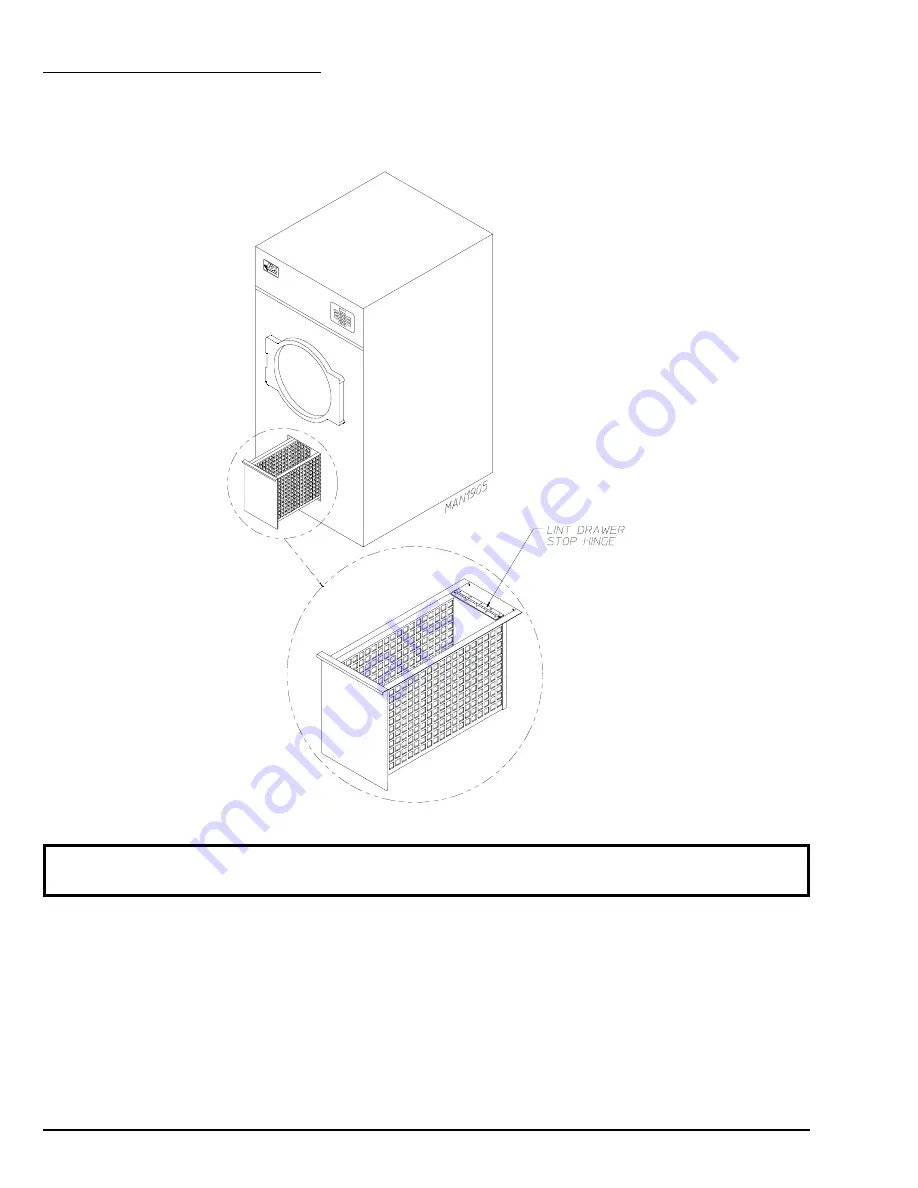
44
American Dryer Corp.
113329 - 14
D. LINT DRAWER REMOVAL
To remove the lint drawer from the dryer pull drawer out approximately halfway. Rotate/move lint drawer stop
hinge (refer to the illustration below) downward and pull the drawer out.
IMPORTANT: After replacing the lint drawer back into the dryer, be sure to rotate/move hinge back
to the upward stop position.