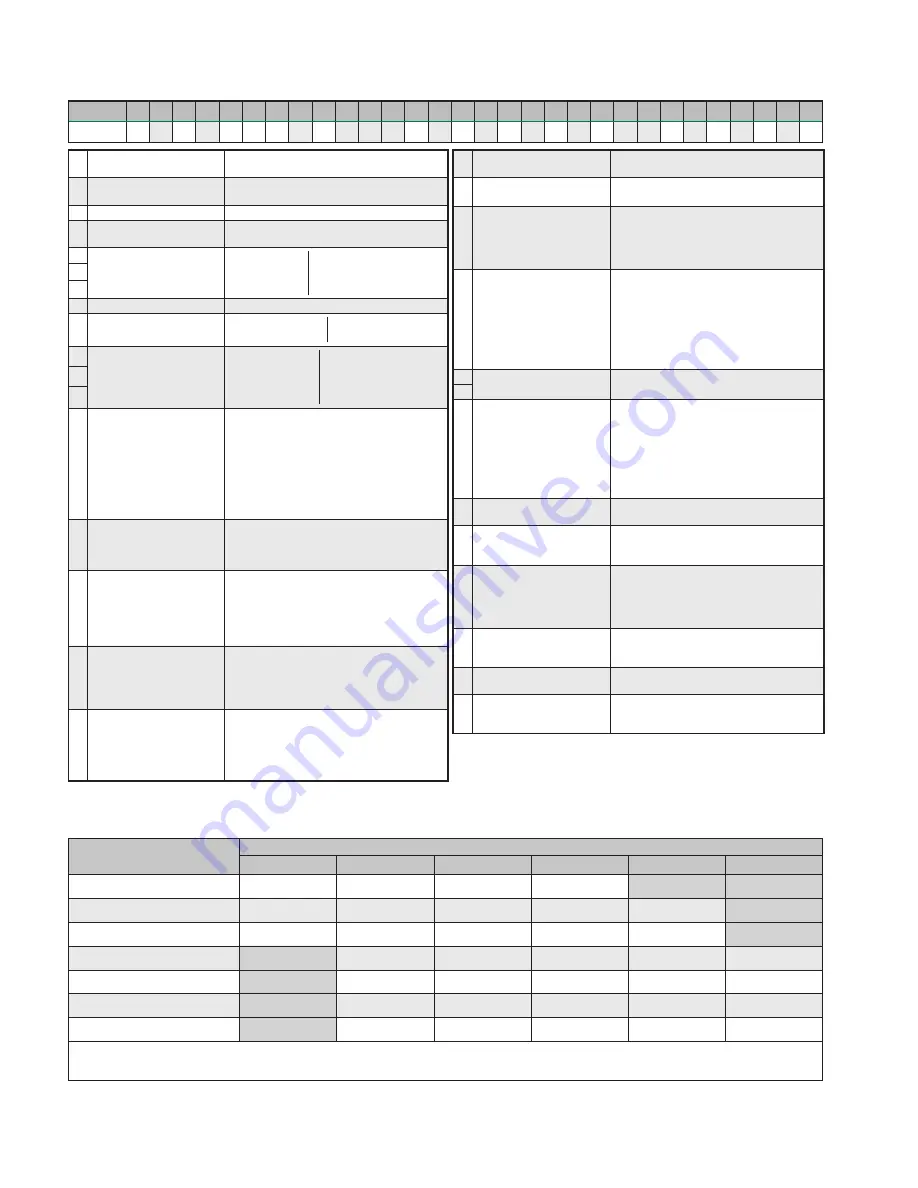
6
Eubank Wall Mount Heat Pump I&O Manual
05/2023 Rev.2
1.3 Model Identification
Example E A A 1 0 3 6 H A 0 5 0 C + + R + 1 E A + A 1 1 + + + + + +
Position
1
2
3
4
5
6
7
8
9 10 11 12 13 14 15 16 17 18 19 20 21 22 23 24 25 26 27 28 29 30
1
Unit Designation/Family
E
= Eubank Wall Mount
S
= Stock Unit
2
Energy Efficiency Ratio
(EER)
A
= 11
G
= 10
3
Refrigerant Type
A
= R-410a
4
Compressor Type/Quantity
1
= Single Fixed Speed
2
= 2-Stage Compressor
5
Unit Capacity/Nominal
Cooling (BTUH)
020
= 20,000
042
= 42,000
024
= 24,000
048
= 48,000
030
= 30,000
060
= 60,000
036
= 36,000
072
= 72,000
6
7
8
System Type
H
= Heat Pump
9
Power Supply
(Volts-Phase-Hz)
A
= 208/230-1-60
D
= 460-3-60
C
= 208/230-3-60
10
Heat Designation
@ Rated Voltage
000
= No Heat
090
= 9KW
040
= 4KW
100
= 10KW
050
= 5KW
120
= 12KW
060
= 6KW
150
= 15KW
080
= 8KW
11
12
13
Ventilation
Configuration
A
= Solid Front Door
C
= Economizer
D
= Motorized Damper w/Pressure Relief
E
= Motorized Damper w/Pressure Relief &
Independent
K
= Economizer w/Factory Inst. CO2 Control
N
= Barometric Damper w/15% OSA
+
= None
$
= Special
14
Dehumidification
R
= Electric Reheat
T
= Electric Reheat w/Humidity Control
+
= None
$
= Special
15
Controls
A
= Power Fail Alarm w/Additional Lockouts
C
= 24V EMS Relay Kit
D
= 24V EMS Relay Kit w/Factory
Installed T-Stat
+
= None
$
= Special
16
Operating Condition
N
= Hard Start
1
= Low Ambient w/FCC
R
= Crank Case Heater (CCH)
+
= None
$
= Special
17
Indoor Air Quality Features
A
= UV Light
K
= Bi-Polar Ionization
M
= Dry Bulb Sensor & CO2 Sensor
(Only w/Economizer)
+
= None
$
= Special
18
Air Flow
1
= Top Supply/Bottom Return
$
= Special
19
Compressor Location
D
= Left Hand - All 3
1
/
2
to 5 ton units
E
= Right Hand - All 1
1
/
2
to 3 ton units
20
Filter Option
A
