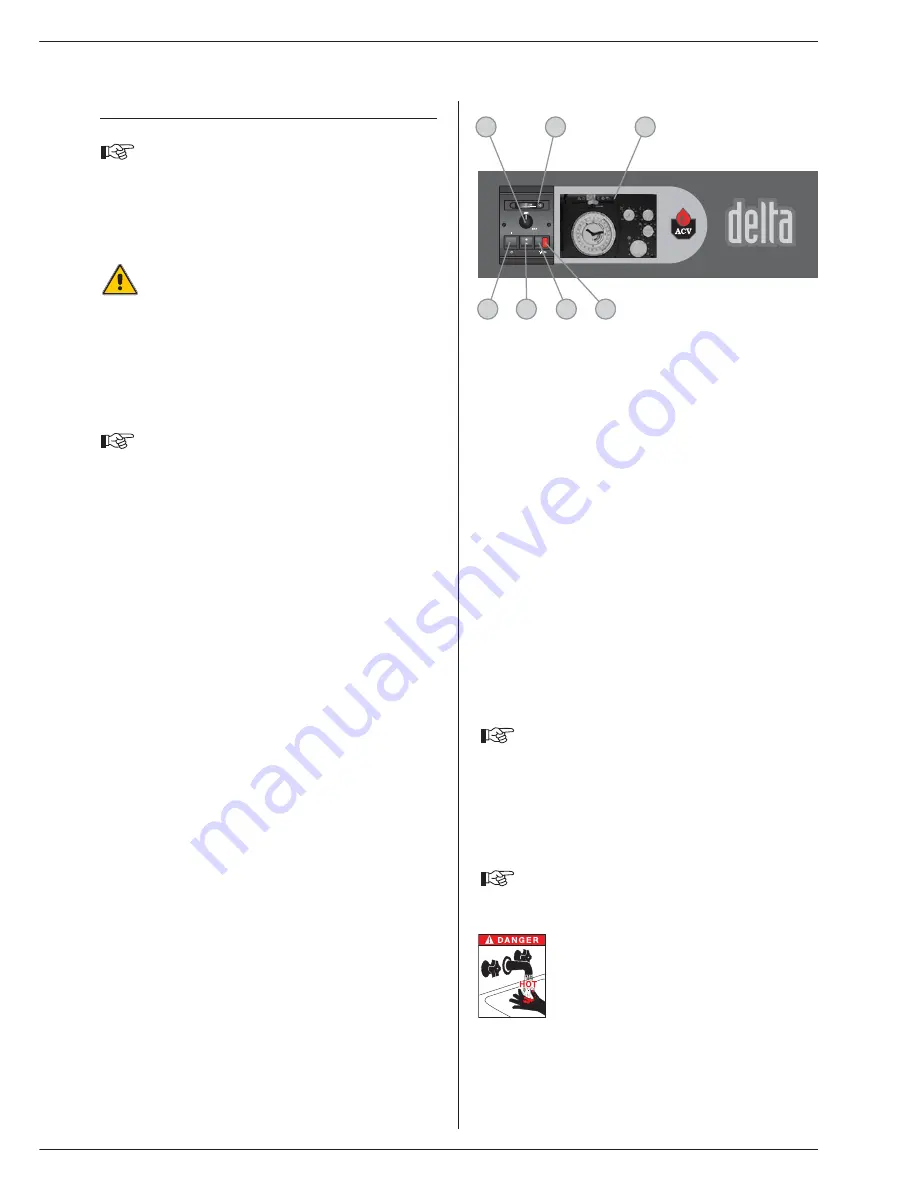
21
USE OF THE BOILER
We recommend that you have your system serviced
each year by a qualified engineer.
Starting the burner:
In normal operation the burner starts automatically if
the temperature of the boiler is below setpoint.
Before carrying out any work on the boiler, isolate it
from the electrical supply at the switch on the external
control box.
Also move the main switch on the control panel to
“OFF”.
You should familiarise yourself with the control panel
(Fig. 25)
The user must not attempt to gain access to the
components inside the control panel.
1.
Control thermostat (SV) or potentiometer (MV)
If the boiler is being used to generate hot water only, the boiler
temperature can be set to between 60 and 90°C. If the boiler is
being used for hot water and heating, then the boiler's control
thermostat or its potentiometer should normally be set to 80°C to
guarantee optimum operating conditions.
2.
Main switch
This switch is used to start and stop the boiler
3.
Summer/Winter switch
This switch is used to start and stop the heating pump (if a pump is
fitted).
4.
Thermometer
The thermometer shows the boiler temperature in the heating
circuit. This temperature should not exceed 90°C. If it does, stop the
boiler and check the settings on the thermostat (SV) or potentiometer
(MV). If the problem persists, contact your installer for advice.
5.
Resetting the burner
This switch can be used to restart the burner if it has shut down.
6.
Burner indicator lamp
This lamp tells the user whether the burner has shut down (lamp on)
or not (lamp off).
7.
Controller
(optional)
Refer to the instructions supplied with the controller if you have this
option.
Gauge pressure in the heating system
Your system must be equipped with a heating safety valve calibrated
to 3 bar and fitted with a pressure gauge.
Ensure that the system is always under water pressure. When the
system is cold and the air inside it has been vented, the gauge must
indicate a pressure between 0.5 and 1.5 bar depending on the
height of the building.
To add water:
(refer to Fig. 8 on Page 8)
• Open the filling valve (5).
• Close the valve properly after filling.
• Vent the system in order to obtain an accurate reading of the
pressure inside the heating circuit.
Safety valves
(heating circuit)
If water is found to be escaping from one of the safety valves, stop
the boiler and contact your installer for advice.
A monthly test is recommended: Lift the lever on the drain cock for
a few seconds to ensure that the safety valve is working correctly.
If there is a problem after this short test, please
contact your installer for advice.
Safety group
(hot water circuit)
A monthly test is recommended:
Lift the lever on the drain cock for a few seconds to ensure that the
safety group is working correctly.
If there is a problem after this short test, please
contact your installer for advice.
Water escaping from the safety valve or safety
group can be extremely hot and cause very
serious burns.
USER GUIDE
1
4
7
2
3
5
6
Fig. 25: Control panel
Summary of Contents for Delta
Page 9: ...28 SPARE PARTS B49 B51 B52 B50 B53 B55 B54 ...
Page 14: ......