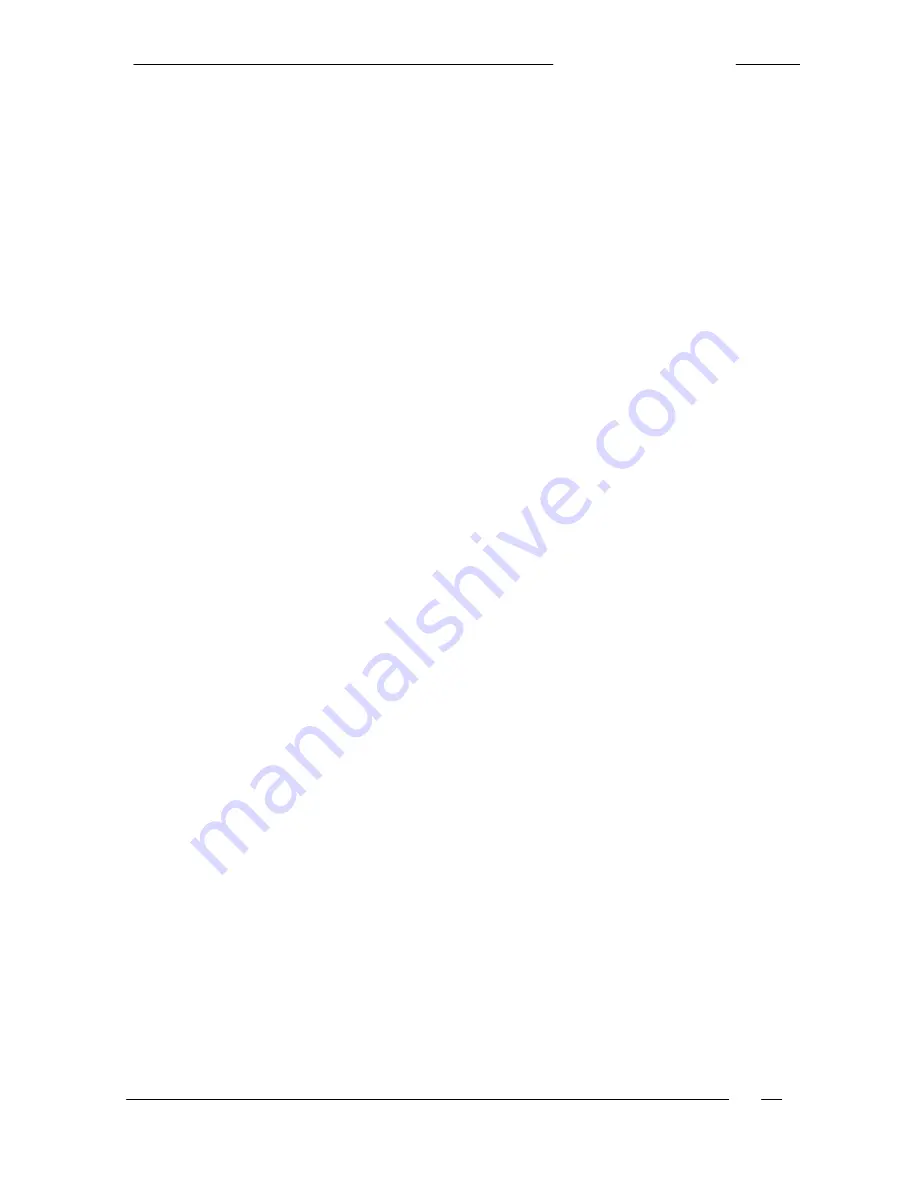
Grumman F7 F-3 Tigercat
Building instructions - Grumman F7 F-3 Tigercat
4
the wing and drill holes at the marked points, initially using a 3 mm Ø drill. Be sure to drill parallel to the
underside of the wing. Open up the holes to 5 mm Ø. Cut two pieces of beech dowel (26) about 30 - 35
mm long and check that they fit in the holes in the fuselage. File out the holes if necessary, then press the
dowels into the wing. Check that the wing seats correctly on the fuselage, and correct the position of the
dowels if necessary. When everything fits correctly, glue the dowels in the wing using laminating resin.
Trim part (36) to match the wing dihedral and glue it in place with laminating resin as shown on the plan.
Add the plywood plate (51) as shown. Section E-E shows how the bridge piece assembly is installed in
the fuselage recess. Apply plenty of thickened laminating resin to bond the parts in place securely.
