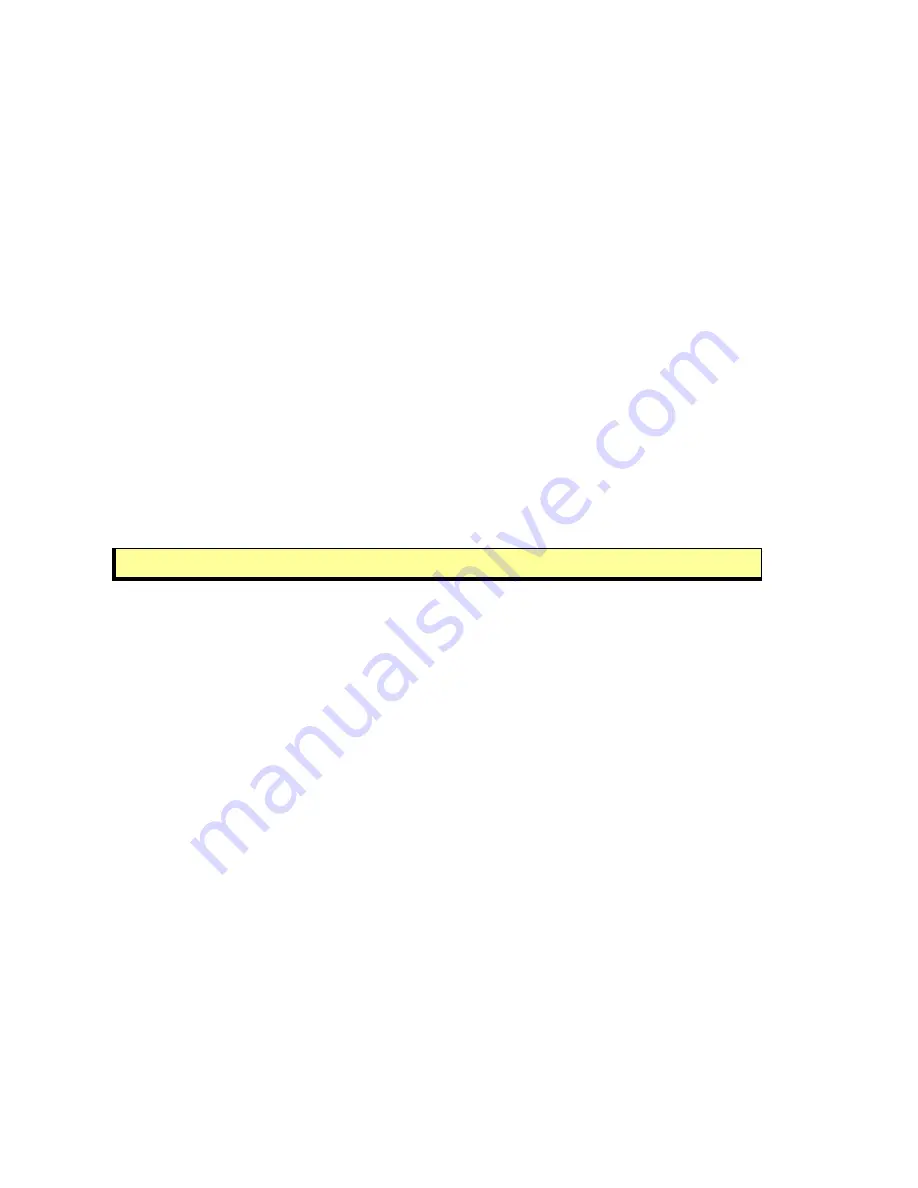
Specifications and Controls
B
ODY AND
N
OSE
Your Performance PeopleBot’s sturdy, but lightweight aluminum body houses the
batteries, drive motors, electronics, and other common components, including front and
rear sonar arrays. The body also has sufficient room, with power and signal connectors,
to support a variety of robotics accessories, including the onboard PC, radio Ethernet,
and more.
A hinged rear door gives you easy access to the batteries, which you may quickly hot-
swap to refresh any of the up to three batteries. On the rear panel, too, is the
Main
Power
switch and battery recharge port.
The nose is where we put the onboard PC. The nose is readily removable for access to
internal components: Simply remove three screws from underneath the front sonar array
and pull the nose away from the body. It’s hinged at the bottom. This provides a quick
and easy way to get to the accessory boards and disk drive of the onboard PC, as well
as to the sonar gain adjustment for the front sonar array.
B
ATTERIES AND
P
OWER
For best stability and run-times, your Performance PeopleBot should contain three
batteries which are accessible though a hinged and latched back door. They are hot-
swappable, seven ampere-hour, 12 volts direct-current (VDC) sealed lead/acid batteries
(total of 252 watt-hours). We provide a suction cup tool to help grab and slide each
battery out of its bay. Spring contacts on the robot’s battery power board alleviate the
need for manually attaching and detaching power cables or connectors.
Balance the batteries in your robot.
Battery life, of course, depends on the configuration of accessories and motor activity.
Your Performance PeopleBot runs continuously for four hours or more with onboard
computer. When hot-swapping, remove and replace one at a time.
IMPORTANT:
Batteries have a significant impact on the balance and operation of your
robot. Under most conditions, we recommend operating with three batteries.
The User Control Panel on the left strut has a bi-color LED labeled
BATTERY
that visually
indicates current battery voltage. The control panel’s buzzer also sounds a repetitive
alarm if the battery voltage drops consistently below the FLASH
LowBattery
level (see
below). If the battery voltage drops below 11 volts, the microcontroller watchdog server
automatically shuts down a client connection and notifies the onboard PC, via the
SERIAL
RI
pin, to shut down, thereby preventing data loss or systems corruption due to
low batteries.
Typical battery recharge time using the recommended accessory (800 mA) charger
varies according to the discharge state; it is roughly equal to three hours per volt per
battery. The Power Cube™ accessory allows simultaneous recharge of three
swappable batteries outside the robot.
Greatly reduce recharging time with the optional high-speed charger (4A maximum
current). It also supplies sufficient current to continuously operate the onboard
accessories, including the onboard PC and radios. But with the higher-current charger,
care must be taken to charge at least two batteries at once. A single battery may
overcharge and thereby damage both itself and the robot.
Both recommended chargers are specifically designed for optimal and safe lead-acid
battery recharging. Indicators on the module’s face show fast-charge mode (typically
an orange LED) in which the discharged batteries are given the maximal current, and
14