= 2” Pleated (MERV 8, AC/HP-C)
D
= MERV 11 High Filtration Package
E
= MERV 13 High Filtration Package
+
= None
$
= Special
21
Corrosion Protection
A
= Condenser Coil Only
C
= Evaporator Coil Only
D
= Both Coils Condenser & Evaporator
F
= Coat All
G
= Coastal Package & Evaporator Coil
K
= Coastal Package
+
= None
$
= Special
22
Engineering Revision
Level
A3
B3
23
24
Cabinet Color
1
= Eubank Beige
2
= Gray
4
= White
5
= Stainless Steel Exterior
6
= Dark Bronze
7
= .050 Aluminum Stucco
A
= Stainless Steel - Unit
$
= Custom Color (Powder Coat)
25
Sound Attenuation
2
= Compressor Blanket
+
= None
26
Security Option
A
= Lockable Access Plate/Tamper Proof
+
= None
$
= Special
27
Fastener/Drain Pan Option
A
= Stainless Steel Fasteners
C
= Stainless Steel Drain Pan
D
= Stainless Steel Fasteners & Drain Pan
+
= None
$
= Special
28
Unused
C
= Copeland Compressor
+
= None
$
= Special
29
Unused
+
= None
$
= Special
30
Special Variation
+
= None
$
= Special Configuration Not Covered by
Model Nomenclature
Note: Not all options are available with all configurations.
Contact your Eubank sales representative for configuration
details and feature compatibility.
1.4 Air Flow, Weights, Filter Sizes, Refrigerant Charges and Ambient Operating Ranges
Model Number
External Static Pressure (WET COIL)
0.10
0.20
0.25
0.30
0.40
0.50
EAA1020H/1024H/2024H
889
831
820
801
EAA1030H/2030H
1152
1122
1100
1075
1028
EAA1036H/2036H
1265
1222
1200
1175
1133
EAA1042H/2042H
1650
1585
1520
1450
1360
EAA1048H/2048H
1693
1650
1619
1591
1529
EAA1060H/2060H
1693
1650
1619
1591
1529
EGA1072H
1987
1950
1865
1783
1661
Air flow ratings of 208-230v. Units are at 230v. Air flow ratings of 480 v. units are at 460 volts. Operation of units at a different voltage from the rating
point will affect air flow.
Table 1. Air Flow (Cubic Feet per Minute)