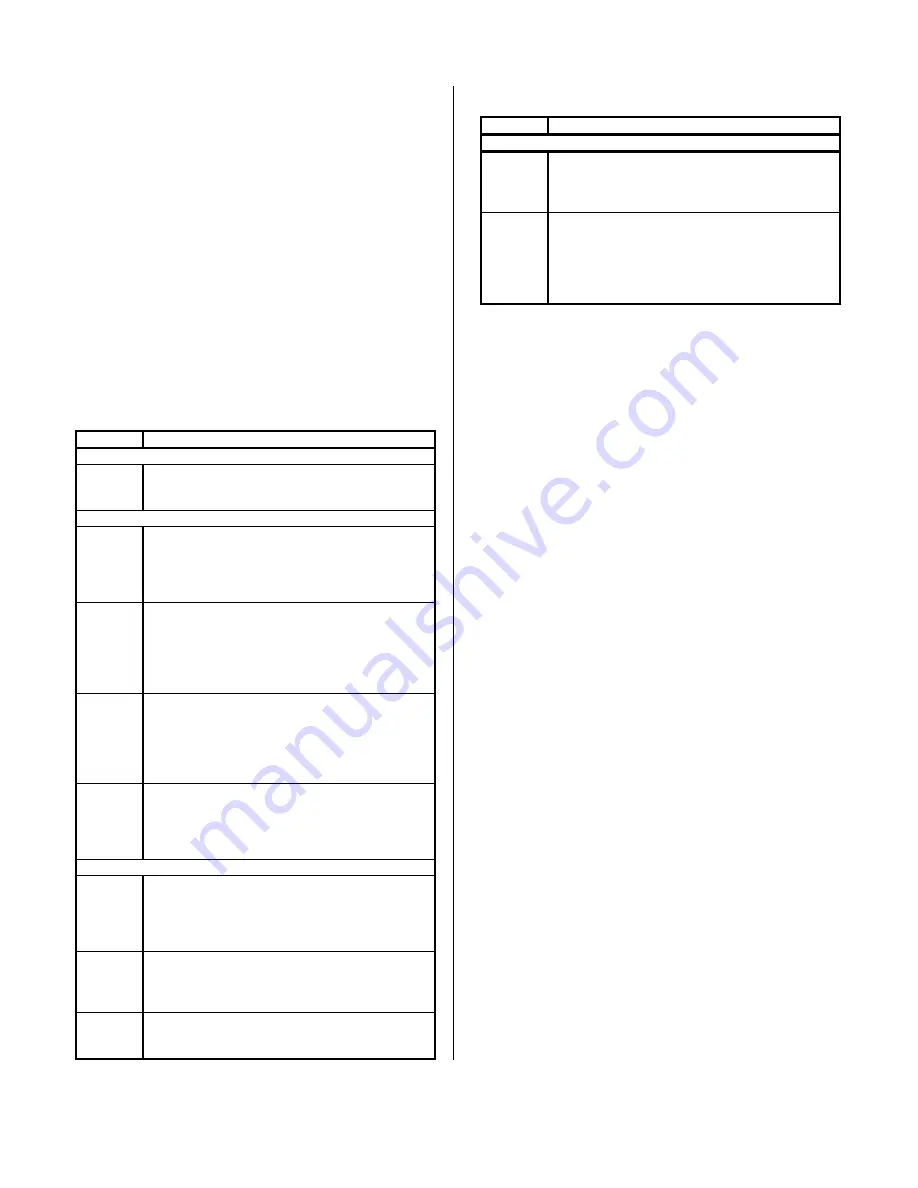
SERIES IP503 INDUSTRIAL I/O PACK EIA/TIA-232E & CENTRONICS COMMUNICATION MODULE
___________________________________________________________________________________________
- 19 -
THE CENTRONICS PARALLEL INTERFACE
This interface is a protocol for parallel data transfer first
developed by Centronics, a printer manufacturer. It has since
gained wide industry acceptance as an acceptable interface
between computers and printers
The parallel port signals can be divided into four groups:
control signals (four open-drain, TTL compatible output lines),
status signals (five TTL compatible input lines), data lines (eight
I/O lines), and ground (8 common lines)
Pins 26-50 of the field I/O connector P2 provide connectivity
to the Centronics parallel port of this module (Refer to Table 21
for pin assignments)The functions of these pins are described in
the table below. Note that the pin numbers noted in the table
refer to the pin number of the common 25-pin “D” shell connector
used for parallel ports and not the P2 pin number (see Acromag
cable Model 5029-944)For P2 numbers, add 25 to the numbers
noted (refer to Table 21)
Centronics Parallel Port Signal Description
SIGNAL
DESCRIPTION
DATA (OUTPUT/INPUT)
PD0-PD7
(Pins 2-
9)
I/O, 8-bit Parallel Data Port Lines
CONTROL (OUTPUT/INPUT)
STB*
(Pin 1)
I/O, Open Drain, Line Printer Strobe - Active low
signal to the line printer to latch the data currently
on the parallel port. The output state of this line is
controlled via Bit 0 of the LPC control register. This
line is internally pulled up via 10K
Ω
AFD*
(Pin 14)
I/O, Open Drain, Line Printer AutoFeed - This
active low signal is sent to the printer when
continuous form paper is to be autofed to the
printer. When this signal is asserted low, the paper
is automatically fed 1 line after printing. This line is
internally pulled up via 10K
Ω
INIT*
(Pin 16)
I/O, Open Drain, Line Printer Initialize - This active
low signal triggers the start of the line printer
initialization routine. When this signal is asserted
low, the printer controller is reset to its power-up
state and the print buffer is cleared. This line is
internally pulled up via 10K
Ω
SLIN*
(Pin 17)
I/O, Open Drain, Line Printer Select - this active
low line selects the printer when asserted. Its
output state is controlled via Bit 3 of the LPC
control register. This line is internally pulled up via
10K
Ω
STATUS (INPUT)
ERR*
(Pin 15)
Input, Line Printer Error - This active low signal is
held low by the printer when an error condition
occurs at the printer This signal usually indicates
the printer is in a paper-end state, off-line state, or
other error state
SLCT
(Pin 13)
Input, Line Printer Select - this active high signal is
asserted by the line printer when it is selected. The
state of this line is monitored via Bit 4 of the LPS
status register
PE
(Pin 12)
Input, Line Printer Paper Empty - This active high
signal is asserted by the printer when it runs out of
paper
Centronics Parallel Port Signal Description continued
SIGNAL
DESCRIPTION
STATUS (INPUT)
BUSY
(Pin 11)
Input, Line Printer Busy - Active high signal from