Glue the 3 mm ply reinforcement in the GRP fuselage fairing (3) as shown on the plan; it supports the
scale antenna (63), and must be drilled 5 mm Ø to accept the M5 screw (31). Temporarily fix the wing to
the fuselage and trim the edges of the fairing (3) to follow the wing section accurately. You will also need
to saw off the bottom of the front face of the fairing (3) horizontally; a diamond cut-off disc makes this job
easy. When the fairing (3) is an accurate fit on the wing, mark the position of the hole in the bridge piece
(51) using a 5 mm Ø drill bit held at right-angles to the underside of the wing. Remove the fairing, and
check that the marked point is exactly central! Drill through the wing and the bridge piece (50 + 37) using
a 4 mm Ø drill. Open up the hole in the wing to 5 mm Ø, cut a thread in the bridge piece using an M5 tap,
and run a few drops of thin cyano into the threaded hole to harden the wood. Run the tap through the hole
again once the glue has set hard.
The aluminium sleeve (30) serves as a spacer for the wing retainer screw (31); this means that it must
transmit the pressure of the screw head to the wing. Here is our suggestion: open up the 5 mm Ø hole in
the fairing to about 8.2 mm Ø, so that the aluminium tube is an easy sliding fit. Fit the screw (31) through
the wing from the underside and fit the aluminium sleeve (30) on the screw shank. Now fit the fairing (3)
over it, leaving the sleeve (30) projecting slightly. Mark the correct length of the sleeve (30), cut it to length
and check that it now ends flush. When you are satisfied, bevel one end of the tube using a countersink
bit, so that the countersunk screw head bears on the full thickness of the sleeve.
Before installing part (30) permanently, de-grease the metal and roughen the surface carefully: place the
tube on a hard surface, lay a sharp file on it, and roll it to and fro under light pressure.
The first step is to glue the aluminium sleeve (30) to the wing using thickened resin. Fit the screw (31)
through the hole in the wing from the underside, slip the sleeve (30) on the screw shank and apply a
generous fillet of resin all round the joint. Cut small plywood plates and glue them to the inside face of part
(3) at the same time - see fuselage side elevation and section B-B.
While the resin is still soft place the wing on the fuselage, apply thickened resin to the top end of the
sleeve (30) and place the fairing (3) over it. The screw (31) acts as a guide to thread the sleeve through
the fairing. Place the fairing (3) on the wing and align it carefully with the fuselage, then tighten the screw
(31) lightly. Apply a little cyano round the periphery of the fairing to fix it to the wing, then apply laminating
resin all along the joint to form a permanent bond. Allow the glue to set hard, then tighten the retaining
screw firmly prior to trimming the canopy (9) to fit. The canopy must fit neatly on the fuselage and also on
the fairing (3).
Cut out the canopy (9) slightly oversize - it should project by about 1.5 mm at the front - and trim it back
gradually to obtain a close fit. A balsa plane set fine (please - use a new blade!) will quickly and
accurately trim the edges of the plastic. The job can be finished using a sharp file laid at an angle on the
edge of the moulding. Remove the wing once the canopy is a perfect fit.
Tape the canopy on the fuselage, and cut out the cockpit moulding (7). Chamfer the bottom edges until it
fits neatly inside the canopy (9) - see also section B-B and the fuselage side elevation. Cut a strip of 3 mm
plywood about 10 - 12 mm wide, and glue it to the rear face of the cockpit moulding. Glue strips of
plywood to the sides of the cockpit in the same way. These must be slightly overlength, as they are
intended to rest on the front face of the fairing (3) - see section B-B and the fuselage side elevation. Trim
the pilot’s seat (8) to fit and glue it in the cockpit. Drill 3 mm Ø holes in the crosswise ply strips to accept
the dowels (57), and glue them in place - see section B-B and the fuselage side elevation. With the wing
securely fixed to the fuselage, mark the position of the dowels on the front face of part (3) (without the
canopy!), then drill the holes using a 2.5 mm Ø bit. These holes should now be opened up gradually using
a round file until the dowels are a snug fit in them. Check that everything fits properly when the canopy is
in position.
Paint the cockpit using plastic kit enamels, e.g. Humbrol or Revell, after masking out the fuselage with
narrow tape where glue will be applied later. Place the cockpit in position, apply adhesive to the sides of
the cockpit moulding, and carefully place the canopy in position. Tape it to the fuselage and leave the
adhesive to harden fully.
Trim the half-former (53) to fit in the fuselage, and glue it in place with thickened laminating resin. Cut a
slot in the fuselage for the actuating lever of the canopy latch (20), and shorten the lever as shown. Drill a
4 mm Ø hole in the half-former (53) to clear the latch pin (20) - see fuselage side elevation. Open up the
hole to about 5 mm Ø using a round file, and tack the latch (20) in place with a little cyano (don’t glue it