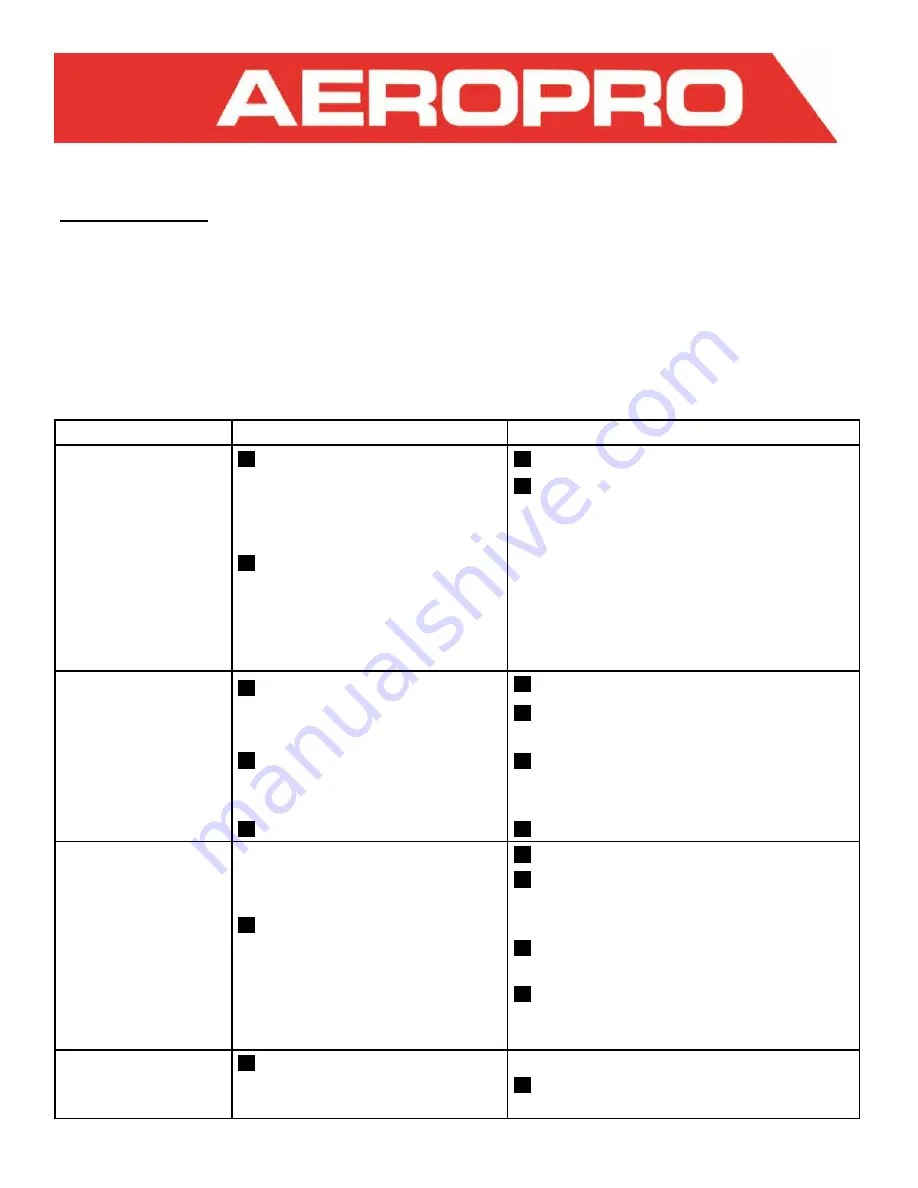
Operating Instructions
Problems
Possible Causes
Remedies
If tool runs at normal
speed, but loses
speed under load
Motor parts worn
Lubricate clutch housing.
Cam clutch worn or sticking
due to lack of lubricant
Check for excess clutch oil. Clutch
cases need only be half full. Overfilling
can cause drag on high speed clutch
parts, i.e. a typical oiled/lubricated air
tool requires 1⁄2 ounce of oil
GREASE LUBRICATED:
Heat usually
indicates insufficient grease in cham-
ber. Severe operating conditions may
require more frequent lubrication
If tool runs slowly
and air flows lightly
from exhaust
Motor parts jammed with dirt
particles
Check air inlet filter for blockage
Pour air tool lubricating oil into air inlet
as per instructions
Power regulator in closed
position
Operate tool in short bursts quickly
reversing rotation back and forth
where applicable
Air flow blocked by dirt
Repeat above if needed
If tool will not run
and air flows freely
from exhaust
One or more motor vanes
stuck due to material build
up
Pour lubrication oil into the tool air inlet
Operate tool in short bursts of forward
and/or reverse rotation where
applicable
Tap motor housing gently with plastic
mallet
Disconnect supply. Free motor by
rotating drive shank manually where
applicable
If tool will not shut
off
O-rings throttle valve
dislodged from seat inlet
valve
Replace O-ring
Trouble Shooting
The following table details the common operating system with problem and solutions. Please read
the table carefully and follow it.
WARNING:
If any of the following symptoms appear during your operating, stop using the tool
immediately, or serious personal injury could result. Only qualified persons or an authorised service
centre can perform repairs or replacement of tool.
Disconnect tool from air supply before attempting repair or adjustment. When replacing O-rings or
cylinder, lubricate with air tool oil before assembly.