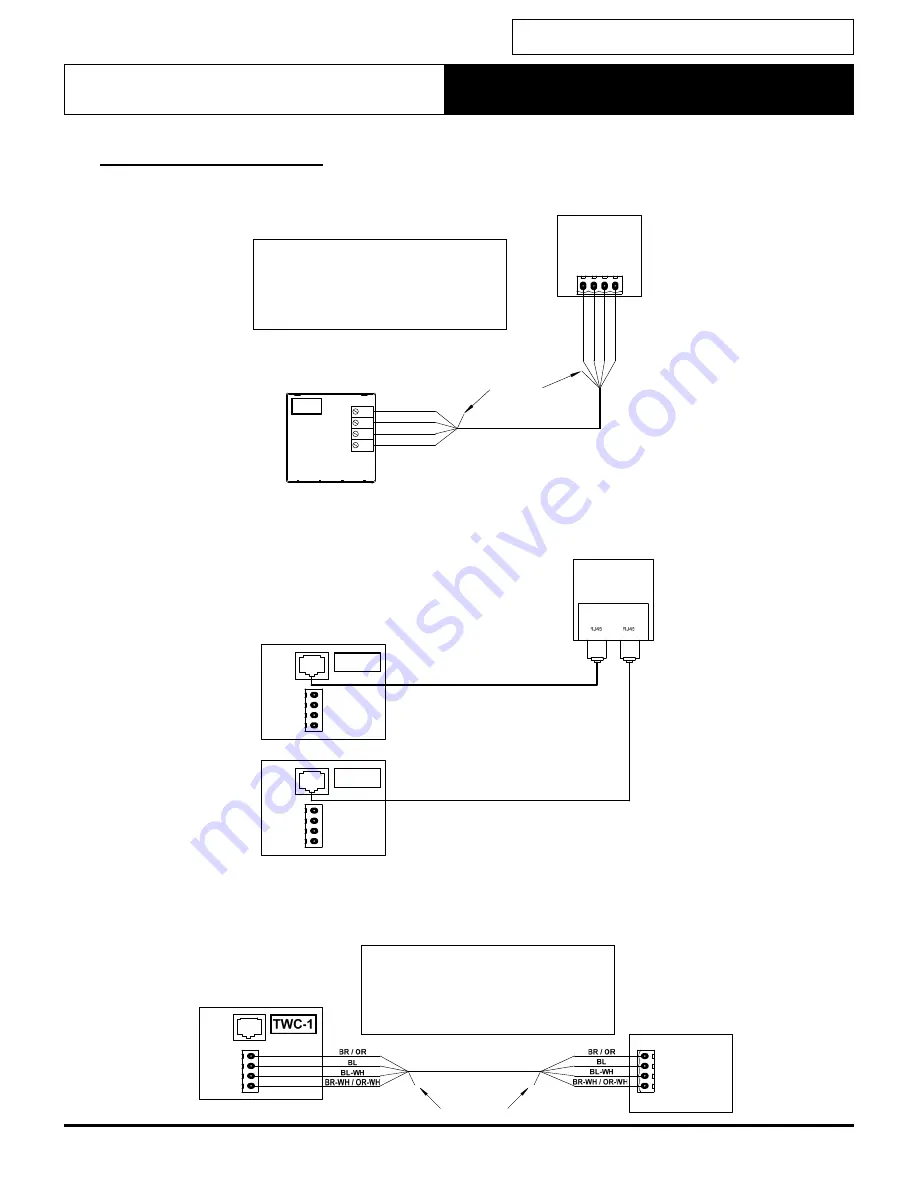
Installation and Commissioning Guide
Variable Capacity Commercial
PRELIMINARY DATA ONLY Ver. 5.01 210406
THIS LABEL TO BE REMOVED ON SIGN-OFF
25
Installation and Commissioning Guide- Package Ducted Variable Capacity Commercial
Doc. Part No. 0525-067 Ver. 5 210414
14. Wiring Connections
14.01. LC7-2 Wall Control Wiring Connections
WALL CONTROL
GND
485 B
485 A
Power
WC-1
WALL CONTROLLER
+12V A B G
CUT OFF
GR / GR-WH
BR / OR
BL
BL-WH
BR-WH / OR-WH
BR /
O
R
BL
B
L-
WH
BR-
W
H /
O
R-
W
H
INDOOR
CONTROL
BOARD
WALL CONTROL WIRING
POWER:
- BROWN / ORANGE
485 A:
- BLUE
485 B:
- BLUE-WHITE
GND:
- BROWN-WHITE / ORANGE-WHITE
NOT USED: - GREEN / GREEN-WHITE
14.02. NEO Wall Control Wiring Connections
14.02.01. NEO RJ45 Wiring
WALL CONTROL
TWC-1
+12V
A
B
G
INDOOR
CONTROL
BOARD
RJ45
WALL CONTROL
TWC-2
+12V
A
B
G
RJ45
WALL CONTROLLER
14.02.02. NEO Hard Wiring
WALL CONTROL
W
AL
L CO
NT
RO
LL
ER
+12V
A
B
G
CUT OFF
GR / GR-WH
INDOOR
CONTROL
BOARD
+12V
A
B
G
RJ45
WALL CONTROL WIRING
POWER:
- BROWN / ORANGE
485 A:
- BLUE
485 B:
- BLUE-WHITE
GND:
- BROWN-WHITE / ORANGE-WHITE
NOT USED: - GREEN / GREEN-WHITE