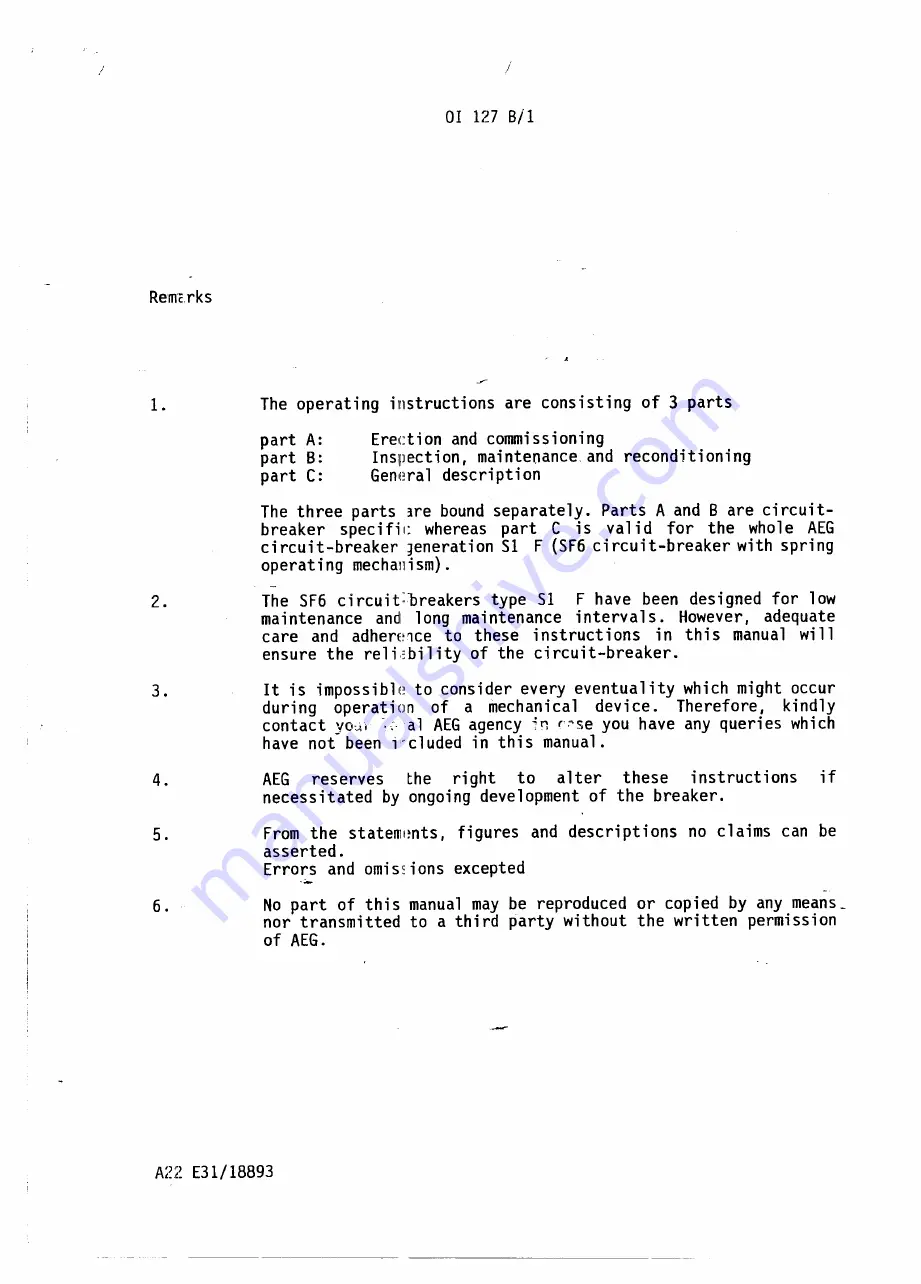
part A:
part B:
part C:
Erection and commissioning
Inspection, maintenance and reconditioning
General description
The three parts ~re bound separately. Parts A and Bare
circuit-
breaker
speci fi
I:
whereas
part
Cis
val id for the whole
AEG
circuit-breaker
~eneration Sl
F (SF6 circuit-breaker with spring
operating mechanism).
The SF6 circuit:breakers type Sl
F have been designed for low
ma intenance
and long maintenance
interv a
1
s. However,
adequate
care and adhere1ce to these instructions
in this manual will
ensure the reliability of the circuit-breaker.
It is impossibh! to consider every eventuality which might occur
during
operation
of
a mechanical
device.
Therefore,
kindly
contact
yo~)
~0
al AEG agency in r~se you have any queries which
have not been i'cluded in this manual.
AEG
reserves
the
right
to
alter
these
instructions
if
necessitated
by ongoing development of the breaker.
From the statenltmts, figures and descriptions
no claims can be
asserted.
Errors and omis~ions excepted
-.
No part of this manual may be reproduced or copied by any means_
nor transmitted
to a third party without the written permission
of AEG.
Summary of Contents for SF6
Page 21: ...Fig 83 Exploded view of tle spring operating mechanism ...
Page 31: ...SF 1377 0 SF 1377 d SF 1377 0 SF 1377 0 SF 1377 _ 0 SF 1377 d SF 1377 0 SF 1377 0 ...
Page 32: ...SF 1377 c rUlUb m m I SF 1377 c J i SF 1377 SF 137 b 0 SF 1377 SF 1377 0 b ...
Page 33: ...BeruLub FK 33 Fig B8 Points of lubrication at the interrupter unit and at thE arcing contacts ...
Page 34: ...SF 1377 bl SF 1377 bl SF 1377 II 1 _ _ _ __ L i SF 1377 bl SF 1377 cl SF 1377 bl SF 1377 bl ...
Page 35: ...1 CLtl _ l1oLykote BR2 pLus l 0 ...
Page 38: ...2 7 17 2 7 18 2 7 16 2 7 02 2 7 18 2 7 03 2 7 01 2 7 06 2 7 11 2 7 07 2 7 22 ...