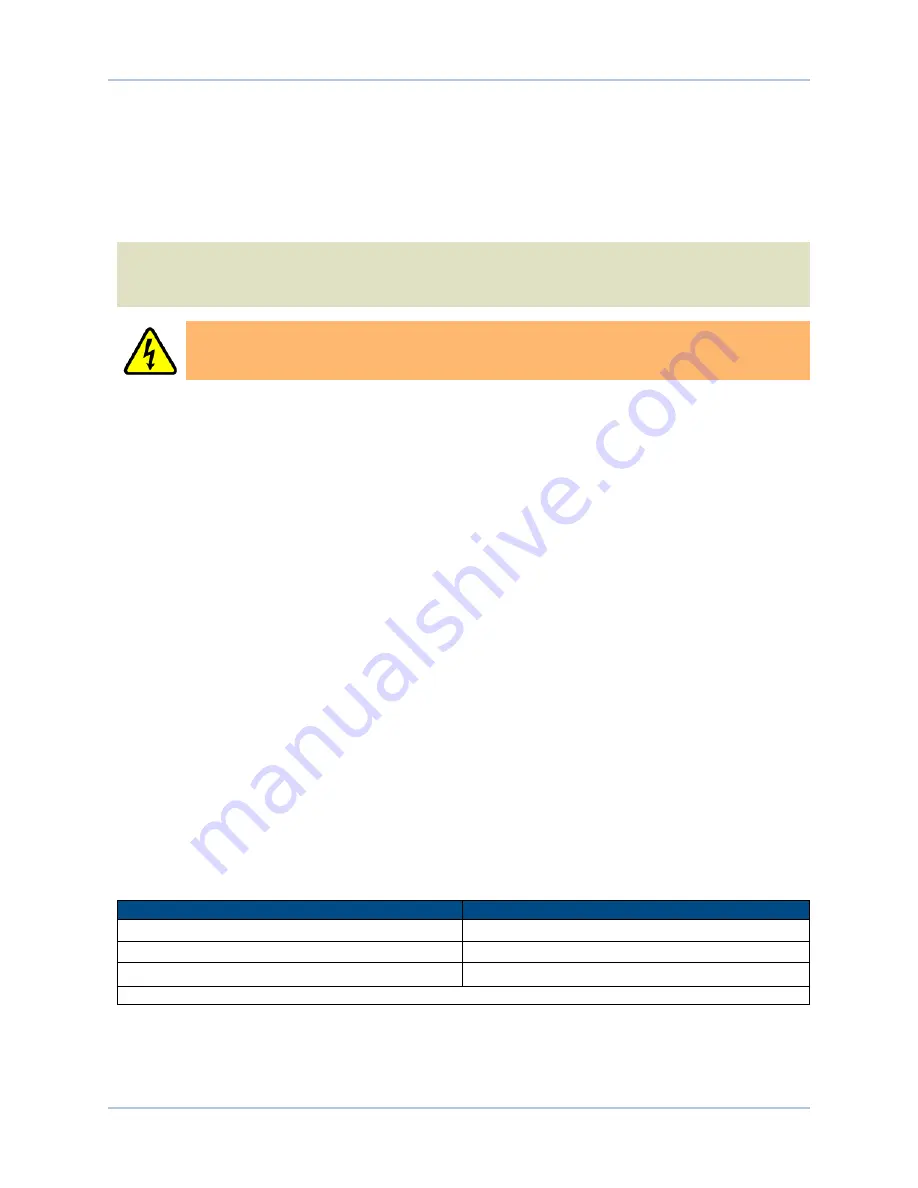
ABL1000 Hardware Manual
Maintenance
Chapter 4: Maintenance
The ABL1000 series stages are designed to require minimum maintenance. Due to the non-contact air
bearing design, there are no friction surfaces or dynamic seals to wear or require lubrication. However, it is
important to clean the bearing surfaces and encoder strips to maintain the accuracy of the stage. This
chapter will detail the cleaning and lubrication process and specify recommended cleaning solvents.
N O T E :
The bearing area must be kept free of foreign matter and moisture; otherwise, the performance
and life expectancy of the stage will be reduced. Always operate the stage with the hard cover and side
seals in place to help keep dirt out.
D A N G E R : To minimize the possibility of bodily injury or death, disconnect all electrical
power prior to performing any maintenance or making adjustments to the equipment.
4.1. Service and Inspection Schedule
Inspect the ABL1000 at least once per month. A longer or shorter inspection interval may be required
depending on the specific application, and conditions such as the duty cycle, speed, and environment.
Monthly inspections should include but not be limited to:
l
Visually inspect the stage and cables.
l
Re-tighten loose connectors.
l
Replace or repair damaged cables.
l
Clean the ABL1000 and any components and cables as needed.
l
Repair any damage before operating the ABL1000.
l
Inspect and perform an operational check on all safeguards and protective devices.
4.2. Cleaning and Lubrication
Clean all air-bearing surfaces and encoder scales to prevent damage to the stage or decreased performance.
Prevent dust build-up from accumulating in the linear motors, encoders, and air-bearing surfaces by blowing
clean, dry, compressed air over the entire stage. Due to the non-contact design, these surfaces operate very
close together, allowing dust to buildup and cause damage.
All encoder surfaces and magnet tracks should be cleaned with isopropyl alcohol. Aluminum hard-coated
metal surface may be cleaned with isopropyl alcohol or acetone. Acetone should not be used on magnet
tracks because it could break down the epoxy that holds the magnets in place.
Table 4-1:
Recommended Cleaning Solvents
Item
Recommended Cleaner
Encoders, Magnets
Isopropyl Alcohol
Hard-Coated Aluminum
Acetone
Granite
Surface plate cleaner
(1)
1. Surface plate cleaner is available from precision granite manufacturers.
www.aerotech.com
Chapter 4
31