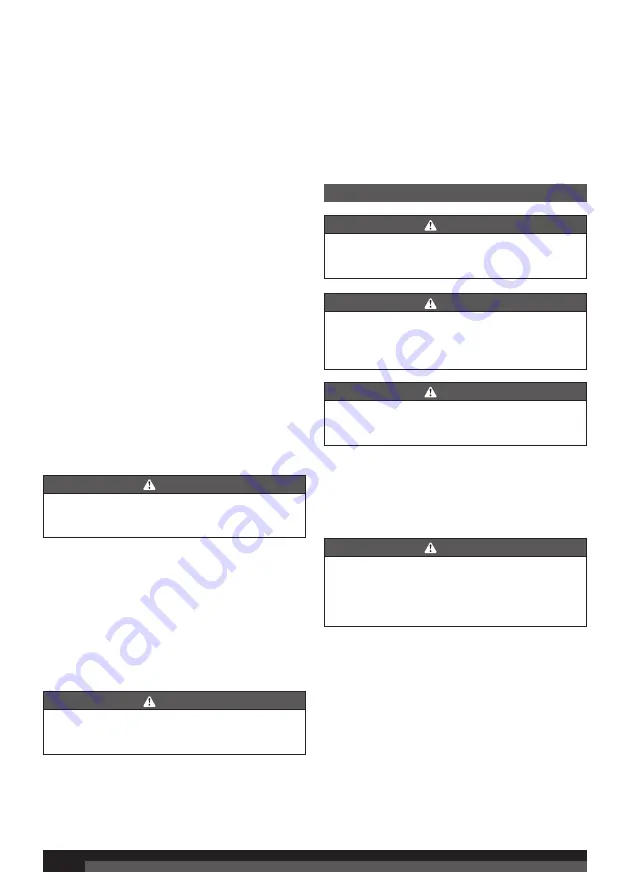
7
from you while clearing the jam.
1. Remove fasteners from the tool.
2. Pull up on the latch and open the jam release.
3. Insert a flat blade screwdriver into the driving
mechanism and push the driver mechanism back,
freeing the fastener jam.
4. Remove the bent fastener.
5. Close the jam release and latch.
6. Reconnect the tool to the air supply.
7. Reinstall fasteners.
MAINTENANCE
WARNING
When servicing use only identical replacement parts.
Use of any other parts may create a hazard or cause
product damage.
WARNING
Always wear eye protection with side shields marked
to comply with ANSI Z87.1. Failure to do so could
result in objects being thrown into your eyes resulting
in possible serious injury.
WARNING
Disconnect the tool from the air supply before
performing maintenance. Failure to do so could result
in serious personal injury.
GENERAL MAINTENANCE
Avoid using solvents when cleaning plastic parts. Most
plastics are susceptible to damage from various types of
commercial solvents and may be damaged by their use.
Use clean cloths to remove dirt, dust, oil, grease, etc.
WARNING
Do not at any time let brake fluids, gasoline, petroleum-
based products, penetrating oils, etc., come in contact
with plastic parts. Chemicals can damage, weaken or
destroy plastic which may result in serious personal
injury.
LUBRICATION
Frequent, but not excessive, lubrication is required for
best performance. Oil for pneumatic fastening tools
added through the air line connection will lubricate the
internal parts. Do not use detergent oil or additives as
these lubricants will cause accelerated wear to the
seals and bumpers in the tool, resulting in poor tool
performance and frequent tool maintenance.
COLD WEATHER OPERATION
For cold weather operation, near and below freezing,
the moisture in the air line may freeze and prevent tool
operation. We recommend the use of air tool lubricant or
permanent antifreeze (ethylene glycol) as a cold weather
lubricant.
SETTING THE AIR PRESSURE
The amount of air pressure required will depend on the
size of the nail and the workpiece material.
Begin testing the depth of drive by driving a test nail into
the same type of workpiece material used for the actual
job.
Drive a test nail with the air pressure set at 6.2 - 6.5 bar
(90 - 95 psi). Raise or lower the air pressure to find the
lowest setting that will perform the job with consistent
results.
It may be possible to achieve the desired depth with
air pressure adjustments alone. If finer adjustments are
needed, use the drive depth adjustment on the tool.
DRIVE DEPTH ADJUSTMENT
See figure 10.
The driving depth of the nail may be adjusted. It is
advisable to test the depth on a scrap workpiece to
determine the required depth for the application.
To determine depth of drive, first adjust the air pressure
and drive a test nail. To achieve the desired depth, use
the drive depth adjustment on the tool.
1. Disconnect the tool from the air supply.
2. Turn the depth selector left or right to change the
driving depth.
3. Reconnect the tool to the air supply.
4. Drive a test nail after each adjustment until the
desired depth is set.
REMOVING NAILS FROM THE TOOL
See figure 11.
1. Disconnect the tool from the air supply.
WARNING
Disconnect the tool from the air supply before
performing maintenance. Failure to do so could result
in serious personal injury.
2. To remove a strip of nails from the tool, retract the
pusher until it reaches the end of the magazine and
locks into place.
NOTE:
Always keep fingers clear of nail track of
magazine to prevent injury from unintended release
of the pusher.
3. Holding your left hand underneath the rear of the
magazine, tilt the tool up so that the hose connector
faces down. The nails will slide back and exit the rear
of the magazine.
WARNING
Disconnect the tool from the air supply before clearing
a jammed fastener. Failure to do so could result in
serious personal injury.
CLEARING A JAMMED FASTENER
See figure 12.
If a nail or fastener becomes jammed in the tool,
disconnect the air hose and keep the tool pointed away
Summary of Contents for AFNDA2565
Page 1: ...AFNDA2565 ANGLED FINISH NAILER ORIGINAL INSTRUCTIONS ...
Page 2: ...2 1 4 10 9 8 7 5 6 3 4 9 11 12 Fig 1 Fig 2 Fig 3 ...
Page 3: ...1 2 15 16 17 1 13 7 14 5 2 8 4 Fig 4 Fig 6 Fig 5 Fig 7 Fig 8 Fig 9 ...
Page 4: ...19 6 10 21 7 20 18 1 2 Fig 10 Fig 12 Fig 11 ...
Page 15: ......
Page 16: ......