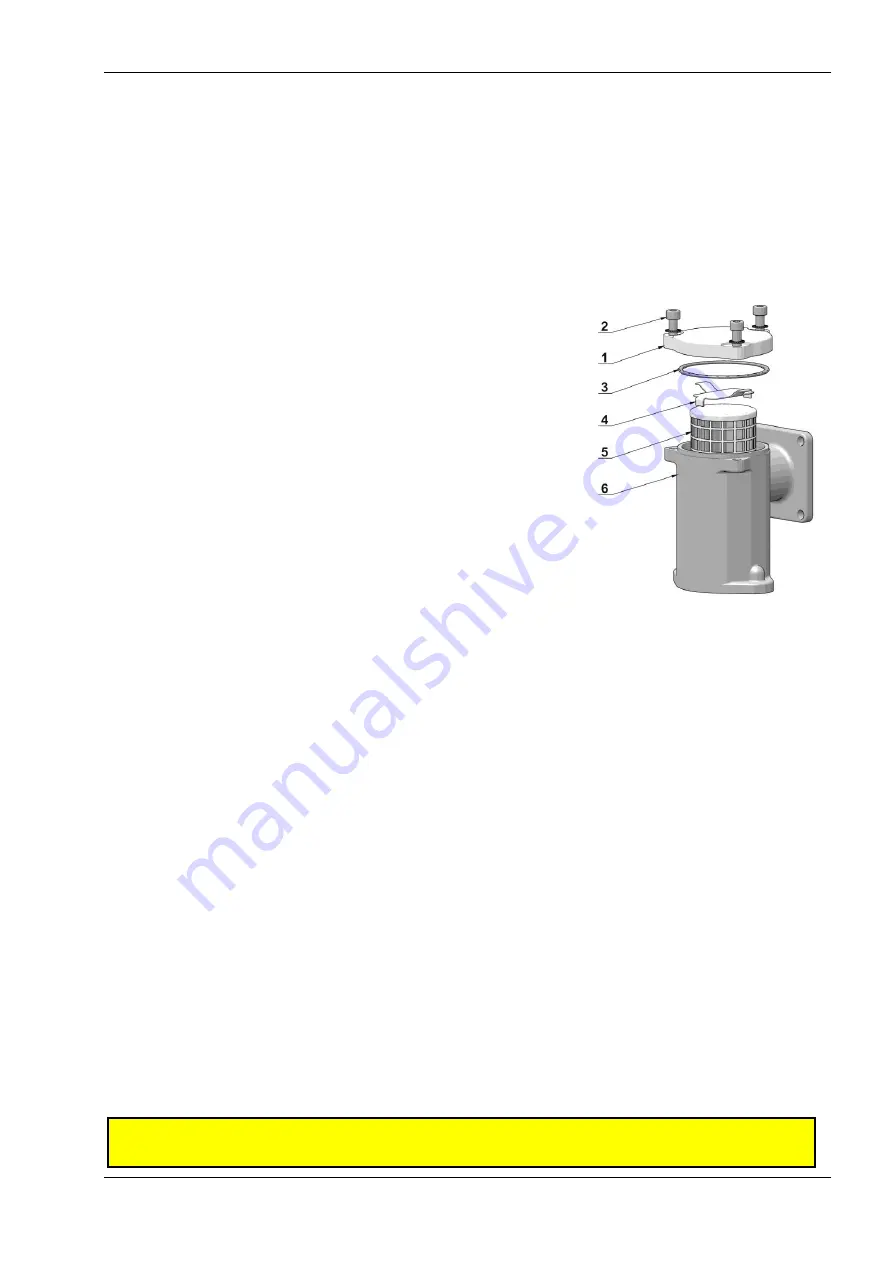
USER’S MANUAL
V-line 899x.xxx/LPG HYBRID
39
Possible defects of the monoblock:
clogged filter - exchange the filtering sleeve
faulty venting, air bubbles appear in the sight glass - it is necessary to check the condition of all
sealing parts of the monoblock and complete suction piping
leakage of the seal - possible seizing of the bearing
irregular running of the dispenser and higher noise - malfunction of vanes
Filling station operators replace the filtering sleeve. Other defects shall be serviced by a qualified repair
shop!
10.1.1.
Changing the filter element
1.
When replacing the filter insert Protect your hands from
splashes your skin the pumped liquid!
2.
Dismantle three screws (2) of the filter cover (1) and
remove the lid. After removing the pressure plate (4),
pulling it upwards to remove the filter insert (5) of the
filter body (6).
3.
Insert the new filter (5) element and perform reassembly.
4.
Check the condition of the sealing "O" ring (3) in the filter
cover. Possibly make his replacement. Damaged seal ring
can cause a malfunction (crashes liquid levels, or air leak).
5.
Chamber to close the filter cover and tighten thoroughly.
10.2.
Piston flowmeter
The meter unit consists of the proper meter with integrated
impulse detector. Only authorised specialists can handle the
metering unit because the meter is officially sealed. If the seals
are damaged, it is necessary to carry out an official inspection and new official sealing.
The condition of the meter (e.g. liquid leakage) shall be followed continuously and repairs shall be
performed in time. The stability of the set accuracy for the calibrated meter is at least one million dm
3
for measured dispensed fuel without mechanical impurities. It is recommended to check the meter
accuracy after the dispensing of such fuel quantity. Even if the seals are not damaged, the meter shall be
periodically inspected by an authorised specialist - once per two years at least.
Also the impulse detector should not be repaired - the meter is replaced only. The fixing of these
components is sealed by an official authority, when replaced they are sealed again the official authority.
10.3.
Electromagnetic two-stage valve
It is used for two-stage closing of flow when dispensing the preselected volume. The first stage partially
closes the flow to approximately 10% of the flow rate just before the set value is achieved. The second
stage closes the flow completely. The operation of the two-level stage closing of the valve shall be
followed and prospective defect shall be repaired in time.
The closing and the throttling functions are eliminated in the service mode. The repair is performed by
qualified workers. Fixing bolts of the valve shall be regularly checked and retighten to prevent any liquid
leakage.
10.4.
Sight glass of the dispenser
It is used for visual inspection of the liquid flow. Possible defects of the sight glass: leakage, broken glass
and other damages. All these defects shall be repaired by a qualified worker only.
10.5.
Dispensing hose
Special dispensing hoses certified according to EN 1360 standards are used for dispensers.
One end of the dispensing hose is threaded for screwing onto the dispensing nozzle, the adapter for
connection to dispenser is on the other end. The dispensing hoses are not repaired but replaced.
ATTENTION!
THERE IS EXPLOSION HAZARD WHEN USING A NON-CERTIFIED HOSE!!!