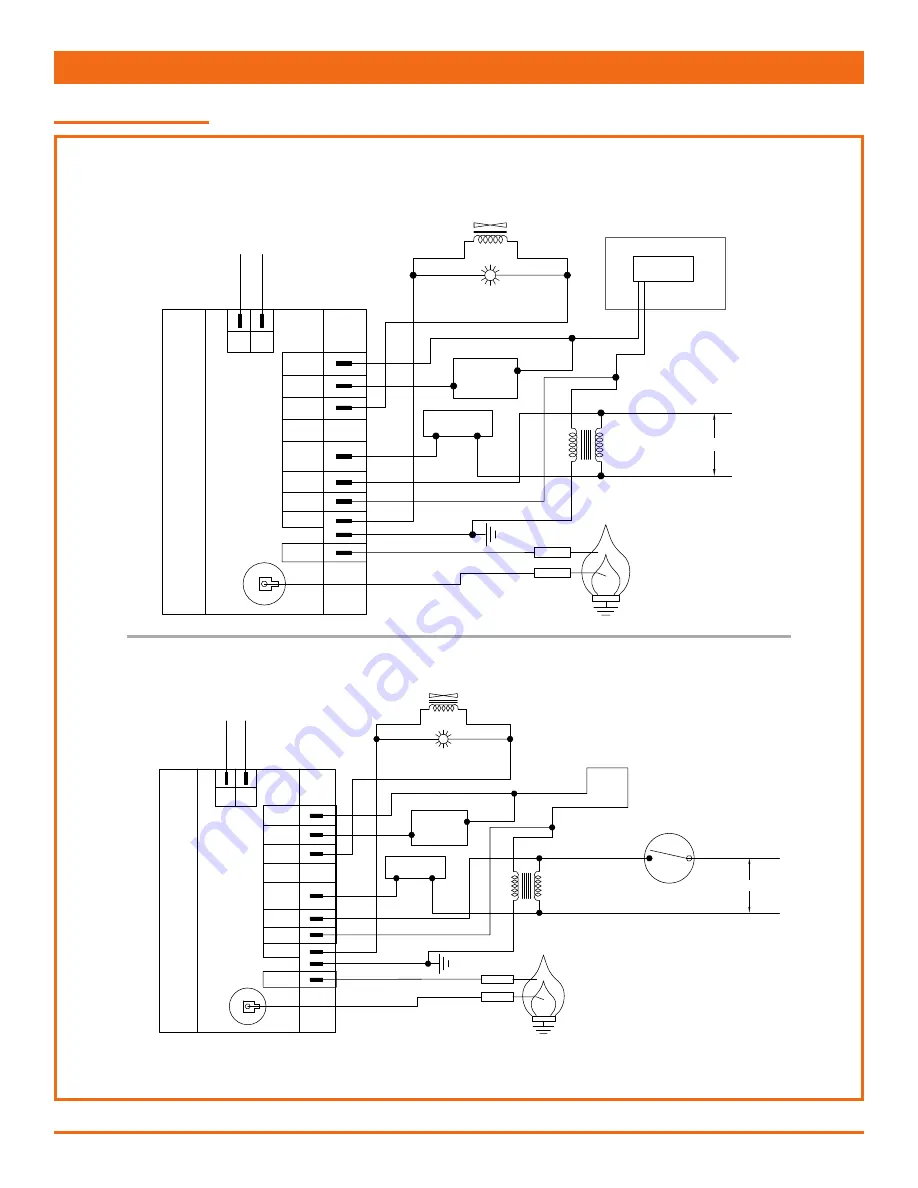
Page 28
ES/ESH-LT209_10152019
Single Stage Unitary Range
ELECTRICAL WIRING
Wiring Diagrams
Figure 30: ES Wiring Diagram Using 24VAC and 120VAC Thermostat
OPTIONAL EXTERNAL LED
CNE DSI MODULE
GAS VALVE
YELLOW
YELLOW
YELLOW
BROWN
BROWN
PURPLE
PURPLE
BLUE
RED
RED
BLACK
BLACK
BLACK
PINK
GREEN
BLUE
BLUE
RUN
LAMP
AIR
SWITCH
BLOWER
SENSOR
IGNITER
BURNER
NEUTRAL
24V
TRANSFORMER
L1
120V
TH
PSW
V1
IND
L1
24V
V2
GND
S1
HV
D-
D+
T'STAT*
WHEN CONNECTION 120 VAC STAT,
THE TWO BLUE WIRES USED FOR
THE 24VAC STAT MUST BE
CONNECTED INTERNALLY.
120V THERMOSTAT
OPTIONAL EXTERNAL LED
CNE DSI MODULE
GAS VALVE
YELLOW
YELLOW
YELLOW
BROWN
BROWN
PURPLE
PURPLE
PURPLE
RED
RED
ORANGE
BLACK
BLACK
PINK
GREEN
BLUE
BLUE
RUN
LAMP
AIR
SWITCH
BLOWER
SENSOR
IGNITER
BURNER
NEUTRAL
24V
TRANSFORMER
L1
120V
TH
PSW
V1
IND
L1
24V
V2
GND
S1
HV
D-
D+
THERMOSTAT IS
MOUNTED EXTERNALLY
BLUE & PURPLE WIRES ARE
FACTORY JUMPERED,
DISCONNECT TO WIRE IN
THERMOSTAT
24V STAT
R
W
24V THERMOSTAT
Summary of Contents for ES/ESH Series
Page 2: ......