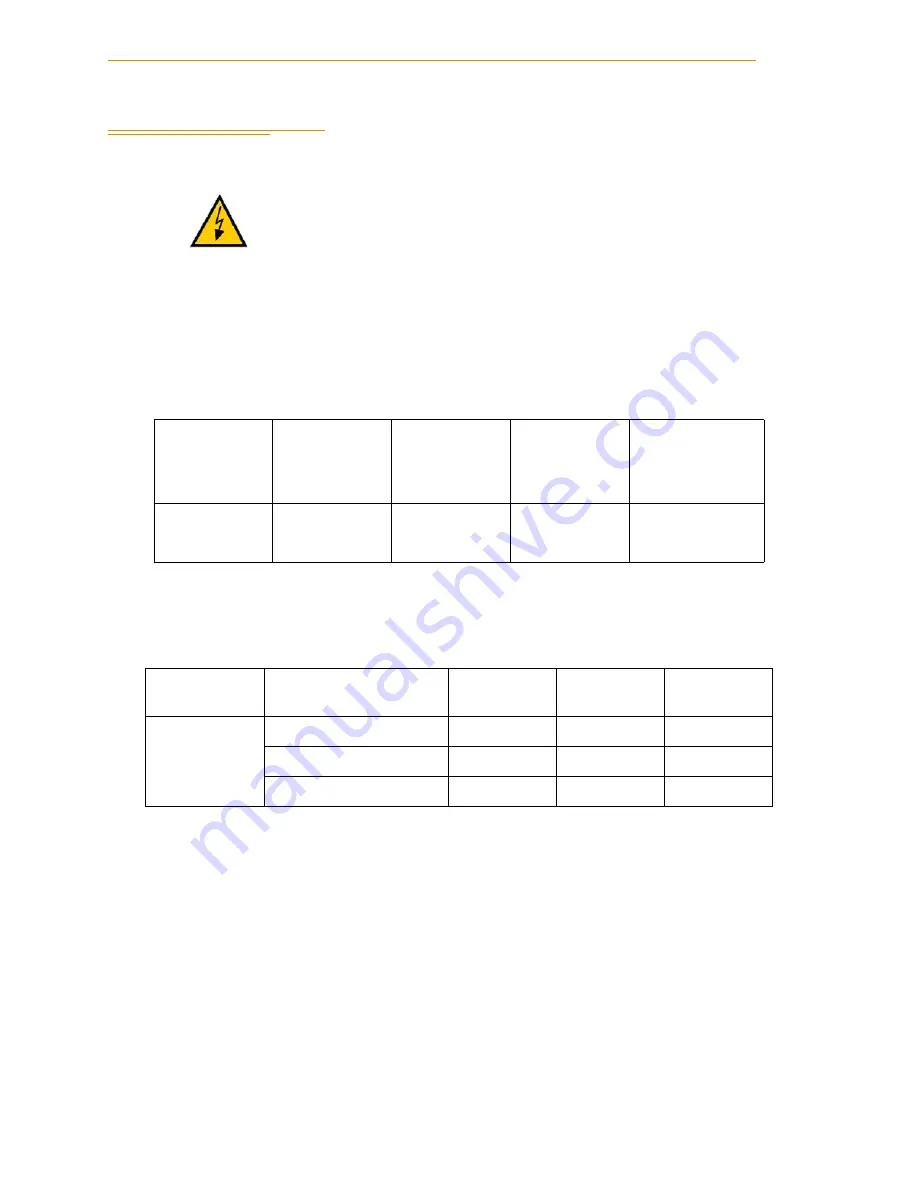
Chapter 4 - System Installation
48
Adept Cobra s800 Inverted Robot User’s Guide, Rev C
4.6
Connecting 200-240 VAC Power to Robot
Specifications for AC Power
NOTE:
The Adept robot system is intended to be installed as a piece of
equipment in a permanently-installed system.
NOTE:
Adept products are designed for connection to
symmetrically-earthed, three-phase AC mains systems (with grounded
neutral). Connections called out as single-phase can be wired
Line-to-Neutral or Line-to-Line.
WARNING:
Appropriately sized Branch Circuit Protection
and Lockout / Tagout Capability must be provided in
accordance with the National Electrical Code and any
local codes.
Ensure compliance with all local and national safety and
electrical codes for the installation and operation of the
robot system.
Table 4-5. Specifications for 200/240 VAC User-Supplied Power Supply
Auto-Ranging
Nominal
Voltage
Ranges
Minimum
Operating
Voltage
a
a
Specifications are established at nominal line voltage. Low line voltage can affect robot
performance.
Maximum
Operating
Voltage
Frequency/
Phasing
Recommended
External Circuit
Breaker,
User-Supplied
200 V to 240 V
180 V
264 V
50/60 Hz
1-phase
10 Amps
Table 4-6. Typical Robot Power Consumption
Cobra Robot
Move
Average
Power (W)
RMS
Current (A)
Peak Power
(W)
a
a
For short durations (100 ms)
s800 Inverted
No load - Adept cycle
531
2.41
1955
5.5 kg - Adept cycle
377
1.71
1406
5.5 kg - all joints move
794
3.61
2110