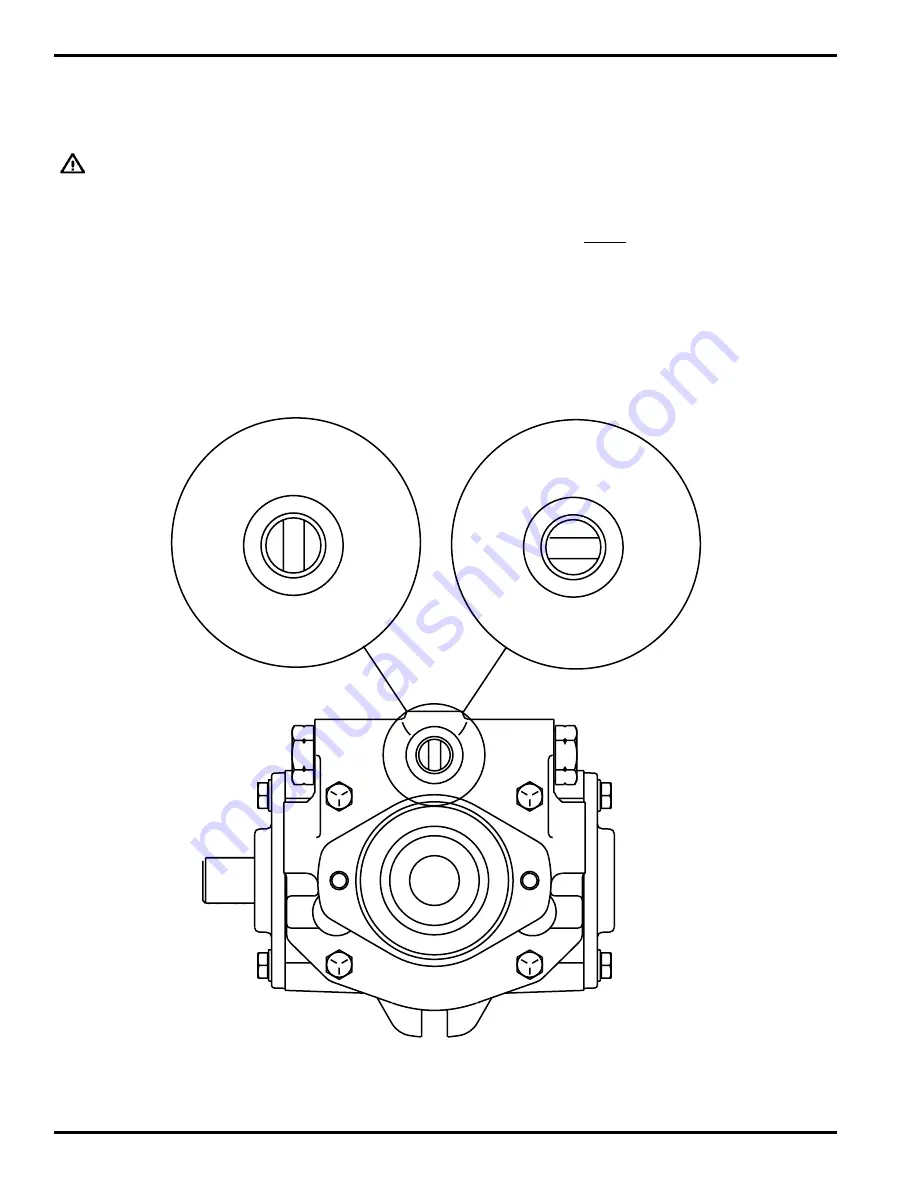
6
- FORM NO. 041410 / HYDRO-RETRIEVER 2067
____________________________________________________________________________________________________________________________________________________________________________________________________________________________________________________________________________________________
TOWING OR PUSHING A DISABLED MACHINE
CAUTION!
The machine’s drive propelling pump is manufactured with an adjustable tow valve. This valve prevents damage to the hydraulic system
when the machine is being towed/pushed short distances without use of the engine.
To access the valve open the engine compartment cover and door. Locate the valve as shown on top rear of the propelling pump. Use a pliers or
5/16” (8 mm) open end wrench to turn the valve 90 degrees, this disengages the hydrostatic lock between the motor and pump.
The hydraulic propelling pump can be damaged if the machine is towed with the valve in the normal working position
(A)
. Reference the illustrations
below for the normal working setting
(A)
(vertical) and the free wheeling towing setting
(B)
(horizontal). Note: If the tow valve is left in free wheeling
(B)
(horizontal) position the propelling pump can’t drive the machine FWD or REV. No damage will result, just re-set valve to the normal working setting
(A)
(vertical). Tow or push machine no faster than a normal walking pace (2-3 miles per hour) and for short distances only. If the machine is to be
moved long distances the rear drive wheels needs to be raised off the floor and placed on a suitable transport dolly.
GENERAL INFORMATION
A
B