the printer that is asserted when the printer is not
ready to accept more Data. The state of this bit is
monitored via Bit 7 of the LPS status register
ACKN*
(Pin 10)
Input, Line Printer Acknowledge - Active low signal
that indicates a successful data transfer has taken
place. Optionally, ACKN* can generate a printer
port interrupt during its positive transition. The
state of this line is monitored via Bit 6 of the LPS
status register
Pins 18-25 provide ground/shielding pins
Like the RS-232 interface, the Centronics parallel interface
includes some lines that may or may not be supported by various
peripheral devices. However, the basic interface will include the
eight data lines (PD0-PD7) and three signal lines for handshaking
(Data Strobe*, Acknowledge*, and Busy)Data Strobe is an active
low signal line from the computer that indicates to the printer (or
other peripheral) that the data lines have valid information on
them. The trailing edge of Data Strobe causes the peripheral to
assert the active low ACKNowledge line. However, a busy
condition occurs when the printer is given a command to print the
line in the print buffer (carriage return), or when a vertical tab,
form feed, line feed, delete, bell, select, or deselect character is
sent. Receipt of one of these special characters causes the
printer to perform some related mechanical operation that
generally takes more than a few microseconds, causing the
handshake to change to busy condition timing and assert the
BUSY handshake line. That is, after the Data Strobe is negated,
BUSY is asserted instead of ACKNowledge, indicating that the
peripheral is busy and cannot complete the handshake for some
timeLater, after negating BUSY, the peripheral asserts
ACKNowledge for a few microseconds and busy-condition timing
ends with the negation of ACKNowledge
The Centronics interface of this module includes extended
mode support that allows the direction of data flow to be defined,
thus permitting two-way communication via the parallel
dataNormally the data lines are in the output mode, to put them
into the input mode, the port must be configured for extended
mode operation (see the LPC Register description)In extended
mode, data lines can be programmed for input or output
IP503 OPERATION
Connection to both serial ports and the parallel port is
provided through connector P2 (refer to Table 21)These serial
port pins are tied to the inputs and outputs of EIA/TIA-232E line
receivers and drivers. The function of the line receivers are to
convert the required EIA/TIA-232E signals to the TTL levels
required by the UART (Universal Asynchronous
Receiver/Transmitter)The line drivers convert the UART TTL
levels to the EIA/TIA-232E voltage levels. The UART provides
the necessary conversion from serial-to-parallel (receive) and
parallel-to-serial (transmit) for interfacing to the data bus.
Additionally, it provides data buffering and data formatting
capabilities, as well as a Centronics parallel interfAce. A
programmable logic device is used to control the interface
between the UART, the IP bus, and the serial line drivers and
receivers