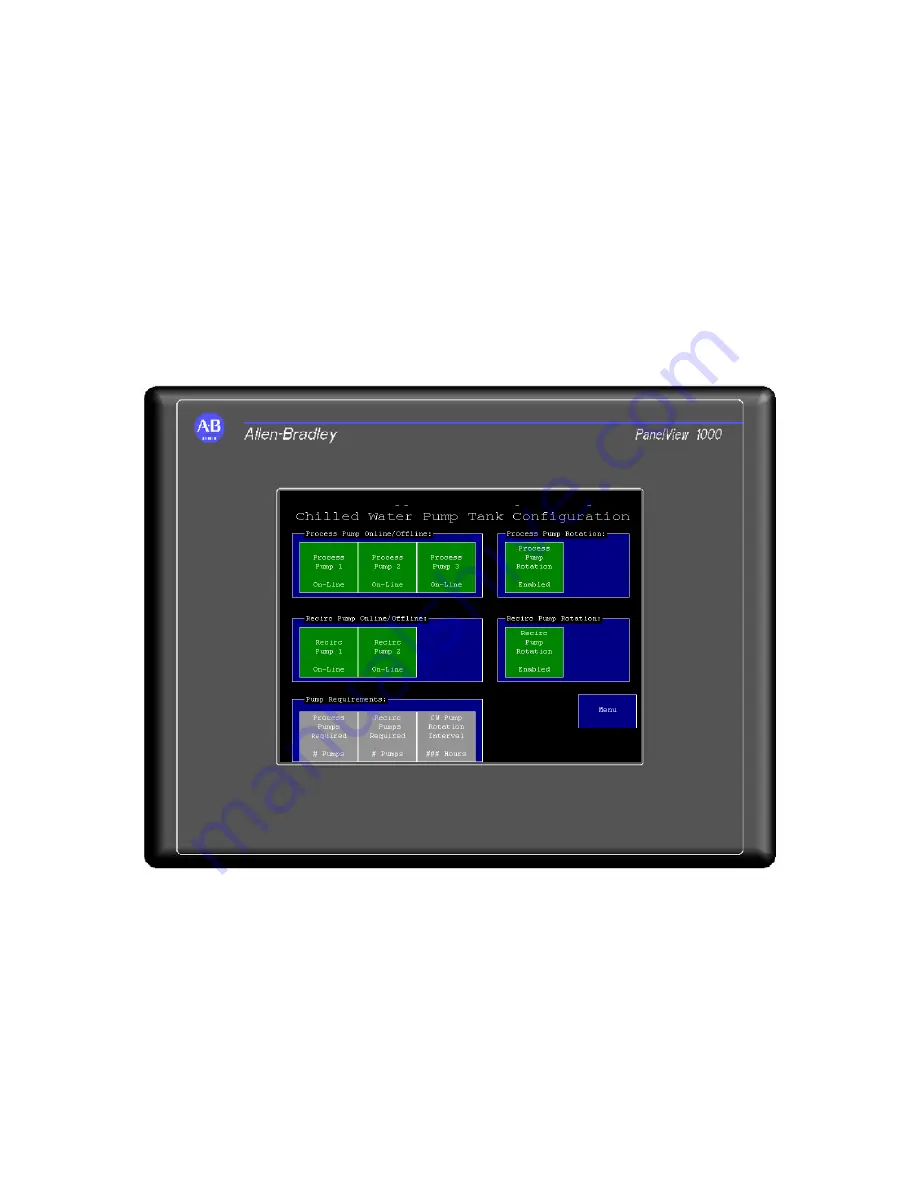
Screw Compressor Central Chiller
Chapter 4: Operation
53
Viewing Chiller Pump Status
Note:
If your chiller system was configured to operate the pump(s) of the
chilled water pump tank, the user may view the status of the process
and recirculation pumps.
To view the status of the pumps, start from the Main Menu, then:
1.
Press the Up or Down buttons to highlight “
Chilled Water Pump Tank
Configuration
”.
2.
Press
The Chilled Water Pump Tank Configuration Screen appears:
Figure 6: Chilled Water Pump Tank Configuration Screen
Only pumps that are included in the system will be shown on this screen. Pumps will display
one of the following states:
1.
OFFLINE
– This indicates that the pump has been turned off in the pump
enable/disable screen. The pump will not be called to operate until it has been re-
enabled. The color code for this indication is red.
2.
READY
– Indicates that the pump is enabled and ready to run. However, the current
number of pumps specified to run does not require this pump to operate. The color
code for this indication is yellow.