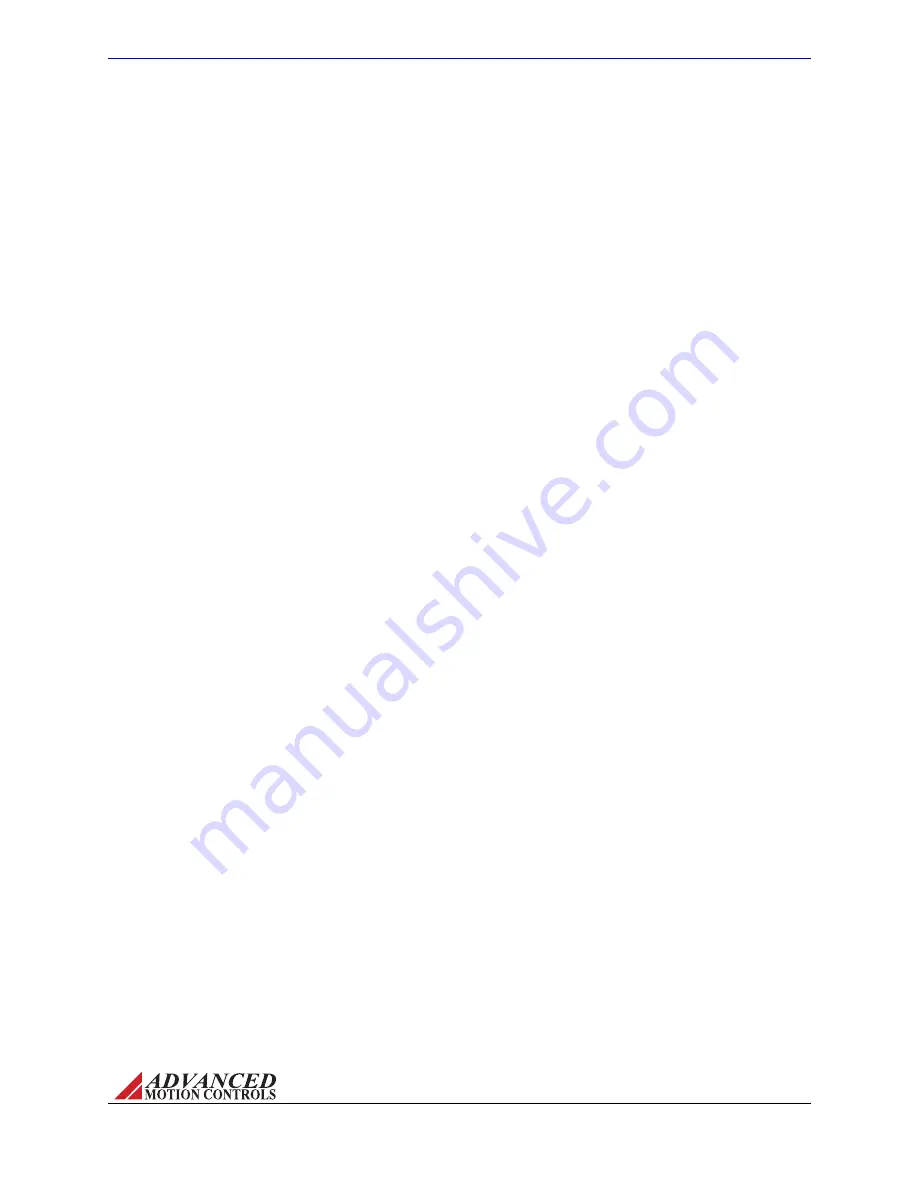
MNALAZIN-02
vii
/
Inhibit Input . . . . . . . . . . . . . . . . . . . . . . . . . . . . . . . . . . . . . . 42
Power-On Reset . . . . . . . . . . . . . . . . . . . . . . . . . . . . . . . . . . 42
Overload . . . . . . . . . . . . . . . . . . . . . . . . . . . . . . . . . . . . . . . . . . . . 42
Over-Current . . . . . . . . . . . . . . . . . . . . . . . . . . . . . . . . . . . . . . . . . 42
Motor Problems . . . . . . . . . . . . . . . . . . . . . . . . . . . . . . . . . . . . . . . 43
Causes of Erratic Operation . . . . . . . . . . . . . . . . . . . . . . . . . . . . 43
Technical Support . . . . . . . . . . . . . . . . . . . . . . . . . . . . . . . . . . . . . . . . . 44
Drive Model Information . . . . . . . . . . . . . . . . . . . . . . . . . . . . . . . 44
Product Label Description . . . . . . . . . . . . . . . . . . . . . . . . . . . . . . 44
Warranty Returns and Factory Help . . . . . . . . . . . . . . . . . . . . . . 45
Index I
Artisan Technology Group - Quality Instrumentation ... Guaranteed | (888) 88-SOURCE | www.artisantg.com