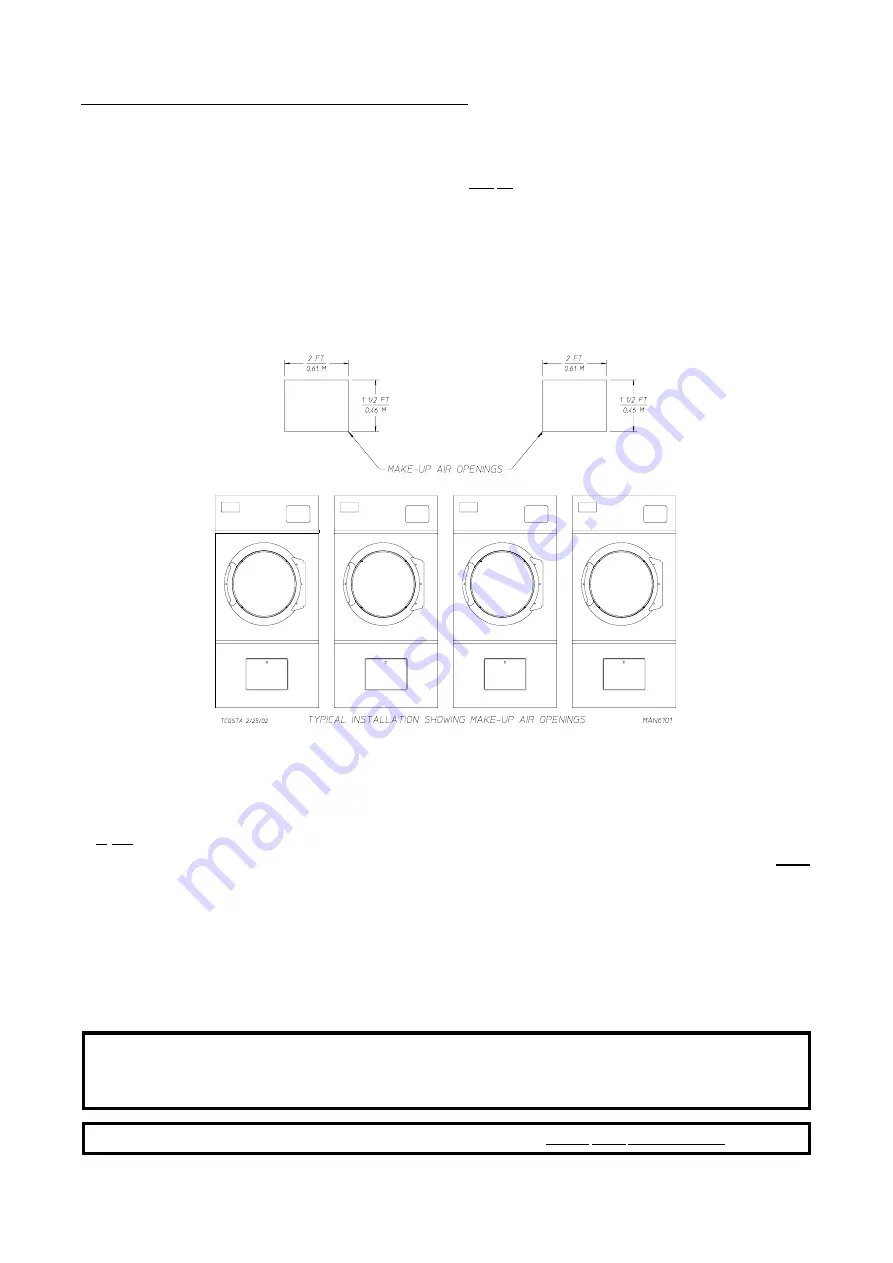
14
D. FRESH AIR SUPPLY REQUIREMENTS
When the dryer is operating, it draws in room air, heats it, passes this air through the basket (tumbler), and
exhausts it out of the building. Therefore, the room air
must be
continually replenished from the outdoors. If the
make-up air is inadequate, drying time and drying efficiency will be adversely affected. Ignition problems and sail
switch fluttering problems may result, as well as premature motor failure from overheating.
Air supply (make-up air)
must be
given careful consideration to assure proper performance of each dryer. An
unrestricted source of air is necessary for each dryer. An airflow of 1,200 cfm (cubic feet per minute) (33.98
cmm [cubic meters per minute])
must be
supplied to each dryer. As a general rule, an unrestricted air entrance
from the outdoors (atmosphere) of a minimum of 1-1/2 square feet (0.41 square meters) is required for each
dryer. The dryer
must be
installed with provisions for adequate combustion and make-up air supply.
To compensate for the use of registers or louvers used over the openings, this make-up air
must be
increased by
approximately thirty-three percent (33%). Make-up air openings
should not be
located in an area directly near
where exhaust vents exit the building.
It is not necessary to have separate make-up air openings for each dryer. Common make-up air openings are
acceptable. However, they
must be
set up in such a manner that the make-up air is distributed equally to
ALL
the dryers.
EXAMPLE:
For a bank of four (4) dryers, two (2) unrestricted openings measuring 2 feet by 1-1/2 feet (0.61
meters by 0.46 meters) (6 square feet [0.56 square meters]) are acceptable.
Allowances
must be
made for remote or constricting passageways or where dryers are located at excessive
altitudes or predominantly low pressure areas.
IMPORTANT:
Make-up air
must be
provided from a source free of dry cleaning solvent fumes.
Make-up air that is contaminated by dry cleaning solvent fumes will result in
irreparable damage to the motors and other dryer components.
NOTE:
Component failure due to dry cleaning solvent fumes will VOID THE WARRANTY.
All manuals and user guides at all-guides.com