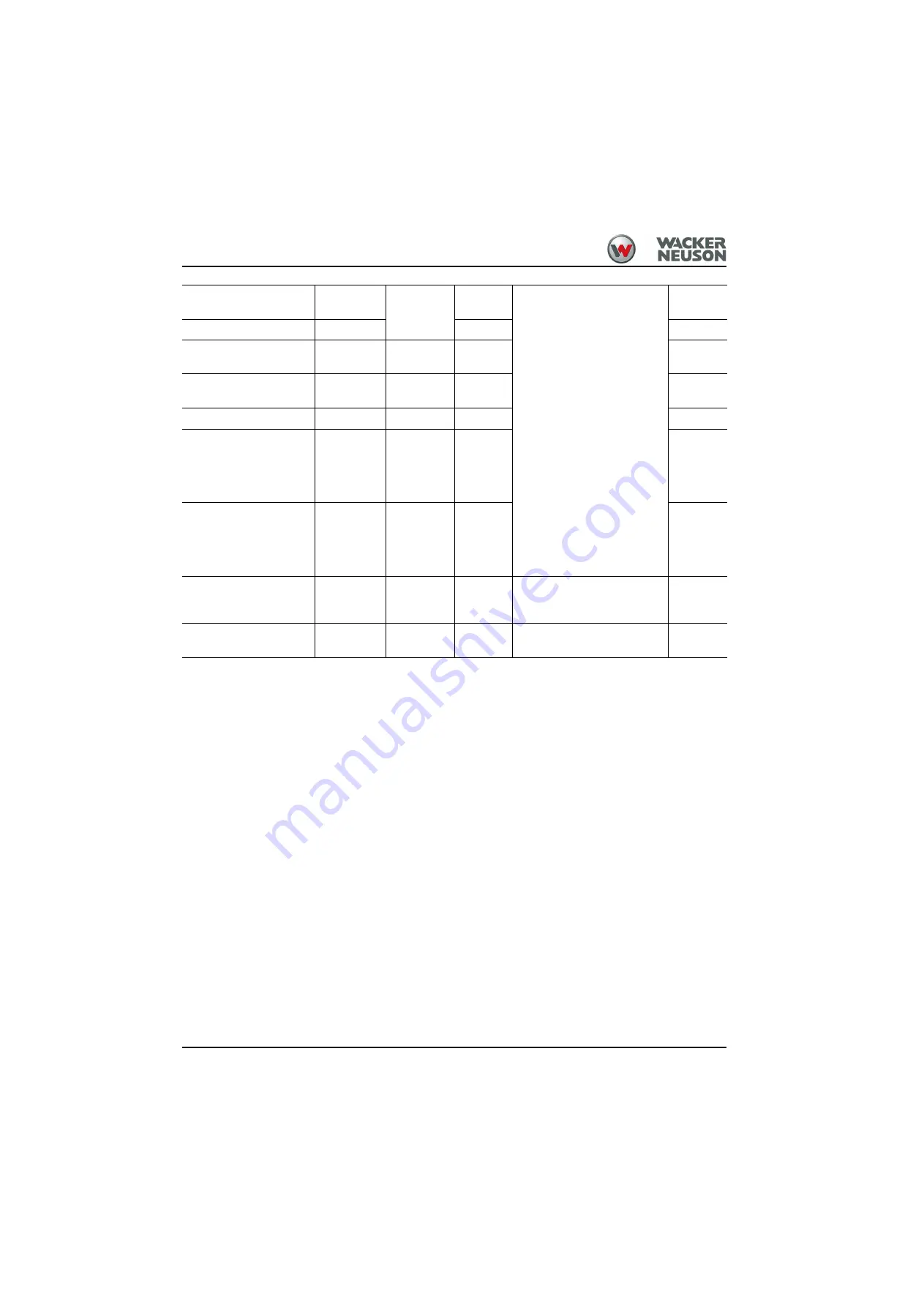
3-16
BA 418-12 * 1.0 * 418_12_3_Einleitung.fm
3 Introduction
For more information on attachments, see:
Merkblatt für Anbaugeräte (leaflet with specific instructions for attachments) §30 Abs. 10/11/12 StVZO (Federal Republic of Germany).
