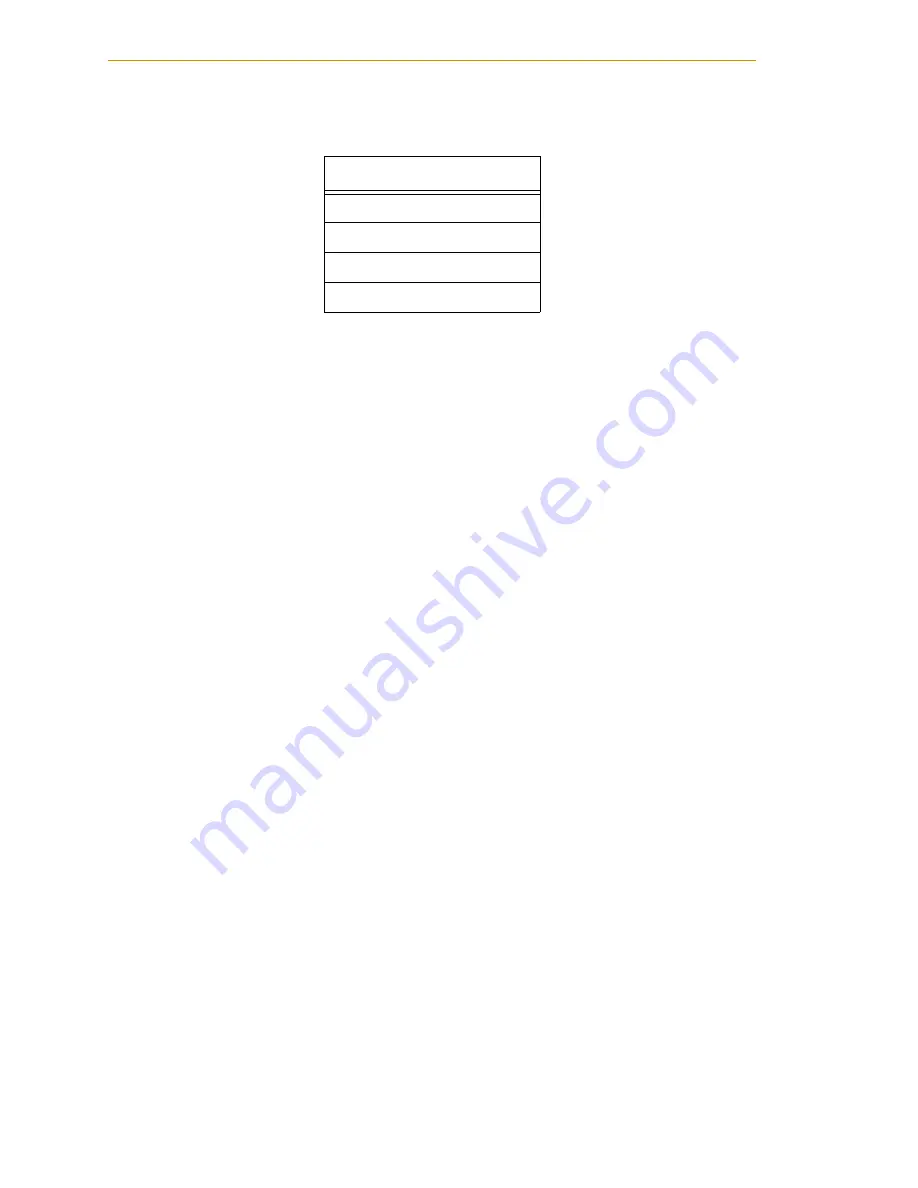
Chapter 2 - Safety
24
Adept Cobra s800 Inverted Robot User’s Guide, Rev C
Safety Barriers
Safety barriers must be an integral part of robot workcell design. Adept systems are
computer-controlled and may activate remote devices under program control at times or
along paths not anticipated by personnel. It is critical that safeguards be in place to
prevent personnel from entering the workcell whenever equipment power is present.
The robot system integrator, or end user, must ensure that adequate safeguards, safety
barriers, light curtains, safety gates, safety floor mats, etc., will be installed. The robot
workcell must be designed according to the applicable local and national standards (see
).
The safe distance to the robot depends on the height of the safety fence. The height and
the distance of the safety fence from the robot must ensure that personnel cannot reach the
danger zone of the robot.
The Adept control system has features that aid the user in constructing system
safeguards, including customer emergency stop circuitry and digital input and output
lines. The emergency power-off circuitry is capable of switching external power systems,
and can be interfaced to the appropriate user-supplied safeguards.
Impact and Trapping Points
Adept robots are capable of moving at high speeds. If a person is struck by a robot
(impacted) or trapped (pinched), death or serious injury could occur. Robot configuration,
joint speed, joint orientation, and attached payload all contribute to the total amount of
energy available to cause injury.
Instructions for Emergency Movement without Drive Power
In an emergency, when power is removed from the system, the arm can be moved
manually. The Joint 3 Brake Release button must be pressed to enable Joint 3 movement.
Emergency Recovery Procedures
In an emergency, follow your internal procedures for emergency recovery of systems.
Table 2-1. Standards Met by Robot
Standard
UL 1740
ANSI/RIA R15.06
NFPA 79
CSA/CAN Z434