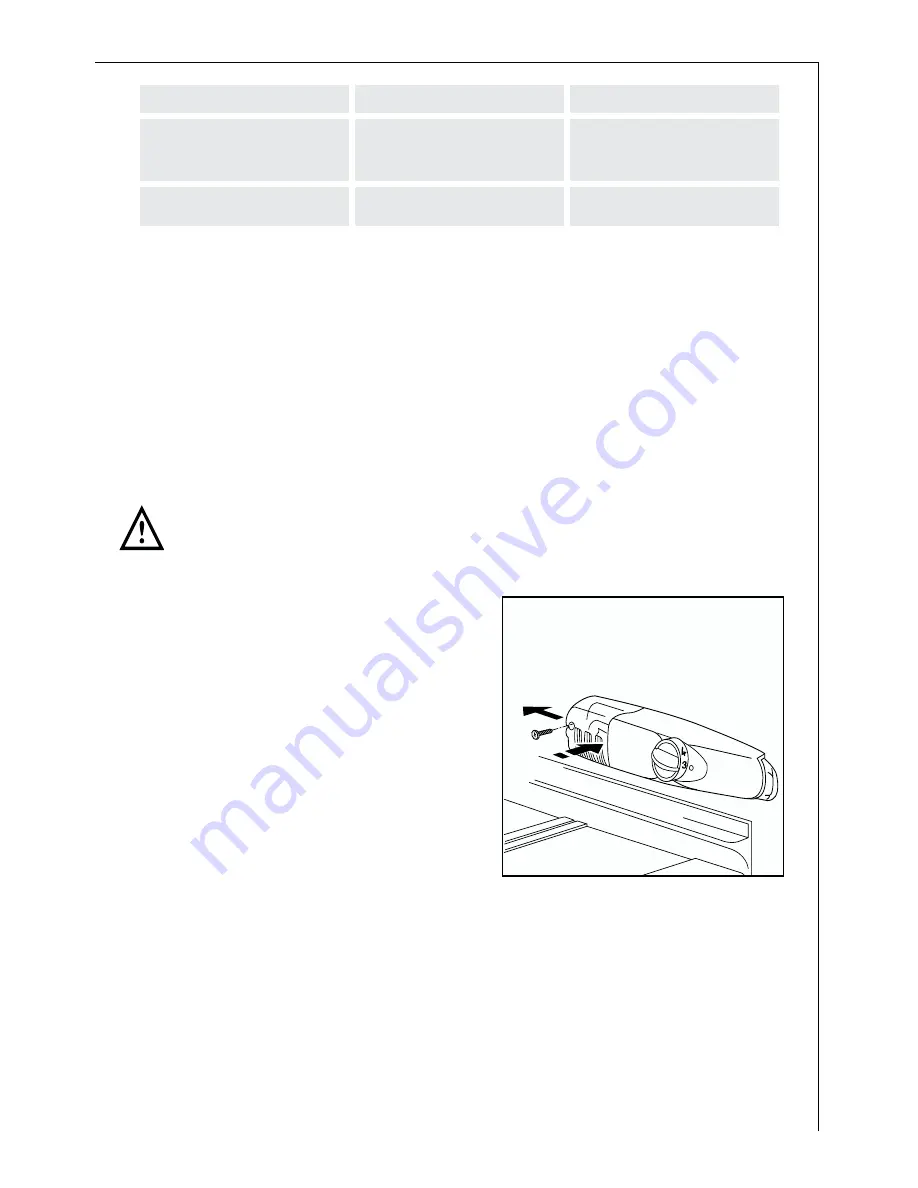
14
Heavy build up of frost, possi-
bly also on the door seal.
Door seal is not air tight (pos-
sibly after reversing the door).
Carefully warm the leaking
sections of the door seal with
a hair dryer (not hotter than
approx. 50 °C). At the same
time shape the warmed door
seal by hand until it sits cor-
rectly.
The food is too warm.
Interior lighting does not work.
The appliance is near a heat
source.
Temperature is not properly
adjusted.
Please look in the "Initial Start
Up" section.
Light bulb is defective.
Please look in the "Changing
the Light Bulb" section.
Turn the temperature control
knob to a colder setting.
Door was open for an exten-
ded period.
Please look in the "Installation
location" section.
A large quantity of warm food
was placed in the appliance
within the last 24 hours.
Open the door only as long as
necessary.
Symptom
Possible Cause
Remedy
Appliance does not work.
Appliance is not switched on
Switch on the appliance.
Mains plug is not plugged in
or is loose.
Insert mains plug.
Fuse has blown or is defective.
Check fuse, replace if neces-
sary.
Socket is defective.
Mains malfunctions are to be
corrected by an electrician.
Appliance cools too much.
Temperature is set too cold.
Turn the temperature control
knob to a warmer setting.
• Do not set temperature any colder than necessary.
• Put frozen food in the fridge to defrost. The cold in the frozen food will
then be used to cool the fridge.
Something Not Working
If the appliance is not functioning correctly, please carry out the following
checks before contacting your local AEG Service Force Centre.
Warning!
Repairs should only be carried out by qualified service engineers. Repairs
carried out by inexperienced persons may cause injury or serious malfunc-
tioning.
15
The compressor starts after a
period of time.
See the "Cleaning and Care"
section.
This is normal, no error has
occurred.
The compressor does not start
immediately after changing
the temperature setting.
Water on the floor or on sto-
rage shelves.
Water drain hole is blocked.
If, after carrying out the necessary checks there is still a fault with your
appliance please contact your local AEG Service Force Centre.
In guarantee customers should ensure that the suggested checks have
been made as the engineer will make a charge if the fault is not a
mechanical or electrical breakdown.
Please note that proof of purchase is required for any in-guarantee service
calls.
Symptom
Possible Cause
Remedy
Changing the light bulb
Warning!
There is a risk of electric shocks! Before changing the light
bulb, switch off the appliance and unplug it. Light bulb data: 220-240 V,
max. 15 W
1.
To switch off the appliance, turn the
temperature control knob to position
"0".
2.
Unplug the mains plug.
3.
To change the light bulb, remove the
screw from the light bulb cover.
4.
Unhook the light bulb cover as
shown.
5.
Change the defective light bulb.
6.
Refit the light bulb cover and the
screw.
7.
Switch the appliance back on.
AEG65