Merkblatt für angehängte land- oder forstwirtschaftliche Arbeitsgeräte (leaflet with specific instructions for hitching agricultural or forestry equipment onto the
machine according to German legislation).
Round and square bale
grapple
1000295315
800 – 1800
(31.5 – 70.8)
–
Picking up and transporting
silage, straw and hay bales
–
Bale grapple V40
1000375485
–
–
Bale grapple W500
1000375486
800 – 1200
(31.5 – 47.2)
–
–
Silage bucket
with grab
6,10
1000295643
2000 (78.7)
–
–
Manure forks
1000292240
1900 (74.8)
–
–
Bale spike
With 3 tines
1000373757
Fork tine
length:
1100 (39.3)
Width:
1200 (47.2)
–
–
Large bale spear
,
Folding
1000374315
Fork tine
length:
1100 (39.3)
Width:
1600 (47.2)
–
–
Silage cutting clamps
1000308359
1780 (70.0)
–
Cutting, picking up and
transporting silage, straw and
manure
–
Gate opener
6, 11
1000278984
–
–
Opening and closing specially
equipped up-and-over doors
–
1.
Pay attention to the safe load indicator during work operation and take appropriate action.
2.
Attachments are
only
permitted for the KRAMER quickhitch facility.
3.
Machine travel on public roads is only certified if a front-edge protection is installed over the entire width of the bucket.
4.
Capacity struck according to ISO 7546/capacity heaped.
5.
Use only with the load-bearing capacity diagram provided for this attachment.
6.
See the Operator’s Manual of the attachment for putting the attachment into operation and using it.
7.
Due to the line-of-sight restriction, this pallet fork may only be used with the elevated cabin.
8.
Use only with the load-bearing diagram of the pallet forks. Only for fork tines 100 x 42 mm (3.9 x 1.7 in).
9.
Use only with the load-bearing capacity diagram.
10. Cannot be used for the mechanical KRAMER quickhitch facility.
11. For safety reasons and to avoid material damage, the door opener is only permitted for opening overhead gates that are approved accordingly. Other activities
are prohibited with this attachment.
Summary of Contents for 418-12
Page 59: ...BA 418 12 1 0 418_12_3_Einleitung fm 3 27 Introduction 3 Right side of machine Fig 4 30 20 ...
Page 60: ...3 28 BA 418 12 1 0 418_12_3_Einleitung fm 3 Introduction Front of machine Fig 5 ...
Page 61: ...BA 418 12 1 0 418_12_3_Einleitung fm 3 29 Introduction 3 Rear of machine Fig 6 30 20 ...
Page 63: ...BA 418 12 1 0 418_12_3_Einleitung fm 3 31 Introduction 3 Outside right of the vehicle Fig 8 ...
Page 64: ...3 32 BA 418 12 1 0 418_12_3_Einleitung fm 3 Introduction Inside the cabin Fig 9 ...
Page 65: ...BA 418 12 1 0 418_12_3_Einleitung fm 3 33 Introduction 3 Engine compartment interior Fig 10 ...
Page 66: ...3 34 BA 418 12 1 0 418_12_3_Einleitung fm 3 Introduction Outside front of the vehicle Fig 11 ...
Page 67: ...BA 418 12 1 0 418_12_3_Einleitung fm 3 35 Introduction 3 Outside rear of the vehicle Fig 12 ...
Page 326: ...5 170 BA 418 12 1 0 418_12_5_Bedienung fm 5 Operation ...
Page 338: ...6 12 BA 418 12 1 0 418_12_6_Transport fm 6 Transport ...
Page 426: ...7 88 BA 418 12 1 0 418_12_7_Wartung fm 7 Maintenance ...
Page 462: ...8 36 BA 418 12 1 0 418_12_8_Betriebsstoerung fm 8 Malfunctions Notes ...
Page 499: ...BA 418 12 1 0 BA_418_12_V1_usSIX fm S 7 Index ...
Page 500: ...S 8 BA 418 12 1 0 BA_418_12_V1_usSIX fm Index ...
Page 527: ...FORM RTF 0907 Printed in U S A ...